Customized Control
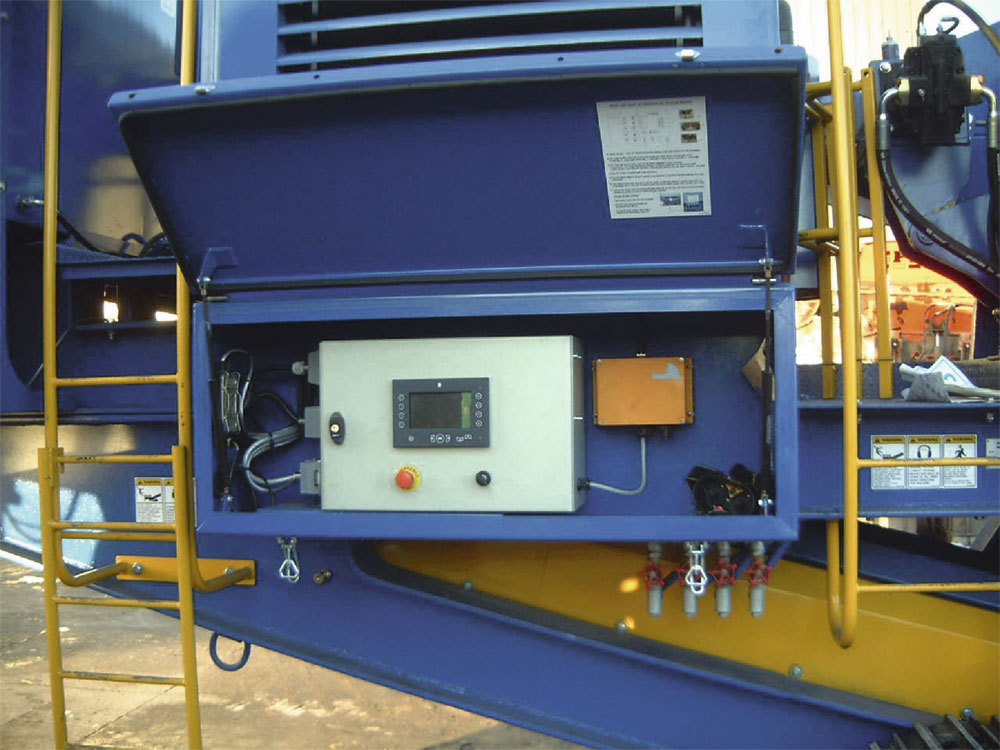
PLUS+1 CANbus technology provides crushing performance benefits
The author, Eddie Phillips, is technical sales support manager with Sauer-Danfoss, Mobile Electronics Division
With more than 40 years’ experience in off-road equipment and over 30 years in mobile electronics, international manufacturers Sauer-Danfoss have applied the company’s expertise in engineered hydraulic and electronic systems for mobile equipment to help OEMs increase efficiency and cost-effectiveness.
The result is PLUS+1, an innovative system that allows mobile plant and equipment manufacturers to customize electronic machine control with the exact functions required. With its powerful programming environment and easy-to-use software tools, as well as newly developed micro-controllers, input/output (I/O) modules, graphical terminals and joysticks, the PLUS+1 system offers equipment design engineers the ability to easily add one capability after another to develop their own control and monitoring network with features that meet users’ specific operating needs.
This mix-and-match system approach allows for custom configuration and precise tuning of work and propel functions, such as speed, position and pressure control, engine anti-stall and automotive propel control. Typical applications include quarrying, agricultural, construction, forestry and materials-handling equipment, as well as utility vehicles and road-building plant.
The foundation of the PLUS+1 CANbus network is a product line of durable, stackable micro-controllers and I/O modules that can be easily scaled to meet machine requirements. The powerful PLUS+1 GUIDE (Graphical User Integrated Development Environment) allows a design engineer to quickly build customized applications from a library of software control objects, including diagnostic tools and service interfaces. This ready-to-fit platform reduces cost and development time to maximize productivity and bring a superior machine more quickly to market.
