Reducing water waste with Warman pump centrifugal seals
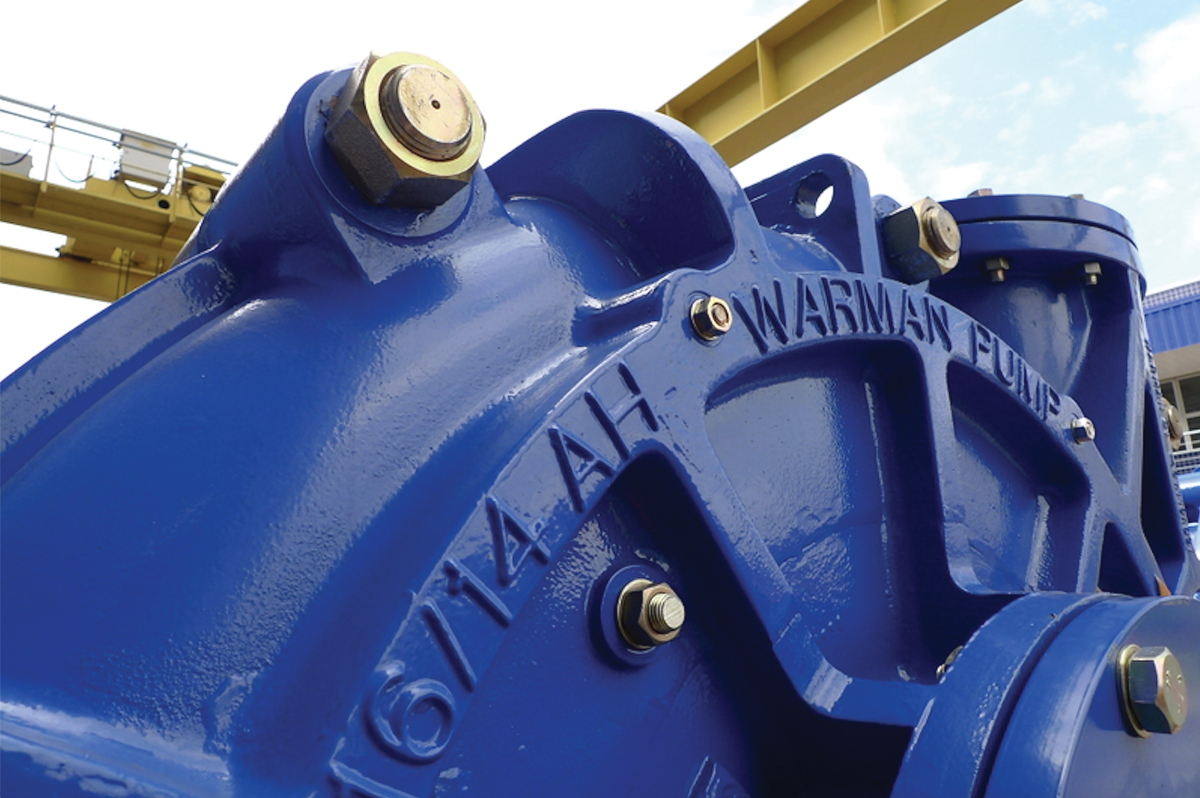
First published in the August 2020 issue of Quarry Management as Sustainable Sealing
Easy to maintain and considerably less expensive to operate, centrifugal (or expeller) seals offer a more sustainable alternative to traditional gland sealing on Warman pumps
Although water is a significant operational cost at most mines and quarries, pump centrifugal seals are often overlooked despite the immense benefits associated with eliminating the need for gland water for pumps.
With many pumps consuming tens of thousands of litres of water per day, centrifugal seals can significantly reduce operating costs, free up clean water for other critical uses and enhance the project’s social license to operate.
In remote areas, the supply of suitable gland water may be very costly due to the need for sinking boreholes and pumping long distances by pipeline back to the plant, while competing industrial, agricultural and residential requirements can complicate the approval of the mine or quarry.
