Benninghoven’s Biggest UK Project
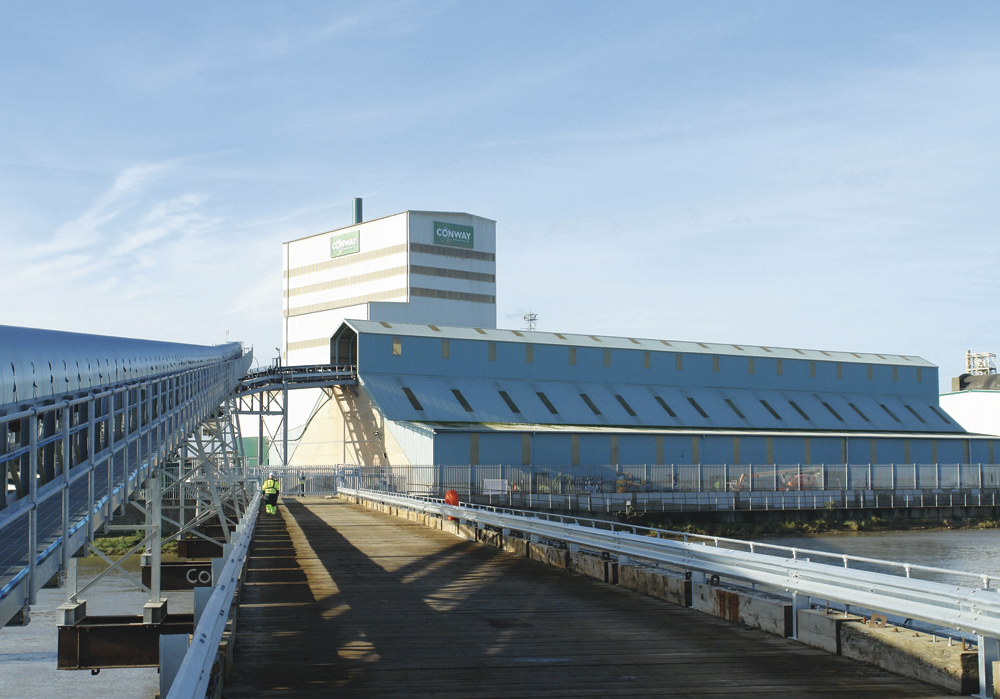
New asphalt production facility and wharf complex on the Thames for FM Conway
In November 2010, FM Conway, the Dartford-based highways maintenance, civil engineering and paving service providers, officially opened their £10 million asphalt plant and wharf complex on the river Thames, at Erith, in Kent. The event marked the culmination of months of planning, site preparation and building work to achieve what is today one of the largest and most technically advanced asphalt production sites in the UK.
The project centred round a new state-of-the-art Benninghoven BA5000U asphalt coating plant equipped with a 5,000kg mixer and a high-level hot recycling system. This design met all the required mix specifications, together with all the necessary environmental criteria. The plant has a production output rated at 320 tonnes/h of dense basecourse, at 5% initial moisture, with an additional 200 tonnes/h recycling capability.
For plant manufacturers Benninghoven, it was the largest single project of its kind to be undertaken in the UK to date. Designed to provide significant operational benefits and cost savings, the new plant is able to produce a wide range of high-specification coated materials, including modern thin surfacings, stone-mastic asphalts and other specialized mixes.
Before the development could commence, the tight- footprint, four-acre, former CEMEX site had to be cleared to allow foundation and piling work to be carried out. Thanks to careful forward planning and effective project management, the various civils were completed on schedule.
Commenting on the development, Michael Conway, chief executive officer of FM Conway, said: ‘The opening of this facility is a testament to what FM Conway have achieved in their 50 years of trading, growing to become one of the UK’s leading integrated service providers.’
Asphalt plant
All units in the asphalt production process are housed in a fully sheeted, factory-style building to aid insulation and help reduce noise levels. The plant features a five-person lift on the outside of the tower, which gives easy access to all five levels of the plant for maintenance etc.
The aggregate cold-feed system comprises 10 units arranged in two lines of five, each of 14m3 capacity and fitted with a frequency-controlled belt feeder for accurate blending of the aggregates. Two of the hoppers are for sand and fines and are equipped with hopper wall vibrators to ease material flow. All the hoppers are sheeted on their sides, ends and roofs, with an extended canopy over the sand hoppers.
A full-length concrete retaining wall supports the feed ramp, with the bulk of the aggregates stored in large covered storage bays that hold approximately 24,000 tonnes of material. Where permitted, reclaimed asphalt pavement (RAP) from Conway’s own operations is used in the asphalt production process.
Two 24m long collecting conveyors move material on to a 10m long x 800mm wide inclined dryer feed conveyor, which, in turn, discharges on to a short 3.5m long reversible slinger conveyor from which material is fed directly into the dryer drum.
The aggregate dryer drum, which measures 2.8m in diameter x 10m in length, is fully insulated and aluminium clad for heat retention and noise reduction. The drum is friction driven by four support rollers through individual 22kW geared motor units.
The burner is a Benninghoven Rax Jet Oil EG4-FU type, which can burn both gas oil and natural gas. This is equipped with a full range of operating and safety devices to deliver high-efficiency fuel usage. An air-inlet silencer is connected to the burner to suppress noise levels.
The plant’s dust-collection system, sized for the dryer unit and mixing section scavenging, is rated at 95,000Nm3/h and achieves emission levels of less than 25mg/m3. A primary skimmer unit mounted alongside the dryer separates any coarse dust from the airstream, which passes to the hot-stone elevator feed boot via a gravity flap valve and chute. A secondary cassette-type bag-filter system collects any remaining dust and transfers it, via two screw conveyors, to a filler elevator. Dust is also collected from nuisance points at the screen, weigh hoppers and elevator. A dust monitor mounted on the plant’s 41.5m high exhaust stack provides a remote readout in the operator’s cabin. As a result of such measures, the plant is said to meet the most stringent dust-control regulations.
