New hydrocyclone from Weir Minerals
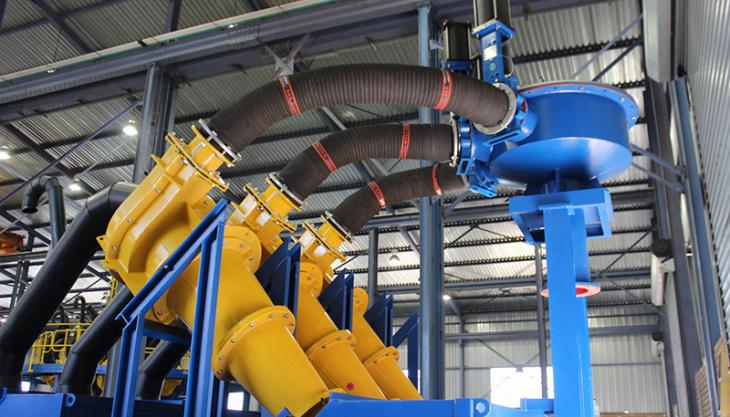
Latest Cavex 700CVX hydrocyclone maximizes throughput within existing footprint
MAXIMIZED throughput and uptime, with minimized costs, are the goals of all processing plants. Extensive research and smart engineering have resulted in the development of a hydrocyclone that is said to achieve up to 50% higher throughput capacity in comparison with competitor cyclones in the 26in diameter range due to its larger inlet and vortex finder configuration.
The Cavex 700CVX hydrocyclone, with a smaller, more space-efficient body, has a higher throughput than the Cavex 650CVX hydrocyclone making it attractive for new installations as well as retrofitting into existing cyclone clusters. This allows sites to increase capacity with minimal capital expenditure while maintaining a competitive advantage.
According to Sheldon Gabriel, Weir Minerals Africa and Middle East’s product manager for cyclones, the inclusion of a unique laminar spiral inlet in the Cavex 700CVX hydrocyclone is the secret behind the success of this new product.
‘It is important to note that the development of the Cavex 700CVX hydrocyclone was not based merely on a cone modification, but rather on an entirely new feed geometry that substantially increases hydraulic throughput capacity while minimizing localized wear on the feed chamber and vortex finder,’ explained Mr Gabriel.
Conventional hydrocyclone geometry causes migration of unclassified solids into the overflow, which can result in valuable mineral losses. The laminar spiral inlet geometry design of the Cavex 700CVX hydrocyclone provides a natural flow path into the hydrocyclone. Owing to the fact that the shape has no sharp edges or corners, it readily allows the feed stream to blend smoothly and efficiently with the rotating slurry within the chamber.
‘When turbulence is reduced, sorting efficiency is naturally enhanced and fewer misplaced fines bypass to the underflow, with less coarse tramp material bypassing to the overflow. This is achieved by maximizing the air core diameter created within the rotating mass of fluid in the hydrocyclone and results in reductions in overgrinding and circulating loads,’ said Mr Gabriel.
In conventional hydrocyclones, slurry bursts into the cylinder with no flow control. The resultant turbulence is responsible for premature and localized wear of the liner walls causing inefficient classification and decreased wear life.
By minimizing flow resistance through the feed chamber, Cavex hydrocyclones are able to process substantially higher slurry volumes. This increased productivity effectively reduces the quantity of hydrocyclones required and reduces the energy required for the job.