New asphalt plant for Cauldon Low
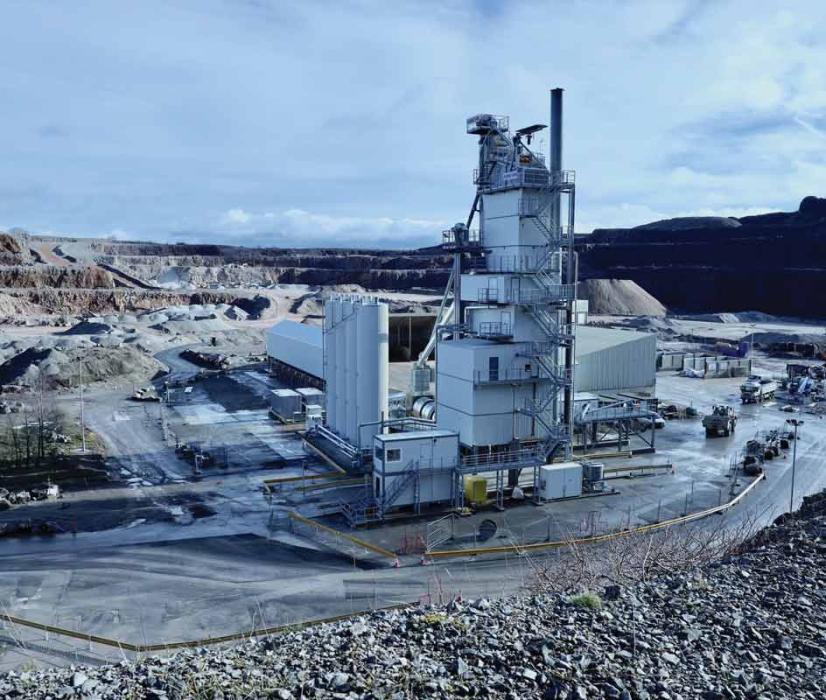
First published in the March 2024 issue of Quarry Management
Aggregate Industries invest in state-of-the-art Ammann ABP 240 Universal asphalt plant
Aggregate Industries have reinstated asphalt production at Cauldon Low Quarry, in Staffordshire, following a major multi-million-pound investment in a brand-new, state-of-the-art asphalt mixing plant. Having acquired Cauldon Low from Tarmac in 2015 as part of the global merger between Lafarge and Holcim, the new plant has been plant built on the same site as the former Tarmac asphalt production operation. Serving markets in Derbyshire and Staffordshire, along the M6 corridor, as well as parts of Warwickshire, it will help bolster Aggregate Industries’ Haughmond Hill Quarry, near Shrewsbury, and Topley Pike Quarry, near Buxton, where future asphalt supplies are constrained.
Having received approval in November 2022, the project was put out to tender and Ammann were selected as the preferred bidder. Aggregate Industries chose to invest in the well-known Ammann ABP Universal mixing plant, which is noted for its high capacity, reliability, flexibility, efficiency, safety, and sustainability. Offering plenty of potential for customization through numerous options and easy integration of future technologies, the ABP 240 model specified by Aggregate Industries is capable of outputs up to 240 tonnes/h. With the order placed in December 2022, the build commenced in April 2023 and the first material was produced on 20 December. Since then, final commissioning and plant and product testing has been undertaken with full production expected to commence at the end of February.
New plant
The new pre-feed system comprises 10 covered cold-feed hoppers arranged in line, each with a capacity of 20m3, together with two covered RAP hoppers. Recycled asphalt planings and virgin aggregate feedstocks, which comprise limestone from Cauldon Low Quarry as well as imported high-PSV stone and sand, are kept in a series of storage bays adjacent to the cold feeders, with charging of the hoppers carried out by wheel loader.
Dosing belts beneath the main cold feed hoppers discharge the correct proportion of materials on to a covered collection and transfer belt which, in turn, discharges on to the dryer drum’s reversible feed belt. Separate transfer belts from the two RAP hoppers deliver the recycled material to the dryer drum or, via an elevator, straight to the mixer, as required. All the conveyors involved are equipped with energy-efficient variable-speed drives.
