Cartridge Filters
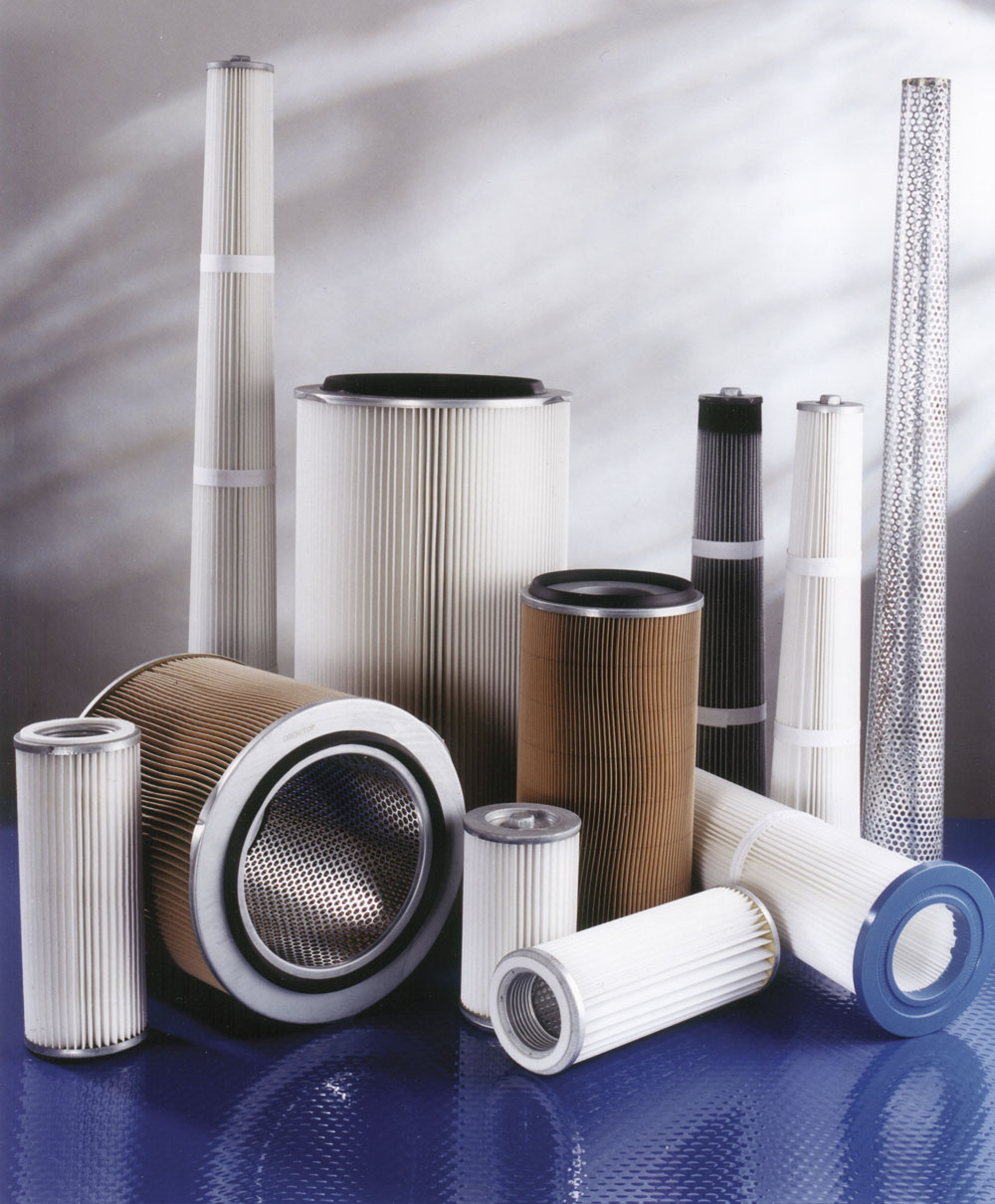
Pete Dawson of Dustcheck reflects on past developments in cartridge filter technology and looks ahead to the future
Just 25 years ago the use of cartridge-type filter elements in industrial dust control and process-air filtration was virtually unknown. Filter media for use in cartridge-type elements were very much in their infancy and little application data was available regarding their use. Woven bag-type media were a tried and tested method of filtration and it is true to say that cartridges were viewed with a great deal of scepticism by much of the dust-control industry.
