New circular fluid-bed dryer from Kason
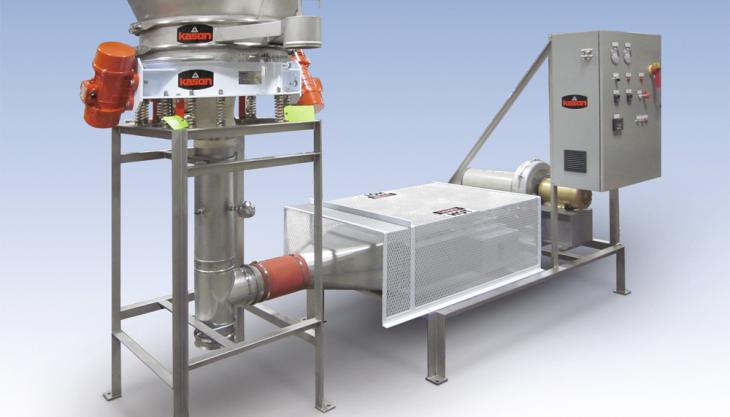
New Vibro-Bed unit improves energy efficiency and reduces cost, size, and cleaning time
THE new 762mm diameter Vibro-Bed circular fluid-bed drying system from Kason has been designed to increase operating efficiency, reduce cleaning time and cut costs.
The inherent rigidity of the circular fluid-bed processing chamber exceeds that of traditional rectangular fluid-bed processors, allowing its materials of construction to be down-gauged and vibratory motors to be downsized.
Associated components, such as multiple air inlets and outlets, have also been eliminated, as the circular unit requires only one of each. As a result, the dryer is said to be lighter, stronger and more energy efficient at equivalent capacities.
According to Kason, cleaning time is also cut in half due to stainless steel material contact surfaces, reduced weld seams, a quick-disconnect housing, and the lack of internal cross-members.
Compactness and lightness allow the configuring of complete systems or modules containing the blower, heater and programmable controls on skid-mounted frames, requiring only on-site connections to a power source, dust collector, and material inlet/outlet.
Material fed into the top inlet of the dryer descends into the fluid-bed chamber where it vibrates on a circular screen within a rising column of heated air ducted into the bottom of the chamber from the upstream heater/blower.
The continuous airflow, and vibration induced by two vibratory motors and spring suspension, separate and fluidize individual particles, maximizing surface area and drying efficiency.
The vibratory action also causes material to travel from the centre of the screen to a discharge spout at the screen’s periphery in controlled spiral pathways on a ‘first-in/first-out’ basis.
The circular fluid processing unit is offered in diameters from 460mm to 2,135mm, encompassing batch and continuous applications from low-capacity laboratory and pilot plant testing to medium-to-high-volume production.
All units are available in drying/heating, cooling or moisturizing configurations, while available options include: centrifugal screeners to de-agglomerate moist incoming material; spray nozzles to coat dried particles; and vibratory screeners to scalp, classify or de-dust dried material.