Using Your I-Site
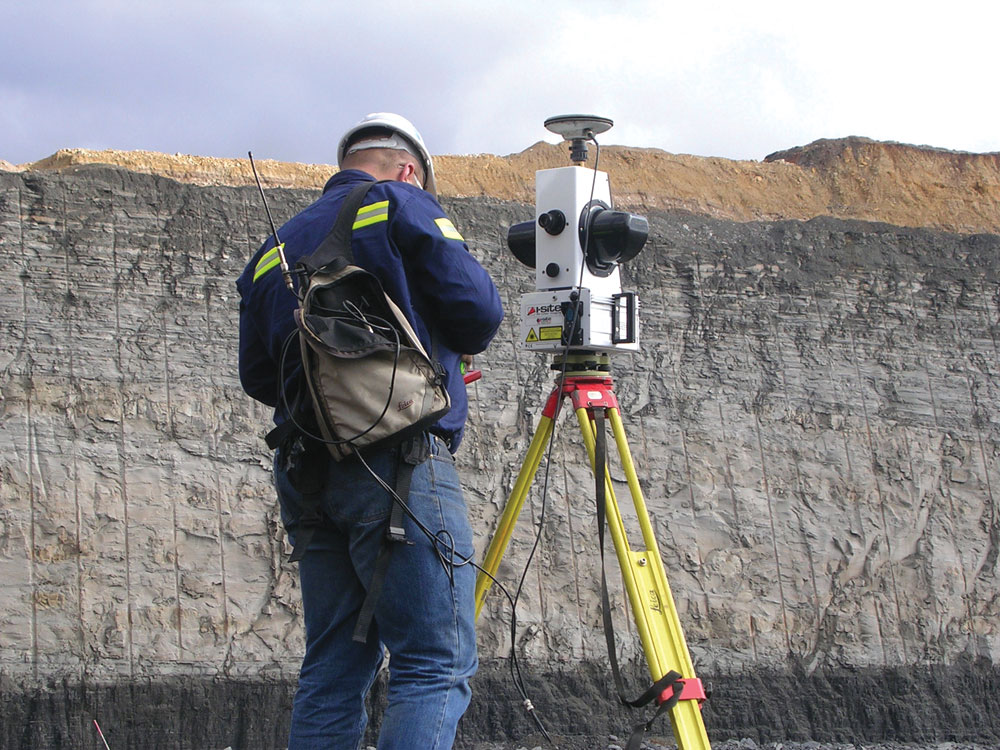
Measuring the benefits of 3D laser scan surveying
Costs, efficiency and safety are the bywords of quarry operators. In difficult economic conditions, it becomes even more critical to improve processes and make the best use of existing resources.
Maptek have been in business for almost 30 years and have supplied mine and quarry technology solutions to customers through boom times and tougher markets – a grounding that helps ensure their products are designed, developed and enhanced with the end-user in mind.
The company developed its I-Site technology in the late 1990s in response to the growing demand for accurate, safe and fast survey and measurement tools. Since then, the 3D laser scanning instrument and scan data processing software have progressed from early prototypes to advanced technology, which directly targets the survey needs of any operation – large or small.
For lean quarry operations, the I-Site hardware–software system provides a solution for processes which need to be completed with as much efficiency and accuracy of results as possible. Open-pit surveying, capturing active and existing highwall faces, analyzing geotechnical data, measuring and monitoring product stockpiles and generating accurate volumes and models, are some of the many applications of the system. Moreover, all this can be done without the need for a complete survey team, while the flexibility of the system allows for the incorporation of data collected by other means, such as aerial photography and GPS units.
Open-pit survey
Driving the length of a pit to survey the extent and record the status of the latest mining activity by traditional methods (total station and GPS units) is a time-consuming and labour-intensive task. Laser scanning significantly reduces this time from days to hours, and powerful processing software means accurate models can be created the same day, in the field if needed. As a result, there is no need to wait for monthly or quarterly ‘flyovers’ – updated data can be at the fingertips of both planning and operational staff within hours.
Maptek’s new I-Site 4400LR multi-sensor laser scanning instrument features a 700m measurement range and patented, simultaneous, panoramic high-resolution imaging technology.
The I-Site 4400LR scanner includes a high-precision alignment telescope and single-axis level compensator, and allows integration with standard survey work flow and external data such as GPS. Recognizing that users require a complete in-field tool, the HHC tablet interface allows for efficient setup, control, data acquisition and survey registration.
The purpose-built panoramic digital colour camera within the 4400LR scanner allows simultaneous acquisition of laser scan data and a 360° high-resolution colour image, which can be automatically rendered over the scan data.
Open-pit and quarry operations generate large amounts of survey data, so it is a distinct advantage that large point datasets can be efficiently interrogated, modelled and manipulated on a desktop PC or field laptop. This allows results to be quickly fed back into the mine or quarry planning process. Historical or commonly accessed data, such as survey stations and mine designs for the same project, can also be maintained.
I-Site Studio software allows projects consisting of hundreds of scans and hundreds of millions of points to be managed inside a single data-engine. The use of 64-bit architecture increases the flexibility in managing laser scan data across multiple projects or multiple data engines.
