Smarter maintenance with RigScan from Epiroc
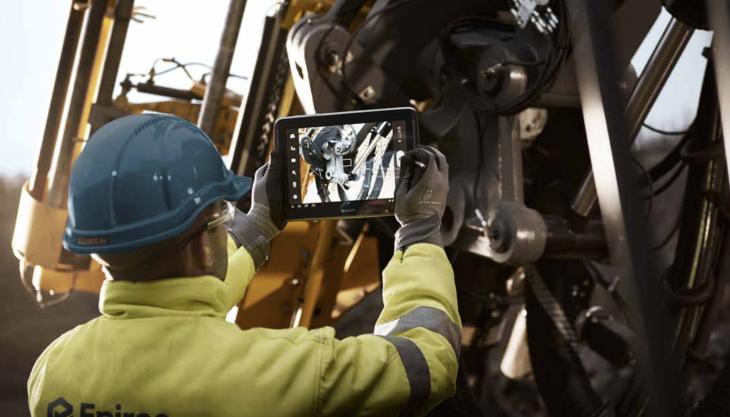
Epiroc optimize service and maintenance operations with cutting-edge drill rig audit technology
NO mining, quarrying or construction operation can exist without maintenance, but it can be a difficult balance to strike between keeping workers safe and machines in good shape, and getting the most out of every minute of uptime.
For much of the industry, assessing the health of a machine still involves a technician inspecting it by hand for several hours or days, taking notes by hand. Companies can find themselves in the unenviable position of being pulled between risking a critical parts failure and missing critical productivity goals.
Today, however, technology is providing companies with innovative new avenues to optimize their operations, and the way maintenance and service is performed is no exception to this trend.
RigScan from Epiroc leverages technology, both emerging and mature, to make the drill rig equipment audit process faster, less intrusive and more comprehensive.
High-tech thermal cameras can find early signs of wear or part stress invisible to the human eye, and unseen internal leaks, providing the technician with a much more detailed view of the machine’s health.
This new access to high-fidelity data is managed digitally through a tablet which ensures that no parts are missed during the audit. The benefits of computerization continue once the audit is completed, as the results are processed and analysed against manufacturer specifications to ensure that any issues, large or small, are brought to the owner’s attention within 72 hours.
Special emphasis is placed on safety too, with any issues that may lead to potential safety hazards brought to the operator’s attention before the technician leaves the site.
While a RigScan audit is undoubtedly a step up from traditional audits as a one-off maintenance check, the benefits are amplified by performing them on a regular basis.
RigScan audits can be performed routinely with minimal impact on a machine’s uptime thanks to the quick turnaround time. Over time, the data collected will create a comprehensive picture of a machine’s health that can be used to optimize multiple aspects of the maintenance process.
For example, costly unplanned repairs can be avoided, and well-maintained equipment lasts longer. Also, regular audits provide useful insights on when, how and why parts are wearing out, creating opportunities to find subtle inefficiencies that might otherwise go unnoticed.
Moreover, having additional confidence in the health of equipment allows for more precise budgeting too. Money that would have otherwise been set aside in anticipation of unforeseen maintenance costs can now be put to better use elsewhere.
Looking forward, the technology that supports the RigScan concept continues to evolve. As machines become more automated, so too will their service protocols. Future equipment will be able to monitor and report issues automatically, letting owners know when a closer look is needed and providing service technicians with an even greater breadth of data to use in planning maintenance.