Some dust-control companies, however, were convinced of the considerable benefits of this innovative approach and keen to embrace the new technology. The benefits were twofold: first, cartridge media offered superior efficiencies over conventional bag-type media, and secondly, much more compact solutions could be achieved through the use of a ‘pleated’ cartridge-type element.
There can be little doubt that their convictions were well founded, as today the pioneering work of such companies has led to cartridge technology becoming universally accepted across the whole spectrum of manufacturing industry.
Legislation and environmental considerations
With the advent of COSHH and the more recent Environmental Protection Act (EPA) more consideration is being given to stringent control of emission levels for a wide range of materials. In recent years many of these materials have been found to be harmful to health or the environment.
Filter solutions must be capable of conforming to these current regulations while also taking up the minimum amount of space. Cartridge technology offers extremely compact solutions (up to a 50% saving in footprint area) and efficiency guarantees that are simply not achievable with conventional bag-type media.
Media development
The choice of filter media is crucial. In the early days of cartridge filtration the relatively high cost of polyester cartridges meant that the most widely used media was cellulose paper similar to that used in automotive filtration. While this offered good levels of efficiency, it was not particularly resilient and was also unsuitable for use with damp or sticky products. Much has changed since those early days and modern media manufacturing and cartridge production processes mean that polyester-based media are now a very cost-effective solution offering high strength, excellent efficiency (eg 100% down to 2µm using Dustcheck’s latest TI15 media) and superior product-release characteristics.
Interestingly, cartridges can also be effectively laundered providing careful guidelines are followed. This dispels the myth that cartridges are a ‘one use only’ solution and also improves the ‘green’ credentials of the technology.
Over the past decade there have been continuous advances in the development of both standard and more exotic cartridge media. For finer or more-cohesive products, PTFE membranes can be applied to the base polyester, offering much greater efficiencies (eg 100% down to 0.5µm using TI56) and even better product-release characteristics.
For some time now all media variations have been available in ‘anti-static’ formats to aid the release characteristics for products prone to static build-up (polymer-based products being a prime example). The anti-static agent applied to membrane (cartridge)-type media is also inherent in the media itself, offering true anti-static properties throughout. In contrast, bag filters use only conductive threads woven into the fabric of the material. Another important benefit of the range of anti-static media is its ability to prevent spark generation caused by static discharge – an important consideration in complying with the requirements of the latest ATEX directive, which is having a major impact on the dust-control industry.
Latest developments
Cartridge filtration is continuously developing to keep up with the demands of industry. The latest Dustcheck developments include DRG5N, a 316L stainless steel media suitable for high-temperature applications while still offering high levels of efficiency. Most recently TI26, a H14-rated HEPA media suitable for secondary filtration and in-line protection applications, has also been made available, thereby offering HEPA-rated filter media in a cartridge format — a technology that was not available previously.
Adapting to application requirements
Dust control is rarely the main consideration for designers of process engineering plant. Multiple design considerations need to be taken into account when designing filter equipment. Air volume, filter area, ambient conditions, cleaning cycle, flow management and element geometry are all crucial, and product characteristics such as particle size, bulk density, bonding, agglomeration and moisture content also play an important part in the design process.
Therefore, not only is it necessary to choose the correct media for the product being handled, it is also important to select the correct cartridge format for the application. For instance, the use of a large-diameter, deep, close-pleated element would not normally be advocated for use in high-dust-load applications such as pneumatic conveying.
To this end, considerable time has been spent developing a range of cartridge formats to suit a wide range of applications.
‘Conical’ filter technologies that offer considerable cleaning-efficiency benefits are now available. This means lower differential pressures, reduced product re-entrainment and better product pre-separation, leading to longer filter life, lower utility usage and reduced maintenance.