Latest developments, such as the open-pit update tool, continue to satisfy the industry’s need for measurement quality. The tool allows new data from scans of working areas to be inserted into existing models, with a new model automatically generated to reflect the changes in topography from those scans. The result is a new and updated pit model, created in one step, and without the risk of altering areas that have not changed since the last data collection.
Highwall geology
Scanning a highwall, development face or pit wall provides geologists with an extremely detailed and truly three-dimensional image of their operation. A single scan of a highwall can generally be undertaken in less than 5min and at the same time as performing routine daily or end of month surveys.
Unlike methods that only colour individual points based on a photograph, all of the pixel information is rendered on to a 3D point cloud, and there is no need to calibrate and align a camera to capture images.
Geologists can digitize boundaries, structures and other features directly on to a 3D image in true local grid co-ordinates without any interpolation from 2D to 3D. As the resolution of the photographs is 15 times greater than that of the point data cloud, surveyors can digitize on-screen with I-Site Studio, knowing they can easily swap between intensity and photographic views.
A simple click of the mouse will generate a detailed 3D model from the point cloud for geotechnical interrogation of fault planes or joint sets. Points, polygons or lines can be created directly on to the 3D model for accurate calculation of dips and strikes. The 3D CAD drawings can be exported and combined with other geological information in external databases.
Laser scanning allows an operation to accurately pinpoint the highwall position (compared with traditional methods of GPS pickups with offsets). The scanner provides an accurate x, y, z position of the seam interface – the point where the seam intersects the highwall.
The speed of the laser scanner means that all structures – low wall, high wall, end walls, and bench levels – are generally captured in each scan. The time difference between completing a 180° scan (highwall) and a 360° scan is only a few minutes. The savings are enormous when compared to traditional methods, where the setting up of reflectors and targets, and taking many shots to cover a small area, is compounded by the hours of post-processing required to extract relevant geological information, such as joint sets and faults.
With laser scanning, an enormous amount of data is collected in a very short period, speeding up field work. Moreover, the operator does not have to set up close to the high or low wall, so is not exposed to any increased risk while scanning.
Blast profiling
Laser scanning is a very efficient tool for blast profiling. Blasting is a potentially hazardous component of surface mining and quarrying, so designing and setting the blast requires careful assessment of the face and bench to identify potential problem areas, such as the presence of seams, voids or geological irregularities. The detail and immediacy of laser scans means staff have accurate 3D models and photographs that can be examined, measured and digitized on screen. Since the scans and photographs can be captured at the same time as the pit surveys, time is saved on site inspections.
Data captured by the scanner pre and post blast allows operators to view and analyse post-blast results, watch for changes in surfaces, and carry out geotechnical surveys in inaccessible areas. Scanning the blast profiles allows operators quickly to get accurate data to analyze how effective a cast blast has been, which aids in future drill and blast designs.
Laser scanning is a very useful tool for determining the volume of lost and gained material. Scans are merged into a full 3D triangulation using I-Site Studio’s ‘fusion surface’, which is then compared to previous results using the ‘distance from surface’ option, highlighting where changes have occurred. In addition, the triangulation model can be used to monitor any subsidence or other geotechnical issues.
Stockpiles
By definition, most quarries extract stone for further processing. It is important to monitor both permanent and transitional (loading) stockpiles to keep track of cost–profit ratios, especially in times of fluctuating commodity prices. Laser scanning represents an efficient and safe means of recording and updating stockpile volumes. Large stockpiles can be surveyed quickly and easily in 360° sweeps with an 80° vertical field of view.
Laser scanning overcomes situations that often occur on site, such as failure of GPS units to work when under or around gantries, the constant movement of heavy vehicles in the stockpile zone, and moving or fixed gantries/conveyors. The I-Site instrument standpoint can be either vertical or horizontal, and when access to stockpiles is restricted or forbidden, due to feed and draw mechanisms or the unstable nature of the material, scanning from a remote standpoint addresses the safety issue without compromising the accuracy of the data captured and the resultant volumes.
Laser scanning can deliver end-of-period stockpile reports in less time, taking advantage of the laser scanning methodology as well as improved reporting workflow, while other benefits include the measurement of material samples to accurately calculate material density for load optimization.
Modelling, volumes and density analysis
To calculate stockpile volumes, a topographic filter is used to thin the millions of data points and remove unwanted, obscuring scan points. The filter grid size reflects the stockpile size and the level of detail required. Further manual deletion of unwanted points may still be needed. A topographic triangulation is then created, and the stockpile volume is calculated.
After determining the volume, the density is needed to calculate the weight of the material in the stockpile. Truck scanning can be used to determine material density. An empty truck tray is modelled for a base and then the material is scanned and weighed. The density is calculated as follows: D = W/V. Results are available quickly, including volume results, density readings and screen captures. Video output can also be generated for use in formal presentations.
Summary
Safety, efficiency, reliability, accuracy and speed are all factors that contribute to the overall success of a quarry operation. New technology, such as the laser scanning system from Maptek, will continue to deliver these outcomes.