Pumping Installations
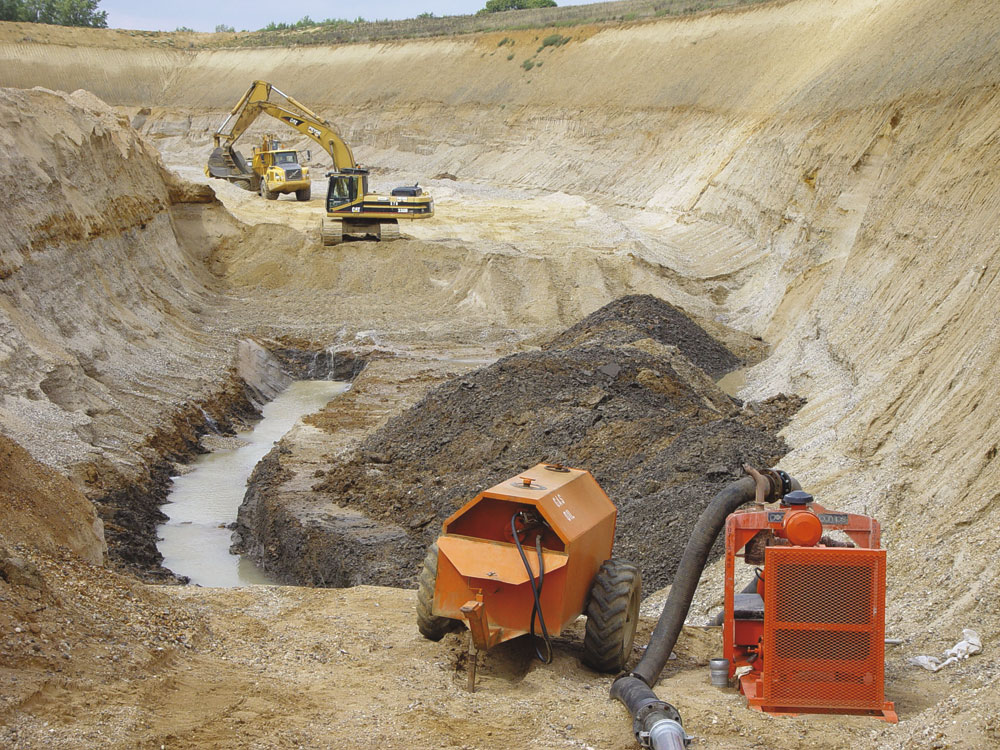
By Roger Lindley, international marketing consultant
With the proliferation of pump types and manufacturers it is not surprising that many quarry mangers stick with the tried and proven, even though they probably know that the chosen option may not be the most practical, reliable or economical. Given that most quarries have to pump hundreds of thousands of tonnes of water a year, saving just a fraction of a penny per litre can deliver significant cost savings over the course of a year.
Today, quarry managers also have to take into consideration other facets of water and slurry management. Environmental issues, such as engine emissions and sound levels, need to be addressed and safety is always a consideration. In some quarries, failure of the pumps can put at risk valuable assets as well as lives of personnel.
To maximize the economic return on dewatering it is necessary to consider various criteria including the volume of water, variations in flow, the amount of solids in suspension, head height, total distance of discharge lines etc. However, pump choice remains the most critical consideration.
Different types of pumps
In general there are three main types of pumps suitable for use in quarry applications:
- Diesel- or gas oil-driven self-priming centrifugal pumps.
- Electric submersible pumps.
- Hydraulic submersible pumps.
Electric submersible pumps, on the other hand, are virtually silent in operation, produce no emissions and can be moved from one location to another. However, they do need a power supply, which means landlines or a generator. Submersible pumps generally have a good reliability record and require little, if any, day-to-day maintenance. When they do fail, however, it can be a catastrophic failure requiring a complete rebuild.
The hydraulic submersible pump is a good option in situations where the supply of electricity to the application is difficult or cost-prohibitive. Because hydraulic submersibles are usually driven by diesel engines, they can offer the same flexibility as diesel-driven centrifugal pump sets without the difficulties associated with suction lifts of greater than 7.5m. However, being diesel engine driven can create noise and pollution and, of course, they need regular refuelling.
Considering the various options available, the range of manufacturers, and product cost, it is easy to see why most quarries choose from the first two options rather than the hydraulic submersible pump. Diesel-driven centrifugal pump sets remain a popular option because they have been used extensively and there are a great number in operation around the world. This is a highly competitive market, which helps maintain purchase costs at a low level.
However, in terms of product development, electric submersibles have benefited from technological innovations. Submersibles such as those made by Grindex have features that ensure greater reliability and maximum performance. A common problem with electric pumps was always the risk of the impeller working in the wrong direction, which reduces pump performance by over 40%. Rotation-sensing devices eliminate this. In the past submersible pumps could quickly overheat during snoring but various developments allow some brands to run dry for extended periods. Improved seals, impeller design and materials have also contributed to improved performance.
A complaint sometimes levelled at the diesel-engine-powered centrifugal pump manufacturers is that, although the power pack has been developed, the basic pump design has remained unchanged over many years. Some of the developments that have taken place are a result of having to meet changing regulations — particularly regarding sound levels and emissions. Manufacturers are being forced by regulation into being more aware of the environment — something that is very high on the agenda for every quarry manager and probably one reason why electric submersible pumps have gained a rapid share of the market.