Two-piece elements consisting of an outer filter sheath and a reusable inner core reduce replacement costs and additional waste. This also means that the element can be incinerated for easy disposal.
In addition, most cartridge configurations can be offered in both ‘clean-side’ and ‘dirty-side’ executions to offer the maximum flexibility for any application.
Reduced maintenance and improved cleaning
Maintenance on conventional bag-type filters has always been a lengthy, dirty and intricate procedure. There are also health and safety issues to be considered — particularly if the products being handled are of a toxic nature. Cartridge technology has revolutionized this operation, offering much faster, cleaner and simpler solutions — not least is the consideration that, for a given filter area, the number of filter cartridges is far less than the equivalent bag-type solution.
A number of different cleaning methods have been developed including mechanical shake, reverse air, and reverse jet.
The majority of cartridge-type solutions utilize reverse-jet technology. The technique is relatively simple: a jet of high-pressure air is injected into the filter element against the direction of process airflow. This causes particulate that has built up on the surface of the filter media to be dislodged, allowing it to fall back into the process (or, in the case of a dust collector, into a collection bin).
Both bag and cartridge reverse-jet systems employ very much the same hardware for this operation: a compressed-air manifold/reservoir, an automatic diaphragm cleaning valve operated by (for the most part) some form of electrically or pneumatically signalled controller, and a jet tube to direct cleaning air into the core of the filter element(s).
The methods of directing air into the filter element are also similar. Some use a simple hole (or series of holes) drilled into the jet tube to direct air into the element, while others use a venturi in order to ‘induce’ additional air into the element to improve cleaning.
However, differences occur because bag-type media rely on ‘depth’ type filtration, which allows dust particulate to be trapped in the fibres of the filter fabric. This method is dependent on the cleaning air to considerably flex/shake the filter element to remove any particulate.
Cartridge filters, by comparison, utilize ‘surface’ filtration, which does not allow particulate to penetrate the media and relies on a slight build-up of dust on the media surface to act as a ‘pre-filter’. The media is held rigid within the confines of the cartridge and the reverse-jet air is then used to simply ‘flush’ the media to dislodge particulate from the surface. Due to the much reduced core volume of a cartridge filter compared with an equivalent bag element, the effect of a given quantity of cleaning air is much greater, leading to improved cleaning efficiency. Multi-hole cleaning jets are also used to very good effect on a number of cartridge filters to ensure efficient distribution of cleaning air over the whole surface of the filter element. It is the above parameters which make it possible for cartridge filters to clean up to 20m2 of filter area from a single cleaning air source, thereby leading to reduced cleaning-valve requirements.
Another cleaning method unique to cartridge filtration is the wing cleaning system. This was developed for very light bulk-density dusts and can be much more effective than traditional reverse-jet cleaning systems. The system utilizes a rotating cleaning ‘wing’ coupled to an integral damper plate that isolates the filter cartridge against process-air flow during cleaning, thereby allowing true ‘off-line’ cleaning. This results in much better product-release characteristics and a reduced chance of product re-entrainment. The rotating wing also gives a very effective filter ‘rinsing’ action, thereby ensuring superior cleaning and sustained lower filter differential pressures. This in turn leads to longer filter life and lower maintenance. Operating at lower air pressures than traditional reverse-jet systems, wing cleaning is also much quieter in operation.
The future
Cartridge filters have been successfully applied to a wide range of applications over the past two decades, including general dust extraction, pneumatic conveying, powder coating plants, blasting plants and sack emptying. More recently, continuing development of new, advanced filter media has meant that cartridges are now being used for more difficult applications such as wet lacquer, cohesive materials and metal spray.
Cartridge technology is no longer a concept to be considered with any degree of caution; numerous applications across all industry sectors are testament to this. Moreover, the fact that most suppliers of dust-control equipment now offer their own cartridge solutions adds further weight to this standpoint.
Continuing product development and the pioneering work of companies such as Dustcheck mean that cartridge technology will remain a major force in industrial dust control and air filtration for many years to come.
