GE Recycled Aggregates invest in new Omega static jaw crusher
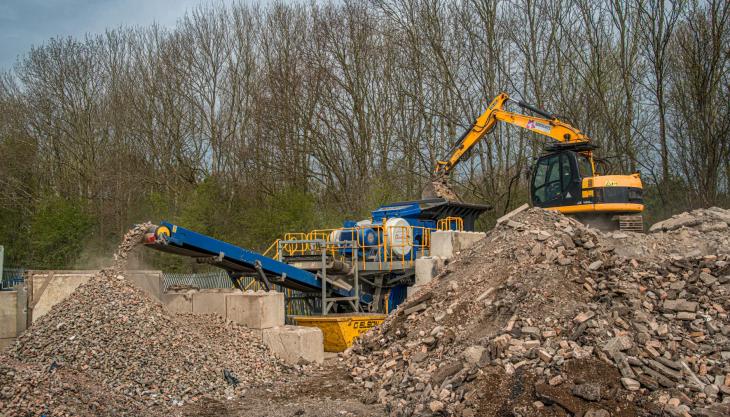
Diesel-electric powered J1065S proves a success for East Midlands aggregates firm
WHEN Loughborough-based GE Recycled Aggregates needed to invest in a new crusher for their recycling facility – the efficiency, simplicity, and compactness of the Omega J1065S static jaw crusher made it the number one choice for the business. The electric-drive crusher can be powered by either mains electricity or a diesel generator and has been impressing with its fuel efficiency and ease of maintenance.
The J1065S – the static model from Omega Crushing and Screening’s jaw crusher range – is one of a number of diesel-electric hybrid machines built by the Co. Tyrone-based manufacturer. ‘We chose the J1065S because it is more compact than our previous crusher and fits nicely in the corner of the yard,’ commented Gary Elson, managing director of GE Recycled Aggregates. ‘Despite its compact dimensions, the J1065S has the same size jaw as our previous machine, plus it is very easy to maintain.’
Mr Elson has also praised the jaw crusher’s ability to process stubborn waste materials, such as tarmac, asphalt, and concrete. ‘With its electric motor, we have found that it’s very good for crushing tarmac. The previous crusher would slow down when crushing tarmac, whereas the J1065S does not slow down at all,’ he added.
Although the company have chosen to run the crusher on diesel rather than electricity, the machine is still proving to be an economical investment. Based on diesel prices at the time of writing, the J1065S costs approximately £150 to run for a full working day, roughly half what the old machine had cost to run for the same amount of time. Once G E Recycled decide to switch the jaw crusher to mains electricity, further substantial fuel cost savings can be achieved.
The J1065S consists of the J1065 jaw crusher fitted in a modular assembly that includes a vibrating feeder with stepped grizzly section and galvanised walkways and handrails. The J1065S is suited to applications, such as municipal recycling and C&D waste-recycling or can be used as part of a quarrying or mining installation. The plant can even be set up inside a building, thanks to its ability to run emissions-free on mains power.
Omega’s machines all use the J1065 single toggle jaw crusher unit. The J1065 has a large feed opening of 1,000mm x 650mm, is driven by a 90kW (12hp) electric motor, and uses a simple drawback tensioning system. Other key features include a heavy-duty shaft equipped with premium bearings, a large jaw ejector cylinder, and a bolted mainframe, which provides strength and durability. An optional deflector plate can be added for recycling applications.
The J1065 crusher achieves an output of approximately 200 tonnes/h. And thanks to the higher throughout of the Omega unit, GE Recycled Aggregates are producing a larger volume of recycled products than ever before. ‘As a small family-firm, investing in the J1065S was a very big step for us but I’m very pleased with the machine,’ said Mr Elson.
Colin Daly, Omega’s sales director, added: ‘We are very pleased to have GE Recycled Aggregates on board as a customer. The J1065S is perfectly suited to their C&D waste-recycling operation, and the efficiency and simple design of the machine are sure to deliver a reduction in both fuel use and downtime.’