CANbus technology has been used in automotive engineering for nearly two decades, having been developed as a solution to meet the increasing wiring demands that ever-more complex controls (ABS, traction control, ride control, GPS, power seats etc) place on the size of the wiring harness. Without networking technology such as CANbus, the wiring harness for a modern car would add considerable weight and be practically impossible to route through the bulkheads and doorposts.
In the mid-1980s Bosch wrote the specification for a Controller Area Network, referred to as CAN or CANbus. This was a serial communication protocol that allowed the transmission of information using two wires. The utility of a two-wire bus meant that this system rapidly caught on and has spread to many mobile and industrial environments. Today PLUS+1, Allen-Bradley’s DeviceNet and Parker’s CANkingdom are all examples of higher-layer protocols of CANbus. The flexible nature of the PLUS+1 user-configurable software means that it can be configured to work with most protocols that use the CAN 2.0b format.
More recently, Sauer-Danfoss formed a partnership with JMG Systems Ltd, based in Omagh, Northern Ireland, to design and develop a PLUS+1 control system for use on the new Fintec 1080 cone crusher. JMG Systems have over 20 years’ experience in providing control and cabling solutions to the quarrying industry, with a reputation for manufacturing high-quality and robust control solutions for this market.
Using the PLUS+1 GUIDE software in conjunction with the specialist knowledge of quarry applications held by JMG Systems’ engineers, a complete control system was developed that not only controls all of the Fintec 1080’s hydraulic functions to provide optimum crusher control, but also provides an interface to the engine to both control and monitor all engine functions. The system also uses a second dedicated CAN channel to interface to a Hetronic radio-control system that is used to track the machine. The use of the DP600 graphical terminal provides the operator with a vastly improved interface that allows automatic machine start-up and shutdown. The powerful control system closely monitors the machine and records in its memory any errors or machine faults that occur, allowing improved response from service engineers in the event of a problem.
At the heart of the system is the graphical terminal, which has been specially developed by Sauer-Danfoss to be used in mobile machinery with both cab and cab-less installations. The device utilizes ‘soft keys’ at the side of the screen rather than a touch screen, as well as the latest TFT (Trans-Flective Technology), which has the benefit of making the display clear and legible in even the brightest sunlight. The soft keys change their function depending on which screen the operator is in, and there are several simple screens that provide the operator with an intuitive and easy-to-use interface.
Using bespoke graphics designed by JMG Systems, the system provides the operator with logical screens to follow from machine start-up. As the system is powered up, the operator can choose manual or automatic start modes and adjustment screens for close-side setting and belt control. A maintenance screen is available to service engineers that allows additional controls and information to be accessed. The system has a real-time clock designed to log the number of hours the machine has been crushing, the number of hours the engine has been running and the reasons for the last 10 machine shutdowns. The system also offers intelligent error-handling, including immediate shutdown for critical problems, such as the loss of engine oil pressure, or delayed shutdown for less-critical problems such as an air-filter blockage.
Initial tests of the system have yielded positive feedback with improved ease of use for the operator and an anticipated increase in machine efficiency as service engineers and operators are better informed about the machine status and any faults that may occur. According to Sauer-Danfoss, the system should provide many benefits from the owner, operator and service perspectives.
Sauer-Danfoss Ltd, Cheney Manor, Swindon, Wilts SN2 2PZ; tel: (01793) 530101; fax: (01793) 430347
The author, Eddie Phillips, is technical sales support manager with Sauer-Danfoss, Mobile Electronics Division
With more than 40 years’ experience in off-road equipment and over 30 years in mobile electronics, international manufacturers Sauer-Danfoss have applied the company’s expertise in engineered hydraulic and electronic systems for mobile equipment to help OEMs increase efficiency and cost-effectiveness.
The result is PLUS+1, an innovative system that allows mobile plant and equipment manufacturers to customize electronic machine control with the exact functions required. With its powerful programming environment and easy-to-use software tools, as well as newly developed micro-controllers, input/output (I/O) modules, graphical terminals and joysticks, the PLUS+1 system offers equipment design engineers the ability to easily add one capability after another to develop their own control and monitoring network with features that meet users’ specific operating needs.
