Moisture-reduction system for Colchester Quarry
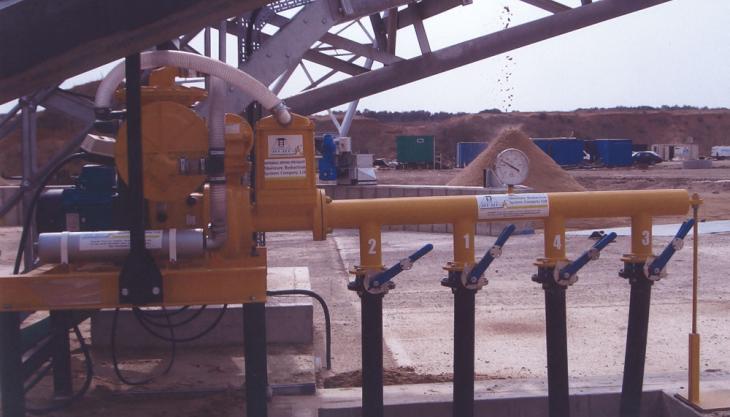
As part of the newly constructed sand and gravel plant at Tarmac Ltd’s Colchester Quarry (see QM February 2007), Cheshire-based specialist pumping company Moisture Reduction Systems Ltd (MRS) installed a moisture-reduction system for drying the medium-grade sand stockpiles.
Installation of the system followed several pre-planning meetings and methodology discussions between Tarmac’s project manager, Bob Aldhouse, and MRS’s managing director/geotechnical consultant, Len McGarry, during which the design criteria were established.
The final design involved the installation of a 7.5kW three-phase electrically driven, large-air-handling, double-diaphragm pump coupled to a four take-off manifold with control valves to a network of four underground vacuum/water-conveying pipelines. These were in turn connected to an intensive pattern of special filter-wrapped perforated drainage pipe located under each of the two 50m x 15m kidney-shaped sand stockpiles.
The extent of the moisture-reduction system required was determined using technical information obtained by means of a free drawdown pumping test carried out by MRS Ltd, whereby actual sand samples from the site were placed in a MRS simulator to ascertain the percentage moisture-retained figures. Data derived during subsequent testing helped to determine the approximate permeability values, particle shape, flow rates etc, as well as the remaining surface-tension moisture level following rapid removal of all free water from the interstitial spaces during drawdown.
Another important part of the design criteria established by the test involved the selection of appropriate filter media to be wrapped around the perforated drainage pipe. This was based on drawdown results (ie falling head) and prevailing D10 information obtained from the site’s own sieve analyses. Selection of the correct filter pack is important as it ensures the longevity of the system and prevents any ‘choking’ of the installation as a result of fines migration during subsequent pumping operations.
According to MRS, the benefits of their moisture-reduction system include lower costs, energy savings, better handling and greater product quality control as a consequence of:
MRS will be exhibiting their moisture-reduction system at Hillhead 2007 and say installations have now been carried out throughout the UK, Ireland, Europe, the US and, more recently, Australia.
Readers wanting further information or to request a free ‘no obligation’ drawdown pumping test and technical report on their own products should contact Len McGarry on tel/fax: (01260) 281002; mobile: (07836) 516216; email: drysand@btconnect.com; website: www.drysand.co.uk
Installation of the system followed several pre-planning meetings and methodology discussions between Tarmac’s project manager, Bob Aldhouse, and MRS’s managing director/geotechnical consultant, Len McGarry, during which the design criteria were established.
The final design involved the installation of a 7.5kW three-phase electrically driven, large-air-handling, double-diaphragm pump coupled to a four take-off manifold with control valves to a network of four underground vacuum/water-conveying pipelines. These were in turn connected to an intensive pattern of special filter-wrapped perforated drainage pipe located under each of the two 50m x 15m kidney-shaped sand stockpiles.
The extent of the moisture-reduction system required was determined using technical information obtained by means of a free drawdown pumping test carried out by MRS Ltd, whereby actual sand samples from the site were placed in a MRS simulator to ascertain the percentage moisture-retained figures. Data derived during subsequent testing helped to determine the approximate permeability values, particle shape, flow rates etc, as well as the remaining surface-tension moisture level following rapid removal of all free water from the interstitial spaces during drawdown.
Another important part of the design criteria established by the test involved the selection of appropriate filter media to be wrapped around the perforated drainage pipe. This was based on drawdown results (ie falling head) and prevailing D10 information obtained from the site’s own sieve analyses. Selection of the correct filter pack is important as it ensures the longevity of the system and prevents any ‘choking’ of the installation as a result of fines migration during subsequent pumping operations.
According to MRS, the benefits of their moisture-reduction system include lower costs, energy savings, better handling and greater product quality control as a consequence of:
- significantly less drying time than gravity drainage
- faster production turn-around times
- easier handling by wheel loaders due to drier products
- reduced processing costs (especially if fluid-bed/furnace drying is used)
- improvements in site conditions (no flooded areas around the base of stockpiles)
- ability to build safer, taller stockpiles with smaller base area (no slumping)
- no ice formation in stockpiles during the winter
- environmentally friendly as all run-off flow paths are inwards rather than outwards
- production of clean, reusable discharge water for recirculation to the washing process.
MRS will be exhibiting their moisture-reduction system at Hillhead 2007 and say installations have now been carried out throughout the UK, Ireland, Europe, the US and, more recently, Australia.
Readers wanting further information or to request a free ‘no obligation’ drawdown pumping test and technical report on their own products should contact Len McGarry on tel/fax: (01260) 281002; mobile: (07836) 516216; email: drysand@btconnect.com; website: www.drysand.co.uk