In addition to saving vast quantities of water, centrifugal seals eliminate the need for the extensive infrastructure required to deliver a controlled supply of clean water to dozens of pumps across a mine or quarry. This significant reduction in capital investment and equipment maintenance combines with the elimination of wasted water to produce a much lower total ownership cost for Warman pumps that use centrifugal seals, when used in the right application.
In many processes, it is imperative to avoid introducing any water back into the slurry since it then costs more to remove it later. Gland sealing does rely on some leakage of water back into the slurry whereas centrifugal sealing does not.
How do slurry pump centrifugal seals work? A centrifugal seal is a dynamic seal that operates when the pump shaft is rotating but has no sealing effect when the shaft is stationary. It consists of an ‘expeller’, a vaned disk connected to the pump shaft, not entirely dissimilar to an impeller. The expeller is positioned behind the impeller and is separated from the main pumping cavity by a wall, or ‘expeller ring’. As long as the pump is running above a minimum speed, the expeller hydraulically seals the shaft by rotating with the impeller, generating a differential pressure gradient that forces the slurry away from the shaft seal and back towards the main volute cavity.
An important consideration for centrifugal seals is the choice of wear-resistant material, as the inner face of the seal is directly exposed to the slurry. Centrifugal seals for Warman pumps can be manufactured from a variety of materials to suit different applications, although testing has shown that Weir Minerals’ Ultrachrome A05 high chromium white iron alloy achieves superior wear life in most abrasive and corrosive conditions.
A more recent innovation is the Warman Hi-Seal next-generation centrifugal seal. It features an increased diameter, which results in a larger differential pressure being created when in operation. This higher differential pressure results in a better sealing experience and allows even larger pump sizes to seal effectively. Warman Hi-Seal is now the standard centrifugal seal offering for most pumps.
When not to use centrifugal seals
While centrifugal seals are suitable for the vast majority of pumps operating in most mines and quarries, there are a few circumstances which make gland or mechanical sealing a better option.
Centrifugal seals rely on shaft speed and only work when they are generating a higher pressure than the impeller. Therefore, they are unsuitable for applications with varying speed of operation, total head and suction pressure. Filter-press pumps, dewatering pumps managing variable sumps, and pumps that are frequently switched on and off are all unsuited to this dynamic sealing method.
Similarly, because of the leakage risk while the shaft is not rotating, centrifugal seals have specific packing and lubrication requirements and are unsuitable for pumps handling dangerous chemicals.
Centrifugal seals do consume a small amount of additional energy compared with glands. While this is much lower than the cost of water for small pumps, the cost of power for larger pumps makes centrifugal seals a poor choice. For this reason, Weir Minerals does not offer centrifugal seals on Warman pumps with a discharge diameter greater than 250mm.
Calculating gland water costs
The costs associated with the use of water to flush the gland of a slurry pump can be split into two components, the supply cost and the removal cost. The former depends on the type of pump, its size and gland type; the latter depends on the particular process and commodity being handled.
Using the following formulas included in Warman Technical Bulletin #32: Total Ownership Cost model for slurry pumps, an approximate cost of gland water consumption can be determined.
First, gland water has to be supplied at a supply pressure which is generally 70kPa above the discharge pressure of the pump. The power required to deliver the water to the gland (Pg) can be approximated by:
Pg = 0.02 x (H + 7 / SGm) x Qg
where
SGm = specific gravity of slurry mixture
H = total head developed by pump (m slurry)
Qg = gland water flowrate (litres/s)
The energy cost (cge) is then:
cge = Pg x ce x ho
where
ce = unit power charge (£/kWh)
ho = total operating time (h/year)
The actual consumption cost for the water then needs to be added to the energy cost. The total water consumption cost (cc) is:
cc = 3,600 x Qg x cgw x ho
where
cgw = cost of water supply (£/litre)
With tightening environmental standards in some cases requiring complete liquid containment on site, any slurry dilution can incur substantial cost penalties. The total cost of unwanted dilution water (cd) is:
cd = 3,600 x Qg x crw x ho
where
crw = cost of removing the water (£/litre)
From this the total service water cost (Cw) can be calculated by summing the three terms:
Cw = cge + cc + cd
- Subscribe to Quarry Management, the monthly journal for the mineral products industry, to read articles before they appear on Agg-Net.com