Asphalt Goes Hi-tech In Harlow
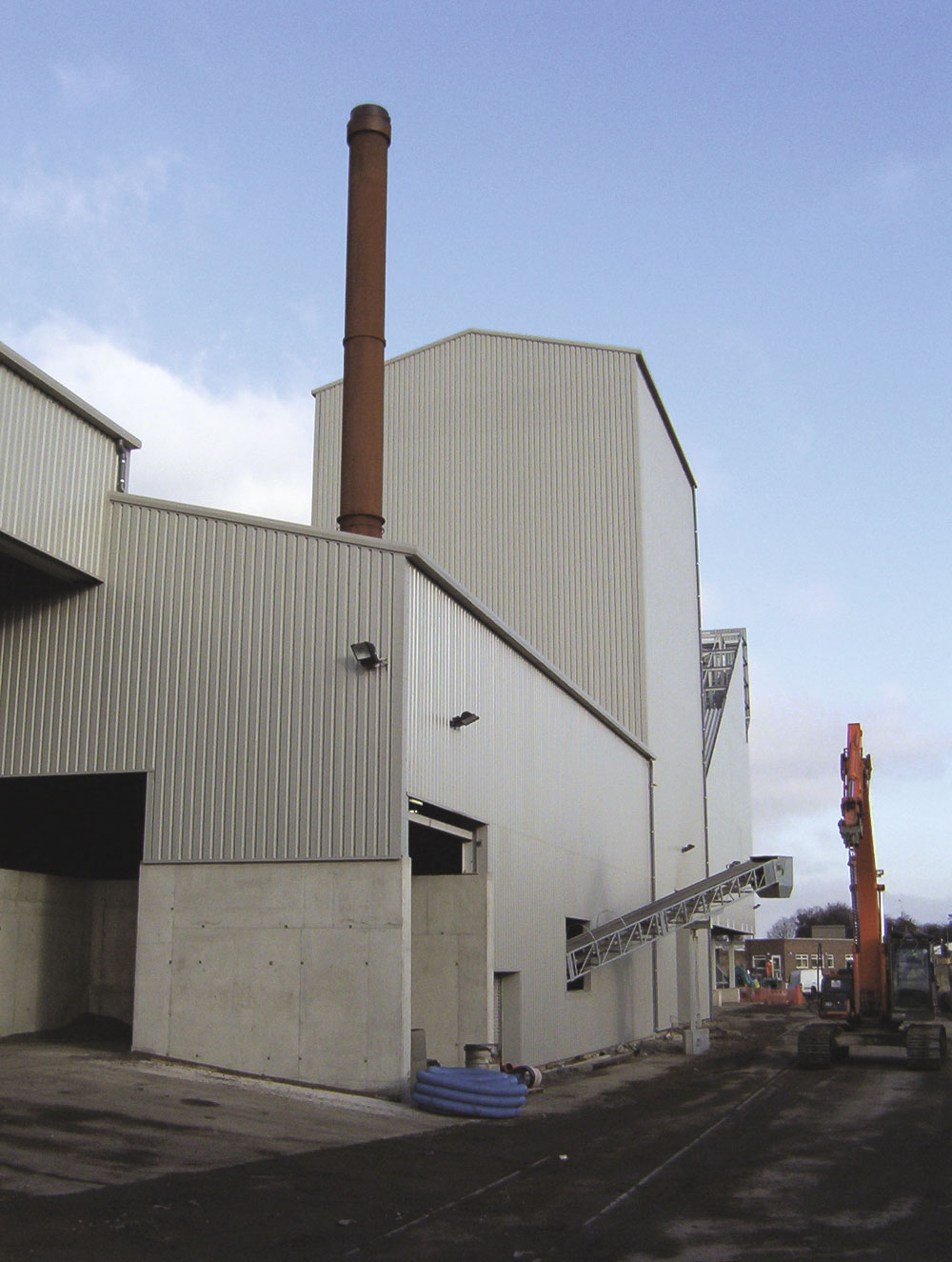
State-of-the-art asphalt plants are no longer just about maximizing production – they need to be energy efficient, quiet and environmentally friendly too. Claire Symes visited a new plant in Essex that meets all these criteria and a few more.
