Kingfisher provide wear-resistant solutions to support zinc ore extraction
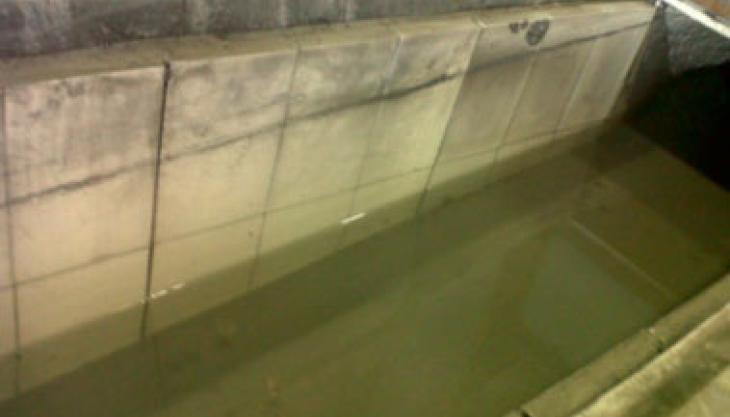
One of Europe’s largest mining conglomerates who specializes in the extraction of zinc, copper, and lead amongst other extractive minerals currently produces nearly 3 million tonnes of mined ore per annum resulting in the production of 400 tonnes of lead and zinc ore concentrate, are continually investing in the use of technologies to improve the performance of their operational process. One such example of continual improvement is in the review, trials and implementation of best practice towards the protection of process plant and equipment.
‘With the shear volume of tonnage mined aligned with the natural hardness characteristics of the mined ore, plant degradation is a consequence of the operation and is a significant factor in the decision making process of the capex investments on new equipment,’ commented John Connolly, managing director of Kingfisher Industrial.
In undertaking continual review and trials on surface protection technologies the plant managers and engineers are well positioned to identify what levels of protection are needed where, and what type of system fits certain applications. As with most things the possibility of a ‘one size fits all’ approach tends to be a short lived scenario, therefore the use of ceramic, metallic and polymer lining systems play their part in offering protection to plant and equipment used at the mined face through to the despatch point. To assist the engineers in this process the mining company engaged the services of Kingfisher in undertaking a bi-lateral approach to the many challenging issues they face during the continual development of plant-protection system enhancement.
Over a period of years, Kingfisher have engineered a range of systems that suit the varying types of wear and erosion that take place within the extraction and cleaning operations associated with mined ore. The use of traditional abrasion-resistant, quench and tempered plate, superior grades of carbide deposit plate and hard wearing castings encompassing varying amounts and grades of manganese, nickel and chrome constituents play an important part in protecting the structural integrity of expensive haulage equipment that if left unprotected would suffer from extreme wear.
The cyclical operation of primary and secondary crushing equipment alongside vibratory feeders, screen decks and grizzlies all encompass metallic protection systems that depend on their tensile strength and hardness properties to counter impact, compression, and sliding induced abrasion. These systems can be used to fabricate the equipment or can be used as sacrificial liners which can be replaced as and when required.
Once the mined ore is of the optimum size and grade the mineral is processed in a series of SAG or AG mills and then further refined through ball mills. This process of reduction utilizes the complete range of ceramic, metallic and polymer lining systems and each range of systems offers unique features and benefits over each other. The next phase of the process involves the milled slurry being screened, dewatered, separated and conveyed into the froth flotation plant for further refining. Screens, pumps, pipes, hydro cyclones, centrifuges, and wash launders are all protected using a combination of technologies that have differing wear characteristics to suit budget, service longevity expectations and asset value of the plant and machinery. To avoid settled slurry blockages the plant designers/engineers often prefer to have steep launders.
In working with the plant engineers Kingfisher have had success throughout the Irish-based plant and by using the plant as a live test bed, they have managed to fine tune what system suits the many different applications within the process.
From the use of 14mm thick K-CLAD chromium carbide wear plates protecting the post crusher screen decks in lieu of the traditional 20mm thick abrasion-resistant plate to the use of 20mm thick 92P K-ALOX ceramic liners protecting the high wear areas of the hydro cyclones and wash out launders Kingfisher have extended the performance of this equipment from months to years.
Likewise, the use of the company’s K-THANE polyurethane lining system has ensured the operational integrity of the back fill slurry tanks. A poorly designed or inadequate wear lining system incorporated within the pipelines and boreholes had resulted in the plant being forced to instigate the replacement of the existing steel structures due to excessive erosion and corrosion.
Deep mining or opencast mining for bulk solid material such as ore body can lead to a number of issues. The costs of non or incorrect action can lead to plant degradation, unplanned shutdowns, costly repairs and potential spillages leading to a breach of environmental legislation or worse still, an accident.