Mill Fan Upgrade for Hanson Cement
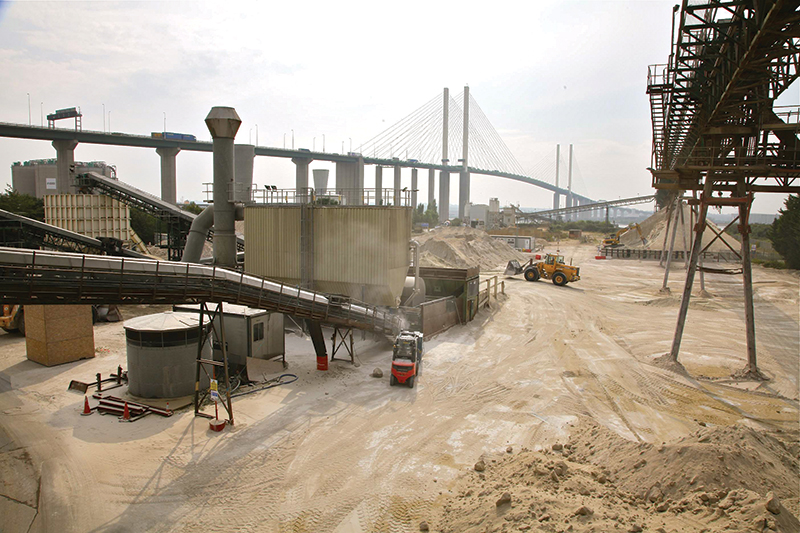
First published in the October 2015 issue of Quarry Management as Perfect Harmony at Purfleet
Siemens fan upgrade at Hanson Cement’s Purfleet plant saves energy and reduces the company’s carbon footprint
A fan upgrade by Siemens at Hanson Cement’s highly productive Purfleet plant has resulted in energy savings of more than 36%, with payback on the investment anticipated to be well under two years.
Situated next to the river Thames, in Essex, Purfleet Works is capable of producing around 1 million tonnes a year of Regen – a cement replacement in ready-mixed and precast concrete which is manufactured from ground granulated blast-furnace slag. The works consist of two closed-circuit ball mills and a Loesche vertical grinding mill. It was Mill 3 that required the upgrade, as the existing mill fan was a fixed-speed unit using a 1MW, 11kV, slip-ring machine running at around 980kW. The airflow was continuously at full speed and was controlled by a damper. The fan’s design airflow was 350,000m3/h, but the system was damped to the operational requirement of approx 241,000m3/h.
As Hanson Purfleet’s electrical engineer, Dave Jackson, explained, the mill upgrade was part of a more general review Hanson Cement were making of all of their sites: ’We were looking to make energy savings around the plant and a survey had recommended a new drive and motor for this mill. The Siemens solution means we are now running with the damper open 100% of the time, yet actual energy consumption has dropped by around 360–400kW.’
Siemens’ total engineered solution centred around the integrated drive systems (IDS) concept, which ensures that all products within the drive system are as integrated as possible, supported by Siemens both in specification and throughout their life cycle. By optimizing the drive system to the highest degree of performance, and by acquiring data through monitoring that system, the best operational performance can be achieved.
For Mill 3, this meant replacing the fixed-speed fan with a 1,000kW Sinamics Perfect Harmony 11,000/4,160V medium-voltage (MV) converter, installed and commissioned to link with existing Siemens process control systems at the plant. A new Siemens MV 1,000kW, 4,160V, six-pole motor was also installed along with new motor cable and a modified motor base (the bed plate was raised by 60mm). Siemens were able to provide the full turnkey solution.
Perfect harmony
According to Siemens, every element of the Sinamics Perfect Harmony cell-based drive range is engineered to maximize productivity and protect a customer’s process in a way that other drives are unable to do. Its modularity is said to allow for a scaleable solution capable of achieving near-100% reliability and 99% availability, two key factors for a busy plant such as Purfleet.
Benefits of the upgrade have included:
- greater productivity through optimized speed and process performance
- improved flexibility, with faster run-up/run-down times
- standardization, reduced size and line attendance
- increased amount of pre-emptive maintenance information
- a significantly reduced total cost of ownership over the product’s life cycle.
Dave Jackson continued: ’It took about a month before we could clearly identify all the changes in running costs, but we were very pleased with the whole system, and more savings were made than originally anticipated. A follow-up visit by Siemens led to even further savings being made using the new drive system and the entire project was completed on time and within budget.’
The annual savings to Hanson from the upgrade have been estimated at £175,000 to £200,000.
Siemens minerals account development manager, Gary Chapman, said: ’This upgrade proves that by using the appropriate software and with Siemens’ knowledge of integrated processes and applications, significant savings can be made while enhancing the overall life cycle of the plant.’
Being able to address a reduction in energy usage and increase plant availability have become key targets for industrial companies. Hanson Cement have been able to reduce their carbon footprint at Purfleet by 1,487 tonnes since the new system was installed last year and are continuing to make further savings.
Steve Hall, Hanson’s national operations manager for Regen, concluded: ’The project was a great success, with the new drive and motor enabling us to reduce drive speed and lower power consumption by approximately 37%. We are continuing to save about 4.5Wh/tonne on our total process with this one fan drive, and these energy savings represent a rapid return on investment for us.’
For further information visit: www.siemens.co.uk/industry
- Subscribe to Quarry Management, the monthly journal for the mineral products industry, to read articles before they appear on Agg-Net.com