This mix-and-match system approach allows for custom configuration and precise tuning of work and propel functions, such as speed, position and pressure control, engine anti-stall and automotive propel control. Typical applications include quarrying, agricultural, construction, forestry and materials-handling equipment, as well as utility vehicles and road-building plant.
The foundation of the PLUS+1 CANbus network is a product line of durable, stackable micro-controllers and I/O modules that can be easily scaled to meet machine requirements. The powerful PLUS+1 GUIDE (Graphical User Integrated Development Environment) allows a design engineer to quickly build customized applications from a library of software control objects, including diagnostic tools and service interfaces. This ready-to-fit platform reduces cost and development time to maximize productivity and bring a superior machine more quickly to market.
CANbus technology has been used in automotive engineering for nearly two decades, having been developed as a solution to meet the increasing wiring demands that ever-more complex controls (ABS, traction control, ride control, GPS, power seats etc) place on the size of the wiring harness. Without networking technology such as CANbus, the wiring harness for a modern car would add considerable weight and be practically impossible to route through the bulkheads and doorposts.
In the mid-1980s Bosch wrote the specification for a Controller Area Network, referred to as CAN or CANbus. This was a serial communication protocol that allowed the transmission of information using two wires. The utility of a two-wire bus meant that this system rapidly caught on and has spread to many mobile and industrial environments. Today PLUS+1, Allen-Bradley’s DeviceNet and Parker’s CANkingdom are all examples of higher-layer protocols of CANbus. The flexible nature of the PLUS+1 user-configurable software means that it can be configured to work with most protocols that use the CAN 2.0b format.
More recently, Sauer-Danfoss formed a partnership with JMG Systems Ltd, based in Omagh, Northern Ireland, to design and develop a PLUS+1 control system for use on the new Fintec 1080 cone crusher. JMG Systems have over 20 years’ experience in providing control and cabling solutions to the quarrying industry, with a reputation for manufacturing high-quality and robust control solutions for this market.
Using the PLUS+1 GUIDE software in conjunction with the specialist knowledge of quarry applications held by JMG Systems’ engineers, a complete control system was developed that not only controls all of the Fintec 1080’s hydraulic functions to provide optimum crusher control, but also provides an interface to the engine to both control and monitor all engine functions. The system also uses a second dedicated CAN channel to interface to a Hetronic radio-control system that is used to track the machine. The use of the DP600 graphical terminal provides the operator with a vastly improved interface that allows automatic machine start-up and shutdown. The powerful control system closely monitors the machine and records in its memory any errors or machine faults that occur, allowing improved response from service engineers in the event of a problem.
At the heart of the system is the graphical terminal, which has been specially developed by Sauer-Danfoss to be used in mobile machinery with both cab and cab-less installations. The device utilizes ‘soft keys’ at the side of the screen rather than a touch screen, as well as the latest TFT (Trans-Flective Technology), which has the benefit of making the display clear and legible in even the brightest sunlight. The soft keys change their function depending on which screen the operator is in, and there are several simple screens that provide the operator with an intuitive and easy-to-use interface.
Using bespoke graphics designed by JMG Systems, the system provides the operator with logical screens to follow from machine start-up. As the system is powered up, the operator can choose manual or automatic start modes and adjustment screens for close-side setting and belt control. A maintenance screen is available to service engineers that allows additional controls and information to be accessed. The system has a real-time clock designed to log the number of hours the machine has been crushing, the number of hours the engine has been running and the reasons for the last 10 machine shutdowns. The system also offers intelligent error-handling, including immediate shutdown for critical problems, such as the loss of engine oil pressure, or delayed shutdown for less-critical problems such as an air-filter blockage.
Initial tests of the system have yielded positive feedback with improved ease of use for the operator and an anticipated increase in machine efficiency as service engineers and operators are better informed about the machine status and any faults that may occur. According to Sauer-Danfoss, the system should provide many benefits from the owner, operator and service perspectives.
Sauer-Danfoss Ltd, Cheney Manor, Swindon, Wilts SN2 2PZ; tel: (01793) 530101; fax: (01793) 430347