Terex Pegson and Powerscreen cover all bases in Southern France
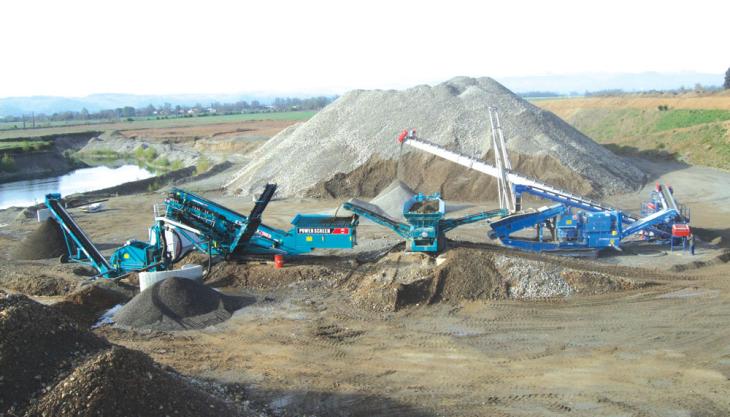
Terex Pegson and Powerscreen French dealers Catecom have recently configured and installed a rental crushing, screening and washing plant in the foothills of the Pyrenees, in southern France, to help process dredged river-bed material. The total package comprises a Terex Pegson 1000 Maxtrak, together with a Warrior 1400, a Chieftain 1700 rinser, a Finesmaster 120 Compact and a T5032 stockpile conveyor from Powerscreen, plus the customer’s own static screen.
Arnaud Debucquois, sales manager of Catecom, said: ‘In addition to selling the full Terex Pegson and Powerscreen range, we provide a comprehensive rental service with all the same customer support standards. This particular customer has a static plant that could not meet the demand for aggregates in the area, so the Terex Pegson and Powerscreen plant was rented to increase production.’ He added that the customer has been so impressed with the plant’s performance that they have decided to purchase it.
The riverbed material is fed to the Powerscreen Warrior 1400, which is equipped with a 25mm bottom deck and 150mm upper deck. These deck sizes separate the aggregate into 0–25mm and 25–150mm products. The 25–150mm aggregate is fed to the Terex Pegson 1000 Maxtrak, which is equipped with an Automax cone crusher operating at a closed-side setting of 25mm.
Featuring a hydraulic setting, tramp release and unblocking system, and available with a choice of four liners, including Autosand, and two ‘eccentric throws, the Automax’s crushes and shapes the material to make –25mm aggregate with good cubicity. The crushed material is fed to the customer’s existing static screen, which recirculates any +25mm oversize back to the Maxtrak. The –25mm product is used as sub-base.
Meanwhile, the –25mm from the Warrior 1400 is fed to the Powerscreen Chieftain 1700 rinser, which is fitted with a 4mm bottom deck, 15mm middle deck and 25mm top deck. Key features of this machine include spray bars on all decks, a hydraulically folding catchbox, fold-out screen walkways, a transverse engine to aid access and serviceability, and a patent pending, hydraulically folding auxiliary conveyor for oversize material stockpiling (three-deck model).
This unit produces four washed saleable end products — 0–4mm sand, 4–15mm aggregate, 15–25mm aggregate and +25mm aggregate — for use in concrete production. The 0–4mm sand is sent to the Powerscreen Finesmaster 120 Compact for washing. This utilizes a sump and rubber-lined slurry pump, rubber-lined hydrocyclones and a high-frequency dewatering screen to remove clays, silts and slime from sand to bring it into specification. The 0–4mm sand is stockpiled using a self-contained Powerscreen T5032 conveyor.
Arnaud Debucquois, sales manager of Catecom, said: ‘In addition to selling the full Terex Pegson and Powerscreen range, we provide a comprehensive rental service with all the same customer support standards. This particular customer has a static plant that could not meet the demand for aggregates in the area, so the Terex Pegson and Powerscreen plant was rented to increase production.’ He added that the customer has been so impressed with the plant’s performance that they have decided to purchase it.
The riverbed material is fed to the Powerscreen Warrior 1400, which is equipped with a 25mm bottom deck and 150mm upper deck. These deck sizes separate the aggregate into 0–25mm and 25–150mm products. The 25–150mm aggregate is fed to the Terex Pegson 1000 Maxtrak, which is equipped with an Automax cone crusher operating at a closed-side setting of 25mm.
Featuring a hydraulic setting, tramp release and unblocking system, and available with a choice of four liners, including Autosand, and two ‘eccentric throws, the Automax’s crushes and shapes the material to make –25mm aggregate with good cubicity. The crushed material is fed to the customer’s existing static screen, which recirculates any +25mm oversize back to the Maxtrak. The –25mm product is used as sub-base.
Meanwhile, the –25mm from the Warrior 1400 is fed to the Powerscreen Chieftain 1700 rinser, which is fitted with a 4mm bottom deck, 15mm middle deck and 25mm top deck. Key features of this machine include spray bars on all decks, a hydraulically folding catchbox, fold-out screen walkways, a transverse engine to aid access and serviceability, and a patent pending, hydraulically folding auxiliary conveyor for oversize material stockpiling (three-deck model).
This unit produces four washed saleable end products — 0–4mm sand, 4–15mm aggregate, 15–25mm aggregate and +25mm aggregate — for use in concrete production. The 0–4mm sand is sent to the Powerscreen Finesmaster 120 Compact for washing. This utilizes a sump and rubber-lined slurry pump, rubber-lined hydrocyclones and a high-frequency dewatering screen to remove clays, silts and slime from sand to bring it into specification. The 0–4mm sand is stockpiled using a self-contained Powerscreen T5032 conveyor.