For further information contact Pete Dawson at Dustcheck on tel: (01782) 599454 or email: sales@dustcheck.co.uk
Just 25 years ago the use of cartridge-type filter elements in industrial dust control and process-air filtration was virtually unknown. Filter media for use in cartridge-type elements were very much in their infancy and little application data was available regarding their use. Woven bag-type media were a tried and tested method of filtration and it is true to say that cartridges were viewed with a great deal of scepticism by much of the dust-control industry.
Some dust-control companies, however, were convinced of the considerable benefits of this innovative approach and keen to embrace the new technology. The benefits were twofold: first, cartridge media offered superior efficiencies over conventional bag-type media, and secondly, much more compact solutions could be achieved through the use of a ‘pleated’ cartridge-type element.
There can be little doubt that their convictions were well founded, as today the pioneering work of such companies has led to cartridge technology becoming universally accepted across the whole spectrum of manufacturing industry.
Legislation and environmental considerations
With the advent of COSHH and the more recent Environmental Protection Act (EPA) more consideration is being given to stringent control of emission levels for a wide range of materials. In recent years many of these materials have been found to be harmful to health or the environment.
Filter solutions must be capable of conforming to these current regulations while also taking up the minimum amount of space. Cartridge technology offers extremely compact solutions (up to a 50% saving in footprint area) and efficiency guarantees that are simply not achievable with conventional bag-type media.
Media development
The choice of filter media is crucial. In the early days of cartridge filtration the relatively high cost of polyester cartridges meant that the most widely used media was cellulose paper similar to that used in automotive filtration. While this offered good levels of efficiency, it was not particularly resilient and was also unsuitable for use with damp or sticky products. Much has changed since those early days and modern media manufacturing and cartridge production processes mean that polyester-based media are now a very cost-effective solution offering high strength, excellent efficiency (eg 100% down to 2µm using Dustcheck’s latest TI15 media) and superior product-release characteristics.
Interestingly, cartridges can also be effectively laundered providing careful guidelines are followed. This dispels the myth that cartridges are a ‘one use only’ solution and also improves the ‘green’ credentials of the technology.
Over the past decade there have been continuous advances in the development of both standard and more exotic cartridge media. For finer or more-cohesive products, PTFE membranes can be applied to the base polyester, offering much greater efficiencies (eg 100% down to 0.5µm using TI56) and even better product-release characteristics.
For some time now all media variations have been available in ‘anti-static’ formats to aid the release characteristics for products prone to static build-up (polymer-based products being a prime example). The anti-static agent applied to membrane (cartridge)-type media is also inherent in the media itself, offering true anti-static properties throughout. In contrast, bag filters use only conductive threads woven into the fabric of the material. Another important benefit of the range of anti-static media is its ability to prevent spark generation caused by static discharge – an important consideration in complying with the requirements of the latest ATEX directive, which is having a major impact on the dust-control industry.
Latest developments
Cartridge filtration is continuously developing to keep up with the demands of industry. The latest Dustcheck developments include DRG5N, a 316L stainless steel media suitable for high-temperature applications while still offering high levels of efficiency. Most recently TI26, a H14-rated HEPA media suitable for secondary filtration and in-line protection applications, has also been made available, thereby offering HEPA-rated filter media in a cartridge format — a technology that was not available previously.
Adapting to application requirements
Dust control is rarely the main consideration for designers of process engineering plant. Multiple design considerations need to be taken into account when designing filter equipment. Air volume, filter area, ambient conditions, cleaning cycle, flow management and element geometry are all crucial, and product characteristics such as particle size, bulk density, bonding, agglomeration and moisture content also play an important part in the design process.
Therefore, not only is it necessary to choose the correct media for the product being handled, it is also important to select the correct cartridge format for the application. For instance, the use of a large-diameter, deep, close-pleated element would not normally be advocated for use in high-dust-load applications such as pneumatic conveying.
To this end, considerable time has been spent developing a range of cartridge formats to suit a wide range of applications.
‘Conical’ filter technologies that offer considerable cleaning-efficiency benefits are now available. This means lower differential pressures, reduced product re-entrainment and better product pre-separation, leading to longer filter life, lower utility usage and reduced maintenance.
