Sandvik introduce Top Hammer XL
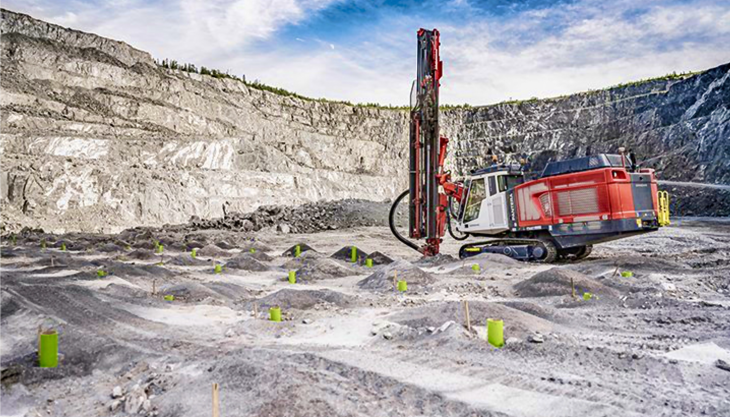
New fully optimized top-hammer system for large hole size drilling in quarries and surface mines
AIMED at large-scale quarry and surface mining customers, Top Hammer XL is the latest innovation in surface top-hammer drilling from Sandvik Mining and Rock Solutions. The new, ground-breaking drilling system is said to offer a faster, more fuel-efficient and more cost-effective way to drill 140–178mm (5.5–7in) diameter holes.
The components of the system – a new Pantera DP1600i drill rig, new RD1840C rock drill and new LT90 rock tools – have all been optimized to work together seamlessly for exceptional drilling results.
Sandvik say they are challenging the industry by introducing a ground-breaking top-hammer drilling innovation that offers the benefits of top-hammer drilling technology as a viable alternative to down-the-hole (DTH) drilling, but on a much larger scale than before.
As well as expanding the hole size range of top-hammer drilling to up to 178mm (7in), they say the Top Hammer XL drilling system provides a faster and more fuel-efficient drilling method, ultimately contributing to reduced CO2 emissions.
The heart of the Top Hammer XL system lies in Sandviken, Sweden, and Tampere, Finland, where all the components have been designed and manufactured to work perfectly together to provide smooth operation and a highly productive system with optimum drilling results.
‘A key asset of the Top Hammer XL drilling system is that all three main components – the drill rig, rock drill and rock tools – have been reviewed, redesigned and mutually optimized,’ said Jukka Siltanen, product line manager for rock drills at Sandvik Mining and Rock Solutions.
The efficiency of the new Top Hammer XL drilling system stems from these three main components. The proven carrier offers a solid base for the extremely powerful rock drill that generates an optimum pulse for the effective tooling system, which in turn transfers the high-energy shock wave with minimum losses to the rock.
The Top Hammer XL system has been thoroughly tested and proven in several field tests, drilling more than 100,000m in challenging rock conditions. The test results have shown a 50% reduction in fuel consumption, 25% reduction in total drilling costs and 15% increase in productivity, compared with the DTH drilling method.
Pantera DP1600i
The DP1600i is the newest member of the Pantera DPi series of intelligent top-hammer drill rigs, characterized by high penetration rates and advanced automation options for data-based fleet management and drilling performance optimization.
Designed for large-hole drilling, the Pantera DP1600i, with its practical intelligence and support for higher-level automation solutions, is well suited to production drilling in large quarries or open-pit mines.
The new rig is based on the reliable and proven Pantera DPi series platform, but with upgraded key components to meet the needs of the Top Hammer XL system. Together with the powerful RD1840C rock drill and robust LT90 rock tools, the end result is extreme capacity for larger hole sizes, without increasing the physical drill rig footprint.
As such, the Pantera DP1600i is said to offer the highest power in its class and can be customized with a variety of options to meet special requirements. It is available in Tier 3 and Stage 5 engine emission versions.
‘The Pantera DPi platform has proven itself over the years, starting as far back as 2008, so it was a natural choice to upgrade the existing platform to the next level for this new solution,’ explained Jarno Viitaniemi, product manager for surface drilling at Sandvik Mining and Rock Solutions.
RD1840C rock drill
The new RD1840C rock drill is designed for large hole drilling with high 49kW (66hp) drilling power. Its robust design and well-balanced long piston percussion package are made specifically for demanding circumstances. The long piston technology generates high-impact energy with optimum pulse form, optimizing performance in large-hole drilling without compromising the service life of the rock tools.
As an additional option, later this year the RD1840C will be available with the Sandvik RockPulse tool stress monitoring system, which will offer the drill operator real-time measurement data on three key drilling parameters: drill bit response, tools load and feed level. The system will measure the stress waves and guide the operator to find the right drilling parameters for the best rock contact and performance.
LT90 rock tools
The LT90 rock tools have been developed to match the other components in the Top Hammer XL system. The tools – consisting of a shank adapter, MF tube rods and drill bits – are said to offer the best-possible drilling dynamics and rock-breaking efficiency.
‘Our patented and optimized LT90 rock tools design increases productivity, improves hole straightness and provides great coupling characteristics and a long service life,’ said Fredrik Björk, product manager for top-hammer surface tools at Sandvik Mining and Rock Solutions.
‘All in all, this new shoulder-driven system with a double-pass thread gives our customers a much better drilling experience. Combined with Sandvik’s class-leading rock tools services, it will truly help our customers reach new levels in their drilling operations.’
Made from high-quality steel, the LT90 shank adapter is designed for optimal energy transfer from the rock drill piston into the drill string and has been developed through close collaboration between Sandvik’s experts on both rock tools and rock drills to ensure optimum performance.
With the new MF tube rods, developed to convey high-energy shock waves with minimal energy loss in the threads, Top Hammer XL customers will get a higher rate of penetration, straighter holes and increased service life for the whole drill string.
The optimized thread design minimizes stress levels from bending, and excellent coupling characteristics are seen in the double-pass thread of this tool system. Premium steel grades and heat-treatment processes further improve its durability.
Sandvik’s classic and patented retrac design form the base for the LT90 drill bits, with a strong gauge row, excellent flushing, high rock-breaking capabilities and reduced hole deviation. Available from 140–178mm (5.5–7in), they can be delivered in standard carbide grades as well as PowerCarbide, depending on the rock formation.
‘Our aim is to serve our customers with the best solutions for every application and in all conditions in order to maximize their productivity, with a strong focus on safety and sustainability,’ said Petri Virrankoski, president of surface drilling at Sandvik Mining and Rock Solutions.
‘We are extremely excited to lead the way in the industry as Top Hammer XL opens up completely new possibilities for our customers to improve their operations.’