On-site Asphalt Innovation Helps Combat Potholes
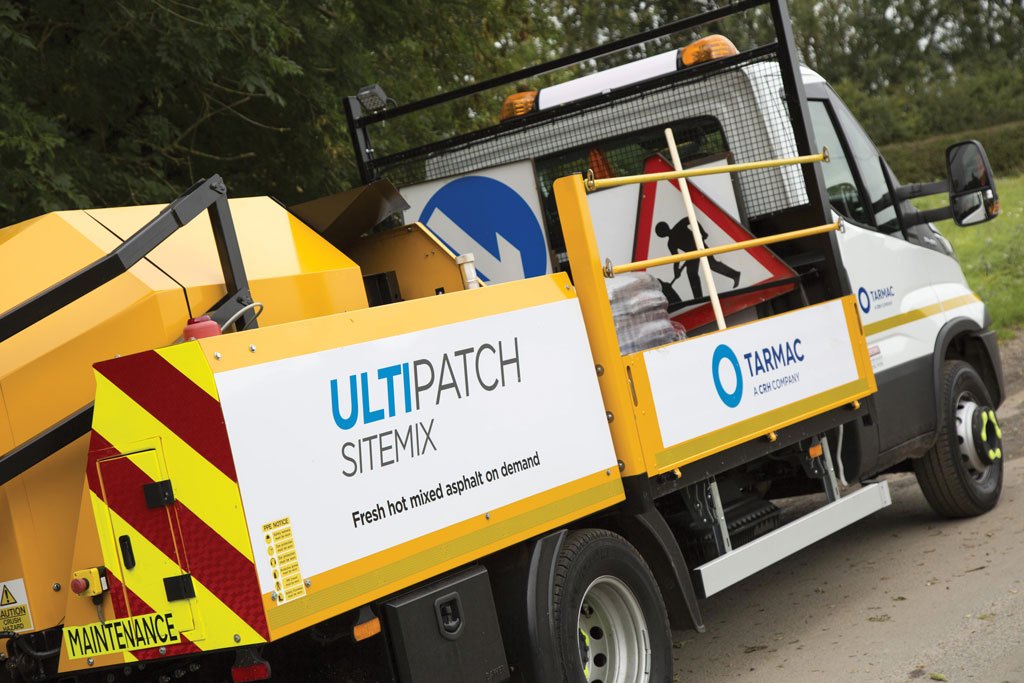
First published in the January 2019 issue of Quarry Management as Perfect Patching
A collaboration between Tarmac, Amey, RSL Fabrication and ND Brown has optimized low-volume asphalt heater technology to deliver advancements in bagged asphalt materials and a new and commercially viable alternative to using bulk hot mix asphalt for minor highways defects and utility reinstatements. Brian Kent, technical director at Tarmac, explains how this end-to-end solution increases the quality, efficiency and workability of bagged asphalt while reducing costs and waste compared with traditional methods.
As the wintry weather descends across our shores, the perennial issue of the condition of the UK’s roads inevitably begins to fuel the national conversation. Up and down the country, the state of local highways is never far from the top of the political and public agenda.
Earlier this year, the RAC published data revealing that pothole-related breakdowns had reached a three-year high. Recognizing the extent of the issue, Chancellor Philip Hammond announced in the Autumn Budget that an additional £420 million would be made available to local councils to help tackle the issue.
With local councils repairing potholes on average every 21 seconds, new innovations in asphalt and heater technology have the power to deliver a more efficient and productive solution for undertaking minor highways repairs and potentially help to proactively target the most at-risk areas.
Wastage: identifying a solution
The quantity of asphalt required for small hot asphalt patching has traditionally created intermittent supply and quality issues. Patching works are undertaken around the clock and arranging collection for small quantities of asphalt can be time-consuming and restrictive.
Having asphalt collected on small trucks in up to 3-tonne quantities can also result in a high proportion of that collected product being wasted due to the material chilling before use, leading to many customers deliberately over-ordering to allow for an extra contingency.
Very high temperatures of between 170°C and 190°C are generally required to mix hot asphalt. When mixed and stored at normal production temperatures for a prolonged period, the bitumen binder can suffer from ‘ageing’, which results in hardening. This reduces the material’s workability and can adversely impact on durability.
To put this into context, after 24 hours of hot storage in a depot hotbox the asphalt binder penetration may have reduced by about 50%. After 48 hours this figure drops to around just 20% of the original value.
The workability of the asphalt also reduces as material temperatures fall, becoming more difficult to spread and compact. This means operatives must often take the difficult decision as to whether to scrap the remaining asphalt or to attempt to lay the material, which can result in inadequate compaction that can affect long-term performance.
Material innovation
Tarmac set out to develop a bagged asphalt product that could give the equivalent performance of fresh plant-mixed asphalt and be compliant with standard specifications. This equally had to deliver a lower compaction temperature technology to reduce reheating time and overcome any quality concerns over potential detrimental impact on the bitumen during on-site reheating of the product.
Tarmac’s solution, Ultipatch Sitemix, is a product that does not have to be heated to such a high temperature as alternative asphalts, resulting in reduced fuel usage, lower carbon emissions and less binder hardening.
The material is ready for installation when it has been heated to a temperature of typically 130°C, compared with alternatives that require heating to higher temperatures. Also, it has safety advantages by reducing the operative risks associated with handling hotter materials.
Heating time can typically be 50% less than alternative site-mix materials and this, in addition to a 30% CO2 reduction during the initial manufacturing process, delivers environmental benefits as well as enhanced durability.
Laboratory trials followed by full plant testing have demonstrated that the asphalt meets all required specification and user criteria, both as a bulk asphalt and in smaller, pre-packed 20kg bags.
In parallel, Tarmac and Amey worked collaboratively with RSL Fabrications and ND Brown to develop and refine mobile heater technology. By mixing materials for minor highways defects on site, rather than transporting material which may have spent considerable time in storage, any loss of bitumen performance due to hardening is eliminated.
In 2015 Amey first trialled low-volume asphalt heaters with a 250kg batch capacity in the North West, and continued to refine their designs to deliver a safe process which quickly delivers a durable end product in situ. The equipment is also able to log data and provide a full auditable trail of the temperature of the material, using GPS technology to record the location, time and date of works.
Delivering benefits
Increased collaboration is providing project partners with the opportunity to link up complementary innovation across the supply chain for the benefit of customers. The new innovations in on-site heater technology combined with advances in bagged asphalt have the ability to deliver significant cost benefits and overcome the challenges relating to completing small-volume, one-time, hot permanent repairs for minor highway defects and utility reinstatements.
As a freshly mixed product, Ultipatch Sitemix can deliver better performance and durability than conventional asphalt, eliminating any loss of bitumen performance in the mixing and storage process to deliver fresh asphalt at the point of use. It also eliminates the material wastage incurred by transporting larger volumes to site from asphalt plants and reduces total vehicle movements.
This new approach equally means that asphalt for small network defects can be available 24 hours a day, seven days a week. By reducing the reliance on plants that are required to be open to access supplies of asphalt, it allows works to be carried out during antisocial hours and minimizes disruption for road users during the working day.
The socio-economic importance of a high-quality, well-maintained road network should never be underestimated, and we will have to wait until the spring to understand what the full impact of this winter’s weather will be on our highways network.
However, by continuing to collaborate across the supply chain, it remains possible to bring forward innovations in materials that can overcome industry challenges while at the same time cutting costs and waste.
- Subscribe to Quarry Management, the monthly journal for the mineral products industry, to read articles before they appear on Agg-Net.com