Two-piece elements consisting of an outer filter sheath and a reusable inner core reduce replacement costs and additional waste. This also means that the element can be incinerated for easy disposal.
In addition, most cartridge configurations can be offered in both ‘clean-side’ and ‘dirty-side’ executions to offer the maximum flexibility for any application.
Reduced maintenance and improved cleaning
Maintenance on conventional bag-type filters has always been a lengthy, dirty and intricate procedure. There are also health and safety issues to be considered — particularly if the products being handled are of a toxic nature. Cartridge technology has revolutionized this operation, offering much faster, cleaner and simpler solutions — not least is the consideration that, for a given filter area, the number of filter cartridges is far less than the equivalent bag-type solution.
A number of different cleaning methods have been developed including mechanical shake, reverse air, and reverse jet.
The majority of cartridge-type solutions utilize reverse-jet technology. The technique is relatively simple: a jet of high-pressure air is injected into the filter element against the direction of process airflow. This causes particulate that has built up on the surface of the filter media to be dislodged, allowing it to fall back into the process (or, in the case of a dust collector, into a collection bin).
Both bag and cartridge reverse-jet systems employ very much the same hardware for this operation: a compressed-air manifold/reservoir, an automatic diaphragm cleaning valve operated by (for the most part) some form of electrically or pneumatically signalled controller, and a jet tube to direct cleaning air into the core of the filter element(s).
The methods of directing air into the filter element are also similar. Some use a simple hole (or series of holes) drilled into the jet tube to direct air into the element, while others use a venturi in order to ‘induce’ additional air into the element to improve cleaning.
However, differences occur because bag-type media rely on ‘depth’ type filtration, which allows dust particulate to be trapped in the fibres of the filter fabric. This method is dependent on the cleaning air to considerably flex/shake the filter element to remove any particulate.
Cartridge filters, by comparison, utilize ‘surface’ filtration, which does not allow particulate to penetrate the media and relies on a slight build-up of dust on the media surface to act as a ‘pre-filter’. The media is held rigid within the confines of the cartridge and the reverse-jet air is then used to simply ‘flush’ the media to dislodge particulate from the surface. Due to the much reduced core volume of a cartridge filter compared with an equivalent bag element, the effect of a given quantity of cleaning air is much greater, leading to improved cleaning efficiency. Multi-hole cleaning jets are also used to very good effect on a number of cartridge filters to ensure efficient distribution of cleaning air over the whole surface of the filter element. It is the above parameters which make it possible for cartridge filters to clean up to 20m2 of filter area from a single cleaning air source, thereby leading to reduced cleaning-valve requirements.
Another cleaning method unique to cartridge filtration is the wing cleaning system. This was developed for very light bulk-density dusts and can be much more effective than traditional reverse-jet cleaning systems. The system utilizes a rotating cleaning ‘wing’ coupled to an integral damper plate that isolates the filter cartridge against process-air flow during cleaning, thereby allowing true ‘off-line’ cleaning. This results in much better product-release characteristics and a reduced chance of product re-entrainment. The rotating wing also gives a very effective filter ‘rinsing’ action, thereby ensuring superior cleaning and sustained lower filter differential pressures. This in turn leads to longer filter life and lower maintenance. Operating at lower air pressures than traditional reverse-jet systems, wing cleaning is also much quieter in operation.
The future
Cartridge filters have been successfully applied to a wide range of applications over the past two decades, including general dust extraction, pneumatic conveying, powder coating plants, blasting plants and sack emptying. More recently, continuing development of new, advanced filter media has meant that cartridges are now being used for more difficult applications such as wet lacquer, cohesive materials and metal spray.
Cartridge technology is no longer a concept to be considered with any degree of caution; numerous applications across all industry sectors are testament to this. Moreover, the fact that most suppliers of dust-control equipment now offer their own cartridge solutions adds further weight to this standpoint.
Continuing product development and the pioneering work of companies such as Dustcheck mean that cartridge technology will remain a major force in industrial dust control and air filtration for many years to come.
For further information contact Pete Dawson at Dustcheck on tel: (01782) 599454 or email: sales@dustcheck.co.uk