Compressing Costs
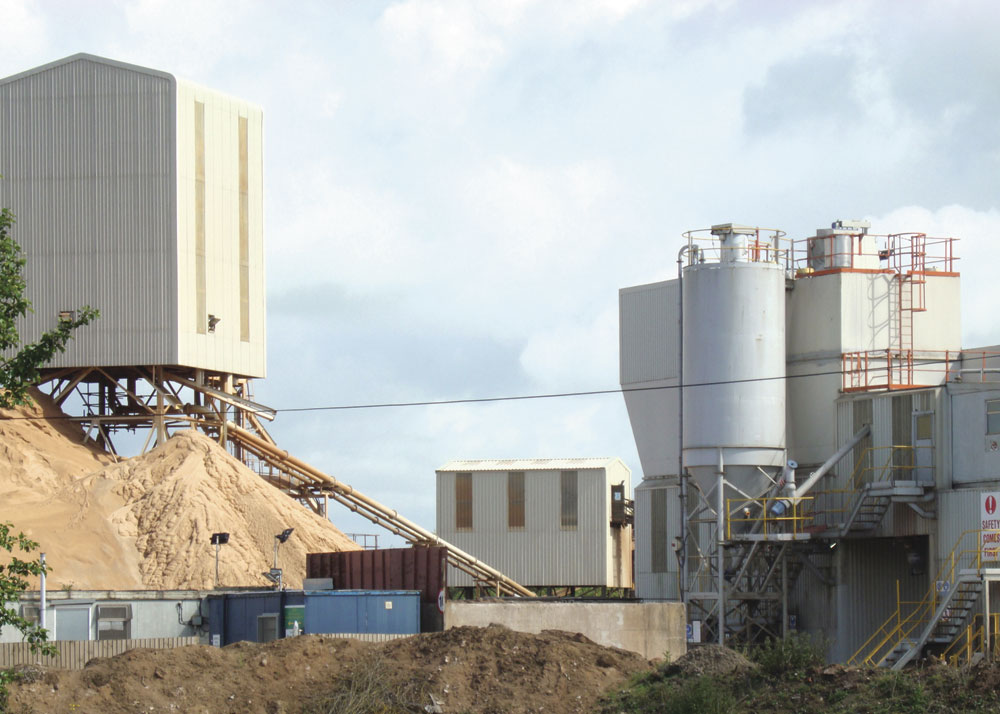
Aggregate producer achieves 61% energy saving on compressed air at dry silo mortar plant using EnergAir intelligent air-management system
A compressed-air audit conducted on a dry silo mortar (DSM) production site in Scotland revealed that 56.07% of the input energy used was actually non-productive. This was as a result of an inefficient but commonplace cascade control system, originally installed to manage three 75kW Atlas Copco compressors. The audit also highlighted that using three compressors of the same capacity did not allow the system to efficiently match compressed-air output to demand.
The solution involved installing an EnergAir Metacentre compressed-air management system, adding a variable-speed drive and changing the compressor line-up to include a smaller 30kW compressor. As a result, off-load energy usage was reduced by over 90%, which, when combined with additional operating efficiencies achieved by the system, resulted in total energy savings of 61% or 182,728kW/h.
Compressor control specialist Peter Tomlins of EnergAir said: ‘The savings made at the Scottish site have prompted the business to install EnergAir’s Metacentre management system at all of its UK DSM sites. There are also three more sites to be completed in other sectors within the business.
‘The beauty of this system is that we can accurately audit a site prior to installation so we know what savings to expect. In every case so far, the actual savings have matched or exceeded our initial calculations.’
The aggregate producer in question is currently investing more than £20 million over five years in the strategic development of its national mortar business, including the expansion of DSM production. Each of the DSM plants is capable of producing between 400–800 tonnes a day, or 100,000–200,000 tonnes per annum. Flexible production capacity means that the plants can be highly responsive to customers needs and tend to run close to 15h a day, making energy efficiency close to the top of the operational agenda for each site.
What was the problem?
There are a number of reasons why air compressors pose such a problem for energy efficiency. Many sites still use fixed-speed compressors operating on a cascaded pressure switch control system. While this method is generally seen as the norm for running compressors, it is very inefficient and with relentless energy price rises it is essential that sites work to develop more efficient methods.
When operating fixed-speed compressors with a cascade control system the exact requirement of compressed air for a plant often falls between the combined capacities of the installed compressors. As one compressor’s limit is reached the output is doubled as the next compressor comes online. This arrangement uses much more energy than is required and leads to an increase in off-load running, with the compressor system creating more pressure than is needed.