Today, with the use of Tier II engines and sound-attenuation technology, diesel-engine-driven pump sets are generally environmentally friendly in terms of noise and pollution as well as being more economical to run due to modern engine-management systems. As a result, refuelling times have also been extended.
Moreover, new entrants to the market, such as Pioneer Pumps, are challenging traditionally held beliefs in pump-set design through greater use of computer-aided design and development techniques to maximize performance efficiency and extend the pump’s operational parameters to achieve an improved ability to handle variations in demand. A benefit of this investment in research and development is that while a Pioneer 6in pump with a fully sound-attenuated canopy is smaller than a competitor’s 8in pump, it is capable of outperforming it.
Obviously, the more compact the pump set, the greater the saving in owning and operating costs. As packaging technology improves more pump sets are being offered in smaller sizes, yet these are able to match or even surpass the performances seen in older pump designs.
Importance of pump performance flow charts
A problem that exists within the industry is many customers’ deep-rooted acceptance of past practice. Ask many plant managers what pump is required for a given situation and they will invariable say a 4in, 6in, 8in etc, because in the past the flow rate possible with each size was within certain ranges. However, that situation is different today.
There is also the age-old dilemma of what to do about variable flow rates. Some managers install a pump set to cope with the maximum expected load, while others opt for a small pump set to cope with day-to-day demand but have a secondary pump on standby for when additional pumping capacity is needed. The former means over- powering with higher fuel and maintenance costs, while the latter results in an expensive pump lying idle for most of the time.
Whether looking at electric submersibles or diesel-driven surface-mounted pumps, the correct use of pump flow charts can help identify another option — a pump set that runs at optimum fuel/flow efficiency while having sufficient power in reserve for changes in demand. For a long time some manufacturers did not make their flow charts readily available because they allow for better product performance comparisons. Today they are generally available, if not always easy to read and interpret, and they do assist in selecting the most cost-effective pump set when comparing many types of pumps.
Electric vs diesel economics
Owing to the inherent design of the electric submersible pump, pumping larger flows or higher heads requires higher power consumption, which in turn means heavier power cables from larger generator sets or a fixed power supply. This issue restricts the flexibility of the pumps. For example, submersible pumps operating at 50Hz (1,475rpm) deliver an almost fixed performance along a single curve. When a quarry is deepened, the user usually has to resite the pump and lengthen the cables in order to maintain operation. However, the pump then has to overcome additional static lift and, unless it can be speeded up, this additional head is offset by a lower flow.
With diesel-driven pumps this is not the case. Provided the pump is not selected to operate at its maximum performance when first supplied, the operator has the option to increase the performance of the pump by increasing its speed. This action would be based upon the pump manufacturer offering a suitable sized engine for the pump covering the entire operating range, including its maximum safe working performance.
The hydraulic submersible offers the best of both worlds if sized appropriately. Being diesel engine driven, the pump set offers a level of flexibility not available with electric submersibles. However, there are drawbacks. The efficiency losses through a hydraulic submersible are higher than both electric submersibles and diesel-driven centrifugal units, which generally means larger power packs.
Nevertheless, with modern technology a hydraulic submersible pump is a very cost-effective alternative to electric submersibles or above-ground pumps, such as diesel-driven sets, and when used in the correct quarry application it is an option well worth considering.
Hydraulic submersibles can be used with environmentally sensitive oils, thereby overcoming traditional problems with potential leakages of the power-transmission fluids. Modern oils from companies such as Shell or BP provide quarries in environmentally sensitive areas with a cost-effective alternative to laying and maintaining long power cables.
Bottom-line economics
Because each quarry has different pumping requirements, it is not possible to apply a common formula. In the past this required lengthy calculations but today there are computer programs readily available to help managers select the most cost-efficient solutions, taking into consideration the total pump line and composition of the material to be pumped.
These computer programs are not expensive and most are very easy to use. At the most basic level they simply require answers to various questions from which to calculate efficiency, depending on the discharge pipeline diameter, whether new or old pipe, distance, gradients, bends etc. The programs will calculate the required optimum pumping pipeline pressure to prevent the settlement of solids. Changing certain criteria, eg from an old iron pipeline to a new material such as polypropylene, immediately shows the changes in efficiency. Similarly, with the re-routing or excavation of a trench to reduce gradients, managers can evaluate any number of alternatives to allow a decision to be made on the best long-term solution. For example, excavating a trench to eliminate a gradient will be the most economical solution over a period of time depending on the discharge volume.
Many pump manufacturers also produce pump-selection software and all companies have in-house expertise available to help managers achieve the most economical solution. However, these are obviously restricted to a company’s own particular product range.
The importance of ‘total pump-line planning’ cannot be overemphasized. Old, rusted discharge pipes and excessive bends and gradients quickly increase pump set demands. Replacing or re-routing discharge lines may require an additional upfront cost but will deliver significant savings in pumping requirements and ongoing related energy costs.
However, only the quarry manager knows the likely future demands on the quarry, changes that will impact on pipelines, availability of power supplies etc. Computer programs, flow charts and other information can make a positive contribution and make the calculations easier, but ultimately only the quarry manager with his or her local knowledge can decide on the most economical solution.
Pumping costs are an unrecoverable expense but a necessary one to ensure that a quarry is workable and that equipment and personnel are able to work in a drier, safer environment. However, with detailed planning and recognition of new product designs and developments that supersede deep-rooted beliefs, it is possible to drastically reduce dewatering and pumping costs.