First UK Stationary Crushing & Screening Plant Installation for Sandvik
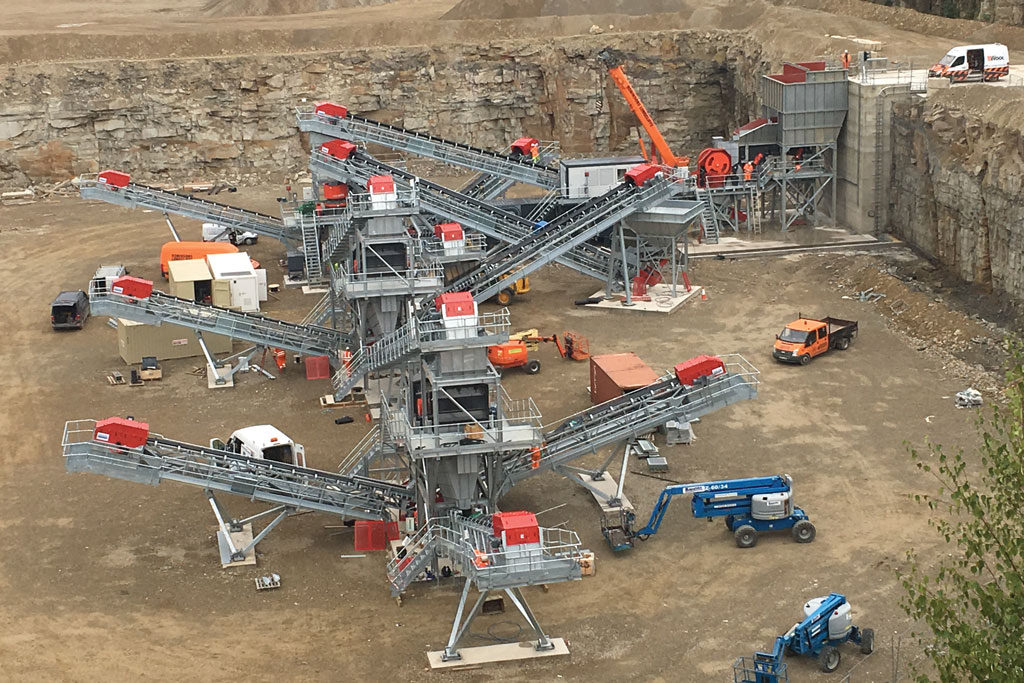
First published in the February 2019 issue of Quarry Management as A UK ‘First’ for Sandvik
Sandvik Mining and Rock Technology install first of a kind stationary crushing and screening plant for the UK market
Last year Sandvik Mining and Rock Technology held an exclusive open day (5 October 2018) at Marshall’s Howley Park Quarry, in Dewsbury, near Leeds. The highly successful event attracted around 60 visitors with end-user customers and major dealers in attendance from all around the UK.
The Sandvik customer open day not only officially marked the launch of the company’s first fixed aggregates processing plant in the UK for Marshalls, one of the country’s leading hard landscaping manufacturers, but also served as a platform to create greater customer awareness of its wider product portfolio and latest offerings and innovations in the marketplace.
Sandvik currently offer their UK customer base three purchasing options for fixed crushing and screening equipment, providing aggregate producers with the opportunity to acquire a high-performance plant that matches their specific needs and budgets.
The plant offerings, available from the company’s Plant Solutions division, are: FastPlant – a pre-defined plant solution with a fast delivery time of just 12 weeks; SmartPlant – an advanced modular plant solution based on Sandvik SmartStations; and CustomPlant – a long-term plant partnership to create the optimal plant solution for the customer.
According to Mark Bodell, sales manager – stationary crushing and screening for England and Wales, at Sandvik Mining and Rock Technology, the importance of supplying fully customizable modular plant solutions to help customers manage their machinery assets and associated costs is growing more than ever.
‘With material producers striving to reduce their operational costs, make efficiency gains and optimize productivity, equipment-management packages are increasing in popularity across the industry,’ he commented.
‘CustomPlant was the approach taken by Marshalls to deliver a fully bespoke and individually designed installation at Howley Park. From day one Marshalls made it clear it was not just about being supplied with the equipment, but a long-term partnership whereby our engineers work closely with them during all phases, from specification to commissioning, to create a fixed processing plant that delivers maximum productivity, reliability and uptime.’
The highly engineered turnkey system at Howley Park Quarry has been configured to a bespoke layout, bringing together modular units to create a tailor-made solution to meet the customer’s exact requirements for business expansion. Although Sandvik have sold stationary plants similar to the one at Marshall’s Howley Park for over two decades all around the world, this recent installation marks a significant step forward in the UK market.
