McCloskey machines play key role in success of south-east London recycling specialist
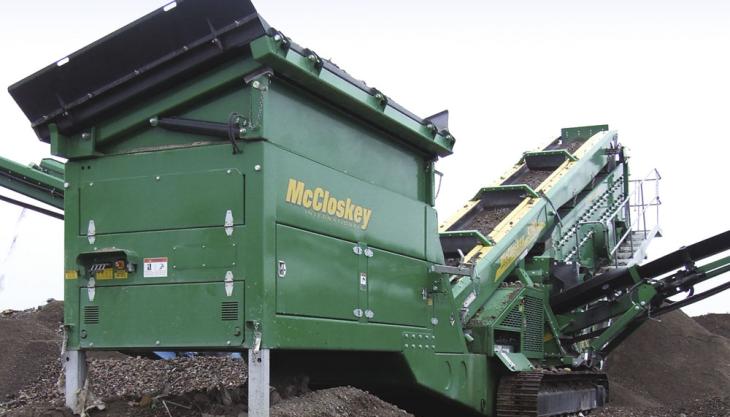
H. Sivyer choose McCloskey machines for their Greenwich depot
A south-east London waste management and recycling specialist explains their ongoing success in five simple words - meticulous management and McCloskey machines.
Given the current economic climate, any company enjoying growth and profitability has plenty to celebrate. Based in south-east London and operating from depots in Greenwich, Farnham and Oxford, H. Sivyer (Transport) Ltd are actively involved in waste management, waste removal and the production, haulage and delivery of recycled aggregates, primary aggregates and hydraulically bound materials (SMR).
George Frazer, recycling manager, said: ‘Ours must be one of the busiest recycling centres in the south east. And if that's in an unstable economic climate, we must be doing something very right.’
Meticulous management
George Frazer works from the two hectare Greenwich depot, and much of the site's efficiency is down to his meticulous, ex-military organization, together with his ability to constantly switch production from one product to another to meet client requirements. Almost all of the material to be recycled comes from utility companies at a rate of 10-12,000 tonnes a week involving over 200 vehicle movements a day.
The Greenwich site is divided into two parts; the A site deals with the really heavy material that needs to be processed before being brought into the B site for crushing and recycling. The 11-strong staff are all multi skilled and constantly change from machine to machine as needed.
Much of the yard is neatly stacked with stockpiles of clean and precisely sized material. And yet Frazer is remarkably modest about the efficiency with which the site operates.
He commented: ‘The secret of the smooth running of the site is being able to process the material properly, and having the right machinery to do just that.’
He reports that Sivyer diversified into recycling some three years ago, but on a much smaller scale. However, managing director Simon Siyver immediately realized the potential of recycling and dramatically increased the capability of the company to exploit the need to recycle rather than dump.
The company has tried a variety of manufacturers of recycling equipment, some have definitely not come up to the mark.
George Frazer said: ‘There is a lot of hype regarding the capabilities of some equipment and in particular the service back up. We have one crusher with a fault on a jacking leg that has not been rectified after two years. So it has been a pleasure to come across a company such as McCloskeys that not only have good machines but which have a superb service department as well.’
McCloskey machines
The first McCloskey machine used on the original site was a compact screener; a machine that made a good impression on Simon Siyver. But as the company has expanded operations, larger and more suitable McCloskey machines have been integrated into operations on the site. The company now runs a 36-tonne S190 triple-deck screener; a 34-tonne R155 vibrating screener; a 28-tonne 621RE trommel; and a TS3050 tracked stacker.
The R155 is used in conjunction with a jaw crusher and is either used to remove fines before material is fed into the crusher, or positioned under the crusher conveyor to produce a clean Type One (75-100mm) or similar product. The S190 is used as a stand-alone machine, producing a 10, 20 and 40mm product from the recycled crushed material. The 621RE screens the fines from the entire site, down to 7.0mm and produces such a clean material that one of the end products can be used as high-quality top soil.
‘All of the McCloskey machines are built to a very high standard; they are very sturdy machines. But it's the little things that show the real design and manufacturing quality, such as a light in the engine compartment for out-of-hours maintenance work, or two filler spouts to the fuel tank, one on either side of the machine, so it can be easily filled if backed into a tight space.’
However, no matter how well they are built, these machines all have to operate under severe conditions, and produce an accurate, consistent, and clean product. According to George Frazer, that’s precisely what the McCloskey machines do. ‘The reliability of the McCloskey equipment is second to none, and we like to keep it that way by checking everything, everyday on every machine,’ he concluded.
‘But when we have needed an engineer, the back-up is very, very good. They have never let us down and their response time is excellent.’