Getting the right quantity of high-quality material to customers at the right time is the main philosophy behind design of most asphalt plants in the UK. But in recent years the focus of new facilities has shifted and now also encompasses a range of environmental issues as well as output performance.
A combination of production and environmental capabilities assembled in a strategic location is behind the recent development of a new Bardon Aggregates asphalt and concrete facility in Harlow. The new asphalt plant was commissioned in October, while the concrete plant is due to open for business in the next few weeks.
The new plant is well located for easy access to the motorway network and is also served by a new railhead that can deliver up to 1,750 tonnes/h of aggregates directly to the site’s aggregate terminal (see box). Harlow’s newest enterprise strengthens Bardon Aggregates’ presence in the south-east and East Anglia through rationalization of their operations at Hoddesdon and Bishops Stortford.
‘Although our Bishops Stortford facility had a railhead, the short-term lease did not lend itself to investment to upgrade the operations. The Hoddesdon site had limited storage space and no railhead,’ said Bardon Aggregates project manager John Edgar. ‘The new plant at Harlow Mill has good access to the M11 and M25 making it ideal for customers who want to collect their materials.’
Harlow Mill’s new KVM plant is capable of producing around 240 tonnes of asphalt an hour and, according to Mr Edgar, has a number of innovative design features that maximize its efficiency. ‘Most Scandinavian production processes give greater consideration to energy consumption and environmental factors than their European counterparts. KVM are based in Denmark and are no exception to the rule,’ he explained.
‘Although KVM are essentially an overseas supplier, they have good service and long-standing technical-support facilities in the UK and that gives added confidence.’
Bitumen delivery is one of the features on the KVM plant that both improves safety and boosts performance. The four 100-tonne bitumen storage tanks are served by a stripping pump to offload the bitumen from delivery tankers. Stripping pumps more closely control the discharging process than the more conventional technique of blowing out.
Bitumen specialists Nynas Bitumen will be supplying Bardon Aggregates’ Harlow Mill plant with bitumen. ‘We supply the plant with three grades of conventional straight-run bitumen and one polymer-modified bitumen — Nypol TS — which is used to produce thin-surfacing materials,’ said Nynas Bitumen sales manager Miles Williamson.
The plant also has the capacity to blend bitumen on site but it is the Nypol TS that offers customers, and Bardon Aggregates, the greatest benefits. ‘Nypol TS has thixotropic properties which allow its viscosity to reduce as energy is added, for example during mixing,’ said Mr Williamson. ‘Once the mixing is complete, the viscosity increases and prevents binder drainage during storage and transportation.
‘This not only improves the end performance of the asphalt material but also removes the need to use costly release agents, that are not particularly environ-mentally friendly, to clean storage areas and trucks after use.’
Other performance enhancements at the Harlow Mill site include full enclosure of the aggregate terminal as well as the concrete and asphalt plants. This not only reduces noise and dust pollution but also helps conserve energy through heat retention. ‘The plant features a number of power-saving devices, including variable-speed drives, which mean it does not have to be run on full power during lighter phases of production,’ said Mr Edgar. ‘There are also auto-shutdown facilities to save energy if the plant is idle for a specific amount of time.
‘Numerous testing points allow the site laboratory to create accurate quality-control records and the use of thermocouple and infrared temperature gauges in combination improves accuracy during production.’
Although the site is badged as a customer-collection Express Asphalt site, the unit also operates a full delivery service under the Bardon Aggregates name. Customers can request material in quantities ranging from just one tonne upwards, allowing the facility to cater for almost every market. ‘The range of bitumen and aggregates stocked at the plant allows us to produce a wide variety of asphalt mixes, including recycled and coloured asphalts, SMAs and thin surfacings,’ said Mr Edgar.
Seven hot-storage silos of varying sizes with a total capacity of 700 tonnes have been installed at Harlow Mill to add flexibility and facilitate rapid turnaround times. These storage facilities will also allow the plant to supply night-time resurfacing contracts, often without having to work outside normal operating hours.
Work on the site’s 250m3/h concrete plant — one of the largest in the UK — is still under way but Bardon Aggregates are already looking to further improve their share of the concrete and asphalt market from their Harlow Mill facility.