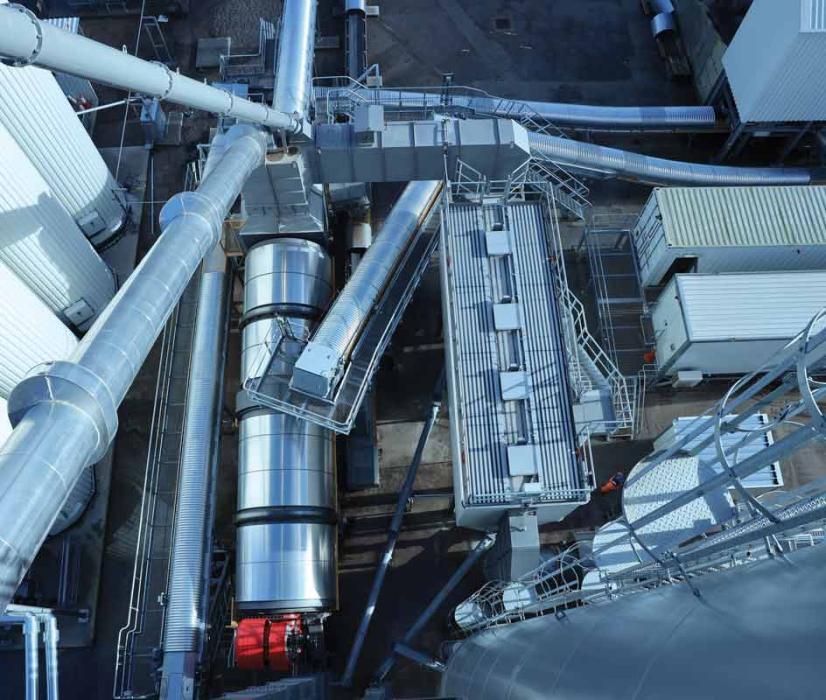
Drying and heating of the materials takes place in a fully insulated, 11m long x 2.7m diameter counterflow drum equipped with Ammann’s unique RAH50 central inlet ring to allow the introduction of up to 50% cold RAP to the dryer. Heat is provided by a 19.8MW Oertli Induflame MIB-6.12 dual-fuel burner which currently runs on light fuel oil pumped from a 50m3 capacity tank. Like the conveyors, the use of VSDs on the dryer drum allows for easy adjustment of dwell times by speeding up or slowing down the drum. Meanwhile, the plant’s dust-filtration system reclaims filler dust from the burner’s exhaust gas, with the cleaned gas and steam returned to atmosphere via an 83,000Nm3/h capacity exhaust fan and 39m high stack equipped with an odour-neutralization system.
From the drum, the dried and heated aggregates are sent, via a 38m hot-material elevator, to a fully enclosed, six-deck vibrating screen with a total screen area of 52m2. The various grain sizes are discharged into the appropriate chamber of the hot mineral silo, with any dust generated by the screening process vented back to the dust-filtration system. The hot mineral silo has six chambers plus a bypass bin, allowing the plant to hold up to 200 tonnes. All the aggregate chambers are equipped with continuous level sensors and temperature sensors where appropriate. Dosing flaps portion the aggregate components, as defined by the required recipe, with their weight determined by the mineral scale, ready for discharge into the mixer.
A similar weighing procedure is carried out for bitumen and filler, with any further additives (fibres, fluxes etc) determined by either weight or volume. With four 100-tonne bitumen tanks, all equipped to RBA standards with appropriate alarms and interlocks, the new Cauldon Low plant is well equipped to handle a range of bitumen products. Fillers are also well catered for with a single 3.2m diameter vertical silo divided into two for both reclaimed filler (90m3 lower silo) and imported filler (80m3 upper silo).
Mixing of the weighed components takes place in the Universal plant’s state-of-the-art, 4,000kg capacity AMIX-2.40 twin-shaft compulsory mixer, with steam evacuation from the mixing process monitored by moisture probes, whilst an infrared sensor measures the asphalt temperature at the mixer outlet. An ‘x-y’ transfer skip arrangement with heated outlet slide delivers the mixed asphalt products to the 400-tonne capacity hot storage section, which consists of four mixed-material compartments, together with one direct discharge bin and one oversize/overflow compartment.
