Thompsons super-strength bodies for Jim Jamieson
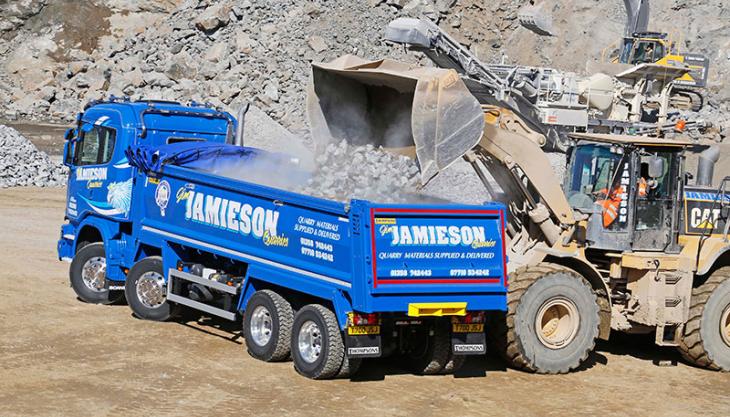
Scottish quarry operator ignores normal accepted practice and does things its own way
IT is quite rare these days to find a road transport operation that does things entirely its own way, completely at odds with generally accepted practice. But one Scottish quarry operator is doing exactly that.
Ten new eight-wheelers have joined Ellon-based Jim Jamieson Quarries’ tipper fleet over the last 18 months, with another five currently in build with Thompsons in Blackburn, Lancashire. But whereas many 8x4s today have fairly routine specifications, Jamieson’s tippers are anything but.
The company’s ‘standard’ chassis is a full-sleeper G cab Scania, supplied with the Swedish company’s highest output 12.7-litre engine. But is 490hp excessive for a 32-tonne gvw truck? Jamieson do not think so. Then there is the body – a full-spec, double-skinned, all-steel Thompsons Loadmaster, complete with front and rear cornerposts, 5mm Hardox floor and raked rear end with hydraulic ‘AutoLift’ tailgate.
Other tippers in the Jamieson fleet include a pair of the latest Euro 6 DAF CFs. Specified principally for lighter aggregates and asphalt work, these trucks have 510hp engines and are fitted with Thompsons’ insulated alloy bodies built to Jamieson’s particular requirements, which include extra-durable 8mm thick hardened aluminium floors.
With few tipper operators today specifying their trucks to such a high level, Jamieson’s transport manager Brian Clark explained how it all came down to productivity. ‘Our tippers are not light,’ he said, ‘and compared with an average-specification eight-wheeler we might be losing half a tonne every trip. So, if we do five trips a day, then we are 2.5 tonnes down – which sounds a lot.
‘On the other hand,’ he continued, ‘we get greatly superior road performance. Even on short haul trips, they can shave 10 minutes off a journey time. And this level of superior performance continues when we arrive on site. The driver has no need to get out of his cab. Put simply, we can be tipped and gone by the time the driver of a conventional tipper is walking back to his cab having just manually released the tailgate locking bar.’
According to Mr Clark, because of the extra performance of the vehicles, productivity is increased. ‘Over a typical week, the overall performance bonus might translate into three extra trips. So that’s an extra 54 tonnes of product out of the door. Take away five days of losing 2.5 tonnes per day and that still gives us an additional 41 tonnes of material delivered per truck, per week,’ he explained.
‘Over 50 weeks, that’s 2,050 tonnes per year, and over 10 trucks, that’s an extra 20,000 tonnes going out to our customers every year. This is our proof that high-performance trucks really can pay.’
Other bonuses also arise from running premium-spec trucks. ‘With tippers, it is always the bodies that do the really hard work, so having the strongest, toughest and most reliable bodies available helps to maximize vehicle up-time,’ said Mr Clark. ‘The Loadmaster is undoubtedly today’s premium tipper body – it’s super-strong and able to handle any job whatsoever.
‘But perhaps best of all is Thompsons’ service. A while back we needed them to come up to Ellon and address a minor installation issue. Their people were up here and fixed the problem within 24h by working through the night to make sure the whole fleet was ready for work the following morning. Coming all the way from Blackburn, that’s truly impressive.’