Aggregate Industries receive dose of preventative maintenance
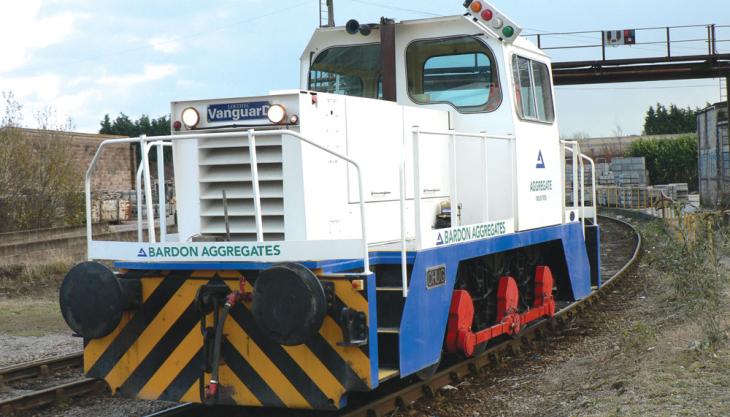
A recently refurbished locomotive (pictured right), operated by Aggregate Industries, is reaping the benefits of a centralized lubrication system, as part of the company’s preventative maintenance programme.
Leicester-based Lube-Spec Ltd, specialists in lubrication systems, were contacted about specifying a solution and recommended the Beka-Max EP1 progressive system, primarily for health and safety reasons.
There are around 50 lubrication points on the locomotive and due, to the location and height of some of the points, this posed a safety issue for the engineer who would have to climb, crawl, and carry equipment in confined spaces for manual greasing. Manual lubrication also incurs cost and downtime, and is often not reliable.
David Mills, an engineer at Aggregates Industries’ Croft Quarry, commented: ‘Even with high-pressure pumping, it is difficult to get grease into a close-fitting bearing, as some surface areas will be in contact with each other under the weight of the machine. This often leads to a lack of effective protective lubricant between the working faces, which increases the risk of accelerated bearing wear.’
The Beka-Max EP1 system feeds all the lubrication points on the loco via a special link arrangement connecting the wheel-rod bearings. This reduces the maintenance cost of replacing bearings through extended bearing life, minimizes downtime by eliminating manual lubrication and, most importantly, improves the safety of operations on the engine.
As a result, Aggregate Industries are now able to transport materials by rail more efficiently, thanks to increased running time of their locomotives.
Lube-Spec Ltd, 42 Edward Avenue, Leicester LE3 2PD; tel: (0116) 2897 982; fax: (0116) 2248 023.
Leicester-based Lube-Spec Ltd, specialists in lubrication systems, were contacted about specifying a solution and recommended the Beka-Max EP1 progressive system, primarily for health and safety reasons.
There are around 50 lubrication points on the locomotive and due, to the location and height of some of the points, this posed a safety issue for the engineer who would have to climb, crawl, and carry equipment in confined spaces for manual greasing. Manual lubrication also incurs cost and downtime, and is often not reliable.
David Mills, an engineer at Aggregates Industries’ Croft Quarry, commented: ‘Even with high-pressure pumping, it is difficult to get grease into a close-fitting bearing, as some surface areas will be in contact with each other under the weight of the machine. This often leads to a lack of effective protective lubricant between the working faces, which increases the risk of accelerated bearing wear.’
The Beka-Max EP1 system feeds all the lubrication points on the loco via a special link arrangement connecting the wheel-rod bearings. This reduces the maintenance cost of replacing bearings through extended bearing life, minimizes downtime by eliminating manual lubrication and, most importantly, improves the safety of operations on the engine.
As a result, Aggregate Industries are now able to transport materials by rail more efficiently, thanks to increased running time of their locomotives.
Lube-Spec Ltd, 42 Edward Avenue, Leicester LE3 2PD; tel: (0116) 2897 982; fax: (0116) 2248 023.