Failure is not an option for DMS
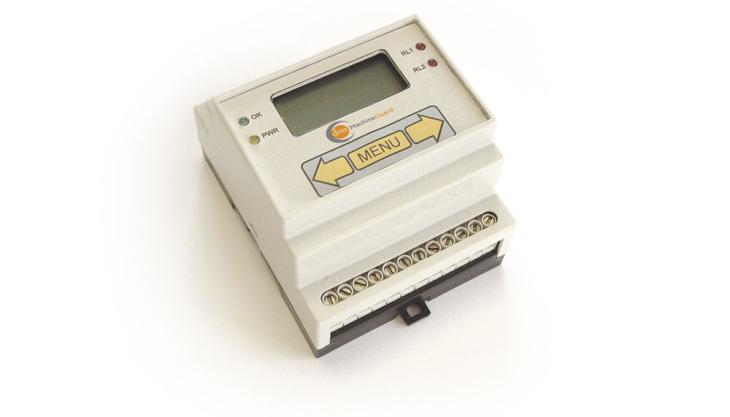
One source of downtime that is unacceptable in the mineral processing and quarrying sector is shredder drive arrangement failure. Such systems are notoriously difficult to monitor either periodically or continuously, but their failure can cause a plant to come to a complete standstill while the offending shaft-mounted gear reducer, AC motor and large shredder support-shaft bearings are repaired or replaced.
After a number of serious failures occurred on four shredder drive arrangements on two sand crushers, a major UK aggregates company decided to seek a better solution and implement a ‘live’ condition-based monitoring system to help predict and prevent further failures. This was the challenge that the company set Drive Management Services (DMS).
On discussing the requirements with the site’s maintenance manager, it was agreed that the following key components would be needed if the solution was to prove effective:
- continuous monitoring 24 hours a day
- multi-level complex alarms to identify specific events
- wireless communication (shredder drive arrangement is situated 800m from the office)
- simple, effective and easy-to-interpret information delivered in real time.
In addition, the system had to be affordable and not cost-prohibitive in operation. After reviewing these specific requirements, DMS recommended implementation of their MachineGuard condition-based monitoring system.
For this particular application, MachineGuard was installed to monitor three critical items of plant:
- shredder motors (monitoring the motor DE and NDE bearings)
- shredder shaft-mounted gear reducers (monitoring in three planes – horizontal, vertical and axial)
- shredder support-shaft bearing pedestals (monitoring both bearings).
The software ‘control panel’ for MachineGuard was installed on a PC in the engineering office and the system was set up to warn plant operators of potential problems by means of a series of simple local alarms, such as flashing lights inside the control room while sending a text message warning to the engineering manager’s mobile phone.
By setting up the system in this way, the customer has been given full control of the monitoring system and instant access to ‘up to the minute’ data on the condition-critical plant. Moreover, the customer has the ability to interface the MachineGuard system with the latest web-based publishing software, allowing designated persons to log on (via the Internet) and view the live data being collected on any PC. This also allows DMS to review the data in question and offer their expert opinion while discussing the live application with the customer.
During August 2011, the level of vibration on the aggregate company’s critical shredder drive shaft-mounted gear reducers started to increase significantly, reaching 30mm/s or more in certain load conditions. This was investigated at the next available maintenance window to assess the condition of the drive arrangement. On close inspection it was noted that the mounting-feet brackets on the shaft-mounted gear reducer had damaged the spacers located between the bracket and the gear reducer mounting face.
The spacers had virtually disintegrated leaving the whole assembly to move both axially and radially, causing the extremely, high and damaging vibration levels. By detecting the fault early enough, this intervention allowed the client to plan for new spacers to be located and fitted within the 2h maintenance window, thereby reducing any unplanned downtime and saving the gear reducer from any potential long-term damage.
The maintenance manager at the site commented: ‘It is possible that this incident was a repeat of the events that may have led to the failure of the previous shredder shaft- mounted gear reducers – except this time we had the benefit of DMS’s MachineGuard system. As a result, we not only avoided the inevitable disruption caused by such a serious failure, but also any consequential damage costs.’