Ribblesdale cement works upgrade cuts coal usage
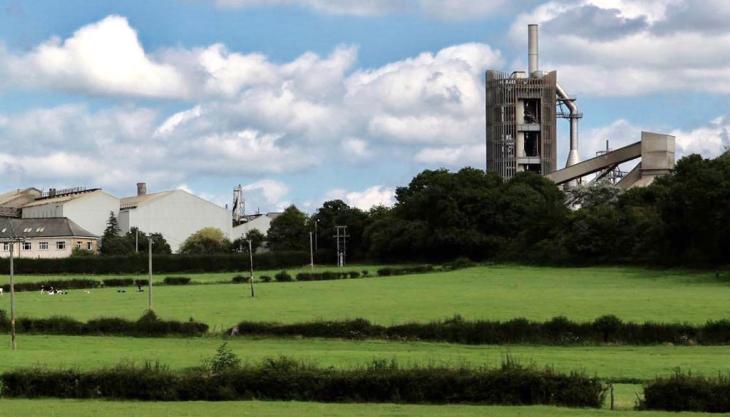
Hanson reduce carbon emissions and waste to landfill by using more alternative fuels to power the kiln
HANSON Cement’s Ribblesdale cement works in Lancashire is reducing its carbon emissions and waste to landfill by using more alternative fuels to power the kiln.
An upgrade to the automatic feed system is part of a three-phase fuel strategy to reduce the amount of coal used to power the kiln and to allow more solid recovered fuel (SRF) to be used.
SRF is made up of non-recyclable paper and plastic from council refuse collections and has been used at Ribblesdale cement works since 2011.
The upgrade will cut coal consumption by 50,000 tonnes a year and reduce the amount of waste going to landfill by 74,000 tonnes a year.
The raw material is processed by a local company and delivered into a docking station at the works – by lorries with hydraulic moving floors – where it is automatically fed into a new fuel system.
Simon Moorhouse, operations manager with Hanson Cement, said: ‘Successful trials have also been carried out to burn waste-paper residues from motor-oil filters in the kilns and use of this as an additional alternative fuel will start next year.
‘The investment is part of our ongoing commitment to minimize waste and save energy.’