Modular sample buildings from McLanahan
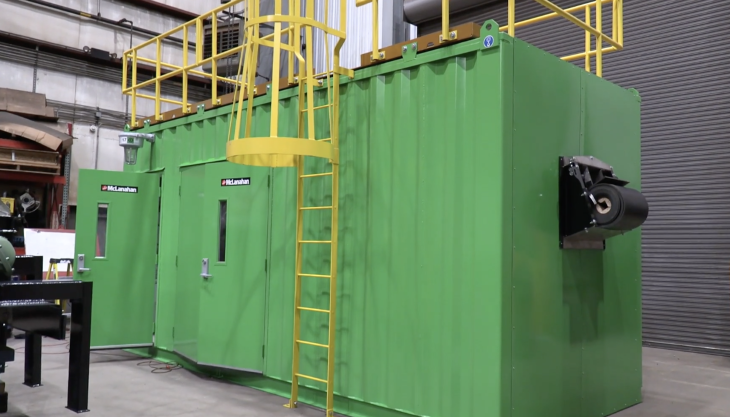
Pre-packaged sample buildings provide installation time and cost savings for customers
McLANAHAN modular sample buildings are pre-packaged versions of the crushing and sampling portion of a multiple-stage sampling system housed in a modular-style building.
‘The main reason for packaging it in a building like this and then sending it out to the customer is that it is going to save them a lot of time, effort, and cost to install the equipment in the field,’ explained Adam Orner, product manager - sampling systems at McLanahan.
‘With this option, the crushing and secondary sampling portion of the system are already packaged in a building, so when it arrives on site, the customer simply has to place the building where it needs to go and then connect to the remainder of the system.’
The modular sample building is tailored to the application but will typically contain a sample crusher – a sampling hammermill crusher, sampling jaw crusher, or sampling roll crusher/sizer, reject conveyor, secondary sampling system such as a cross-belt sampler or falling-stream sampler, and sample collection buckets.
In a typical multi-stage sampling application involving a modular sample building, a sample is collected from a primary sampler located outside the building. This is conveyed through the roof of the building and fed to the sample crusher, which reduces the size of the particles in the sample and discharges them on to a conveyor, whereupon a secondary sampler collects a portion of the crushed material and discharges it into a sample-collection bucket, which is taken to the lab for further processing and testing.
‘In this case, we’re taking the first stage of sample size reduction and then the first stage of division and putting them into an automated system so the final sample mass is much smaller and easier to handle back at the lab,’ said Mr Orner.
Modular sample buildings come pre-wired with lighting as well as a heating, ventilation, and-air conditioning unit to maintain the temperature inside the building. For applications with hazardous-location ratings, the electrical components are explosion-proof.
On the exit end of the modular sample building, the end of the reject conveyor comes with a pre-installed belt that is rolled up for shipping. Once the remainder of the conveyor has been installed on site, the belt can be unrolled and strung through the conveyor.
‘Conveyors are often too long to ship as part of the building arrangement, so, to minimize installation, we try to do as much of the work in the shop as we can to minimize what needs to be done in the field,’ said Mr Orner.
Another key feature of McLanahan’s modular sample building is the integrated control room. This part of the building is separated from the equipment side by a sealed partition to maintain a dust-free environment for the controls.
In addition to the control panel, this part of the building typically contains a voltage transformer, HVAC unit, air compressor, and light fixture for visibility.
The top of the modular sample building typically features a platform for access to the sample crusher feed conveyor. The platform comes with removable handrails, for shipping purposes, and an access ladder with cage.
With all these features pre-designed, modular sample buildings offer a convenient, multi-stage, sampling solution. ‘This has been a fairly popular offering over the years, simply because it saves the customer time and money on the installation,’ said Mr Orner.