The audit trail
The compressed-air audit conducted at the Scottish aggregate site ran continuously for 311.4h with a high-frequency data-log rate of every 5s. The site utilized three 75kW fixed-speed compressors and of the total energy consumed by each compressor, 56.07% of this energy was ‘non-productive’, adding thousands of pounds to the site’s energy costs.
The site’s compressed-air demand often fluctuated depending on the time of day, week and even year, which meant that with the fixed-speed compressors operating with a rigid cascade method, the site was rarely running at the ideal capacity in terms of efficient generation.
Recommendations and action
Two recommendations were followed in order to improve the efficiency of the plant, which, when combined, were able to reduce energy costs by well in excess of 50%.
First, two major changes to the existing compressor line-up were made. The first involved the installation of a retrofit variable-speed drive, giving a fixed-speed compressor variable-speed capability, thereby allowing compressed-air generation to be varied more precisely without reducing compressor efficiency.
The second change involved replacing one of the 75kW compressors with a 30kW compressor. The demand profile that had been recorded during the audit showed a large gap between the varying demand of the plant and the generation capacity. The smaller compressor, combined with the new variable-speed capacity of one of the original compressors, would ensure that air generation could be matched closely to demand, making large gains in energy efficiency.
The final step involved the installation of a new EnergAir Metacentre compressed-air management system. This is connected to sensitive pressure sensors on the air ring main, which provide feedback on system pressure. The system uses the data in real time to assess demand, while controlling all three compressors, with the system selecting the most efficient combination of compressors and compressor speed to accurately match demand.
The management system also provides maintenance updates every few seconds, helping maintenance teams to identify faults in the compressor system far more quickly than normal and reducing the risk of running a faulty compressor for many hours.
Validated results
The EnergAir Metacentre compressed-air management system keeps air pressure at the required 6.0 bar – a reduction from the 7.5 bar it was running at previously. Coupled with the correct use of the variable-speed drive, the site has now reduced its off-load (non-productive) energy usage to 1% rather than the previous 56.07%. With this significant increase in efficiency, the total potential energy savings at the site amount to 182,728 kW/h based on a 3,000h year.
Not only has this installation helped to reduce non-productive energy, in turn helping the site to reduce its carbon footprint, but with the savings of over 50% in energy costs the Metacentre management system will have paid for itself far sooner than was expected, while at the same time reducing maintenance costs significantly.
Questions to be asked at all sites
With rising energy costs and ever-increasing public focus on energy conservation, it is important to consider ways in which energy wastage can be reduced. It is essential to ask questions of current systems to identify where improvements can be made. For example: Has the demand profile been mapped? Are the installed compressors in the right combination of sizes? Has energy use been recorded and benchmarked so that the impact of any changes made can be validated? Are multiple compressors being controlled by an effective management system? Is a new variable-speed drive compressor the right solution, and can its capability for energy saving actually be realized?
Asking these questions will ensure that the potential savings on compressed air are realized. EnergAir have made the first step to identifying possible savings as simple as possible. The company has produced a free online Compressed Air Energy Savings Estimator, which can be found at www.energair.com. This provides users with an accurate estimate of potential savings, both in terms of cost and kW.
If required, the user can have a detailed report on how these saving are possible sent to them via e-mail. Not only is this service free and simple to use, but in the case of the Scottish site referred to earlier the estimate provided by the website was accurate to within 1% of the final savings.
When reviewing a site’s energy efficiency one of the most important factors to consider is compressed air, as this can represent a large percentage of the site’s energy consumption. Many current ‘solutions’ fail to significantly reduce off-load energy consumption and can be expensive to install, as they usually result in the purchase of a new compressor without an adequate control system.
Conclusion
EnergAir believe it is essential that businesses challenge convention in order to make the right decision and ensure that any potential savings are actually realized.
‘We are able to help plants save money on their energy costs in a market where energy bills are soaring,’ said Peter Tomlins. ‘The EnergAir Metacentre compressed-air management system can be installed in virtually all compressor systems with savings noticeable immediately. Many customers find that, once installed, it will pay for itself within a year while also helping to ensure maintenance is carried out sooner and with more accuracy than was previously possible.’
EnergAir Solutions Ltd, PO Box 974, Woking, Surrey GU22 8ZJ; tel: +44 (0)1932 343638; fax: +44 (0)1932 340809; email: sales@energair.co.uk