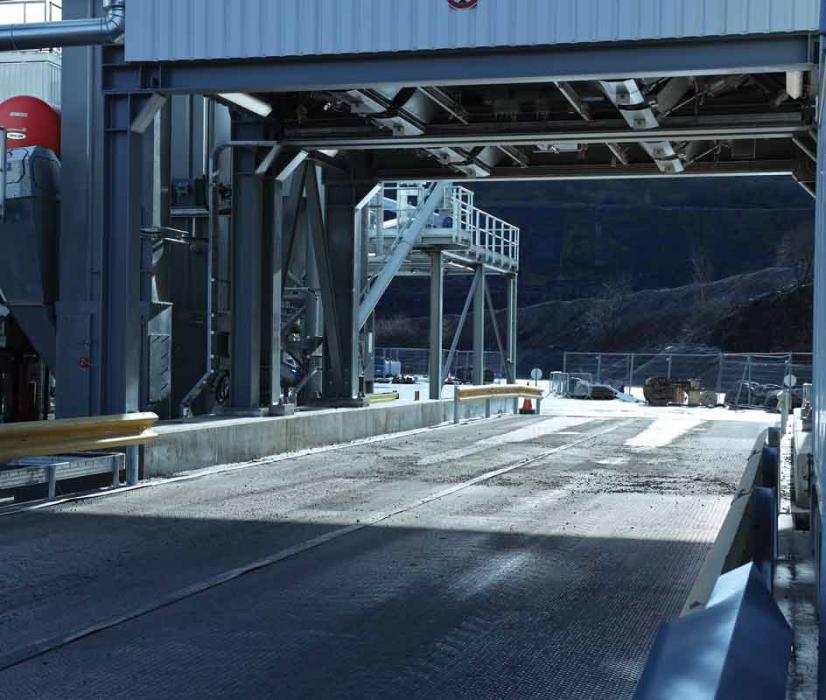
The loading out of finished asphalt products takes place over a 28m x 3m surface-mounted Eurodeck heavy-duty modular weighbridge supplied by Weightron Bilanciai. This communicates with Ammann’s as1 control system, allowing for accurate management of vehicle tare and gross weights and eliminating any overloading.
Plant control
Plant control is via Ammann’s future-oriented as1 system, which combines the company’s proven software with tried-and-tested industrial hardware to provide comprehensive system functionality with optimized networking and administration. The system at Cauldon Low incorporates several new and recent Ammann software developments, including the Argon View interface, along with EcoView and PIP (Plant Information Point) modules.
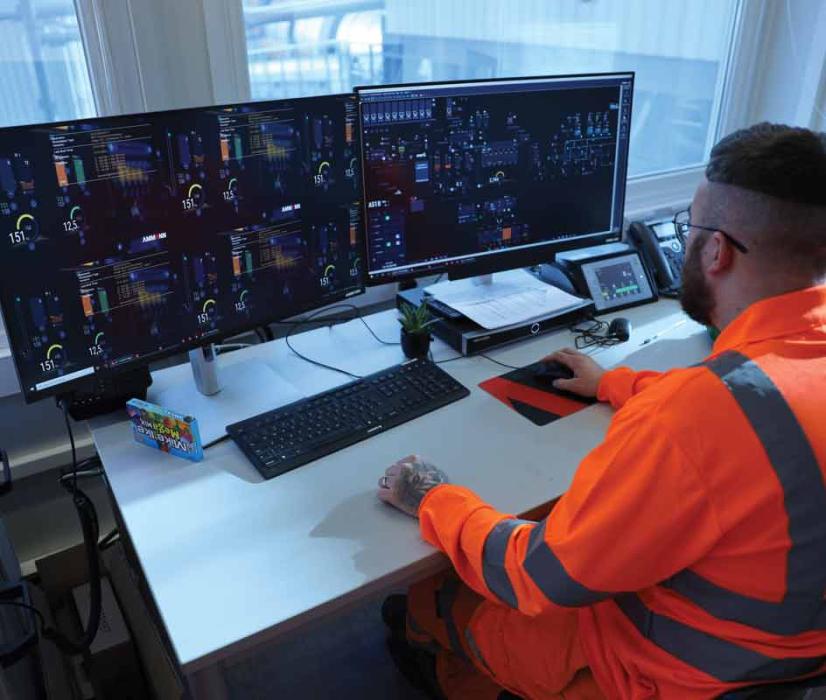
Argon View is a user-friendly interface for the as1 control system which offers both daytime and night-time viewing modes. Providing constant visual updates and animations about production status, the intuitive, simple-to-use interface helps operators track the entirety of the production process, improving efficiency and productivity. Parts that are not needed for the current production are dynamically hidden or discretely placed in the background, ensuring an optimal view of the essentials at all times, whilst drag-and-drop techniques for selections as well as sliders for setpoint pre-sets and other new controls assist the operator in their work.
The EcoView module serves to optimize production from an ecological and economic perspective. Operating data are continuously recorded and presented in condensed form, providing the plant operator with information on energy consumption, energy costs and CO2 emission values per tonne of mixed material produced. By comparing this with historical data or target values, trends and required actions can be identified to promote energy-optimized plant operation and help eliminate energy wastage.
Meanwhile, the PIP module provides both operators and customers with access to key plant data at any time and from anywhere. Information such as daily production quantities, the latest production details, and the status of the plant are uploaded to the Ammann cloud and can be accessed from any location, using a browser on the desktop, tablet or smartphone.
Acknowledgement
The editor would like to thank Aggregate Industries for permission to visit the site. Thanks are also due to Cauldon Low asphalt plant manager Jason Fairbrother and Ammann UK managing director David Hunt for their help in the preparation of this article.
Subscribe to Quarry Management, the monthly journal for the mineral products industry, to read articles before they appear on Agg-Net.com