Any excess dust collected can be discharged from the reclaimed dust silo through a rotary valve into a twin-shaft paddle conditioner where water is introduced, thereby providing an environmentally friendly method of purging this reclaimed dust.
Hot aggregates are transported from the dryer up to the screen by a vertical bucket-type elevator. Elevator drive is by means of a 50kW geared motor and toothed chain wheels at the elevator head. The elevator features externally located bearings and a safety backstop facility, while a wide platform provides easy access for maintenance.
Material discharged from the elevator passes into a six-deck screen which features twin-shaft drive via two ‘bolt-on’ 19kW low-maintenance vibrating motors. These drive units are mounted outside the screen housing to allow the high-temperature screening of materials. Wide access doors together with a roll-away chute provide access to all screen decks.
The hot-storage section has a total capacity of 160 tonnes and comprises six bins. All of the bins are insulated and clad, and each is fitted with continuous level indicators and an overflow chute. Discharge is by a pneumatically operated radial door, which accurately regulates material flow to the aggregate weigh hopper, from where the aggregates are discharged directly into the mixer.
Accurate weighing of ingredients is achieved by separate load-cell-mounted weigh hoppers, including a 5,000kg capacity aggregate hopper, an 800kg filler hopper and a 600-litre capacity weigh vessel for bitumen. Mixing takes place in an insulated, 5,000kg capacity, twin-shaft paddle mixer, with drive provided by two 75kW geared motor units through synchronized gears. A rapid and thorough mixing cycle is achieved by the mixer’s efficient paddle arrangement, while a radiation pyrometer is situated at the mixer discharge to indicate mix temperature.
Mixed material discharged from the mixer falls into a 5,000kg skip unit which runs on horizontal tracks and distributes the material into a 600-tonne capacity silo, arranged in six compartments of 100 tonnes each. All are fitted with high-level warning indicators and are insulated and fitted with electric trace heating around the discharge doors. A direct load-out hopper is positioned beneath the mixer and all bins are mounted on load-cells to ensure accurate material loading.
Bitumen is stored adjacent to the plant in three 80m3 capacity vertical tanks and one split 70m3 capacity tank; these are Benninghoven’s high thermal efficiency units, which deliver low running costs due to their stepped heating system design. An inbuilt loading system with high-level probes offers fail-safe filling with no possibility of spillage.
Filler is stored in an external three-compartment vertical silo holding approximately 85m3 of reclaimed filler and 55m3 of imported filler, with a further 55m3 storage for hydrated lime. All the silos are equipped with level indicators and shut-off valves.
A gravimetric additive system is also incorporated within the plant to feed granulated material from a 30m3 silo. Each batch of granulate is accurately weighed in a load-cell-mounted weigh hopper before being discharged through a butterfly valve to the mixer. A similar specification silo for pigment is sited alongside.
Recycling system
The heart of the recycling system is a 2.8m x 12m long parallel-flow drum which both dries and heats the recycled asphalt. The internal design of the drum ensures the burner flame makes no direct contact with the moving reclaimed material within the drum. The combustion zone of the drum is fitted with special heavy-duty, self-cleaning finger lifters that vibrate during the production process to prevent clogging of the material.
Graded and tested RAP material fed to the recycling drum comes from one of three hoppers, depending on the mix. Discharge from the hoppers is by belt feeder on to a short inclined conveyor feeding an elevator. The elevator is of the bucket type and transports the material up to drum level. Feed into the drum is by a short conveyor running beneath the burner.
Hot recycled material discharged from the drum is held in a 25-tonne electrically heated surge hopper prior to being discharged into a load-cell-mounted weigh hopper, where it is batch weighed before entering the mixing cycle. The hot recycled material then travels through a specially designed RAP chute, which feeds material directly into the plant’s paddle mixer. The chute features stainless steel liners and an internal spray system to keep the sticky material on the move.
Inside the paddle mixer, the dried and heated recycled materials are blended with conventionally produced materials at various percentages. The plant is controlled by a Benninghoven on-line Batcher 3000 computer system which displays all plant functions via colour graphics. The modern-linked system, which is housed in a purpose-built two-storey office block for production and sales personnel, overlooks the plant and has storage for up to 500 asphalt mix recipes. Asphalt from the plant has been used on several prestigious projects, such as London’s cycle superhighway, Dover docks and the Olympic site.
Wharf complex
Following the completion of the asphalt plant phase, the next development involved upgrading the jetty area in order to utilize the Thames waterway for transport. The wharf and jetty, which extends 130m into the river, has been designed to berth ships of up to 6,000 tonnes. A bespoke conveyor system (also built and installed by Benninghoven) consisting of a track-mounted feed hopper and a short horizontal conveyor discharging on to a 140.5m long inclined jetty conveyor, feeds the storage building. An existing overhead tripper conveyor was utilized, after modification, to feed the storage bays, with the unloading system controlled via wireless technology by the dock crane operator.
The new facility allows FM Conway to provide a comprehensive and efficient service to their main markets throughout the South East, while use of the wharf ensures minimal environmental impact by taking 15,000 truck movements off the road every year and saving around 1,025 tonnes of CO2.
ACKNOWLEDGEMENTS
Thanks are due to Michael Conway, chief executive officer of FM Conway, Tim Metcalf, general manager FM Conway Aggregate and Asphalt, and Nigel Moreton of Benninghoven UK Ltd for their help in preparing this report.