‘In the past Sandvik were known in the UK for supplying high-quality, major components and ancillary parts for fixed plant,’ said Mr Bodell. ‘But our core focus has now changed to delivering a fully designed, manufactured and installed plant; the Howley Park project being a prime example of this offering.
‘The modern plant highlights not only Sandvik’s capabilities in developing and supplying high-productivity solutions to meet the most demanding of aggregate producers, but also the partnership approach with customers to fulfil their exact requirements.’
The activities laid on during the Sandvik open day allowed attendees to see the aggregate processing plant at first hand and learn more about its features and benefits, particularly the built-in safety systems and quick and safe access to all service points.
The new plant
Capable of accepting a feed size from 0–700mm, the new plant has a nominal processing capacity of 350 tonnes/h and is designed to deliver seven final products: 0–40mm, 40–75mm, 75–200mm, 20–40mm (or 14–20mm), 0–6mm, 6–10mm and 10–20mm (or 10–14mm).
The blasted sandstone feed material, which has a bulk density of 1.6 tonnes/m3, is delivered to the plant by dumptruck and discharged into a frame-mounted, 40m3 live volume, reinforced-steel feed hopper. This provides a constant feed supply to the plant’s primary crushing unit, which comprises a Sandvik ST1263 vibratory pan feeder/grizzly screen combination and Sandvik CJ411 single-toggle primary jaw crusher.
The abrasion-resistant pan feeder (ST1241) and two-deck, linear-motion grizzly screen (ST1222), which has a stepped grizzly top deck and a steel wire mesh bottom deck, are both driven by a pair of 8kW unbalanced vibratory motors, whilst the jaw crusher, which has a feed opening of 1,050mm x 800mm, is powered by a 110kW squirrel-cage motor via V-belt drive. A pedestal-mounted boom breaker system equipped with a Sandvik BR555 hydraulic hammer has been fitted to deal with any crusher blockages.
The primary crushed material is delivered, via a 31m long x 800mm wide belt conveyor (one of 13 fixed inclined conveyors of varying lengths and widths that carry and stockpile material around the plant), to the primary screening unit, which consists of a Sandvik SS1233H heavy-duty, triple-deck, linear-motion inclined vibrating screen with rubber-lined feed box and wear-protected side plates. Driven by two Self-synchronizing unbalanced 5.5kW electric motors, this dust-encapsulated unit features self-supporting rubber screen elements on the top deck and tensioned steel wire mesh on the lower decks, to deliver the first three product gradings (0–40mm, 40–75mm and 75–200mm).
If necessary, these three products, plus any oversize, can be diverted, via a 20m3 live volume surge bin with Sandvik SP1020 vibrating pan feeder, to the secondary crushing unit for further reduction. A metal detector positioned after the surge bin identifies any metallic elements ahead of the secondary crusher. This crusher, a Sandvik CH440 cone unit, has a throw of 40mm, a closed-side setting of 24mm and features ASRi crusher control technology and a hydraulic setting control system with protection against uncrushable objects.
The output from the secondary crusher is conveyed to and passes through two more dust-encapsulated screens which, between them, deliver the remaining four final products. Both screens are Sandvik SK2162 double-deck, circular-motion vibrating units measuring 6.0m x 2.1m with adjustable inclination. The first is fitted with Sandvik tensioned rubber screen media top and bottom to deliver the 20–40mm product. The second is fitted with tensioned rubber on the top deck and Sandvik tensioned polyurethane screen media on the bottom deck to deliver the 0–6mm, 6–10mm and 10–20mm products.
The state-of-the-art turnkey plant, which was installed in around three months once the foundations had been laid, provides full accessibility for Marshalls staff, with walkways on both sides of all belt conveyors and sloping stairways to platforms around each of the galvanized steel crushing and screening structures.
Looking ahead
Sandvik Mining and Rock Technology took a holistic approach to developing the highly efficient modular plant, working closely with Marshalls to address the specific requirements and challenges on the project, including the site’s small footprint and strict height restrictions.
Sandvik’s ability to meet these requirements and offer practical solutions to the safety and environmental elements of the operation was a major contributing factor to Marshalls purchasing the stationary plant.
‘It was important for us to develop a partnership with the plant manufacturer and to be able to draw on their readily available expertise, backup and support,’ said Andrew Robinson, managing director of Marshalls Minerals. ‘During the tendering process it became clear from an early stage that Sandvik Mining and Rock Technology would satisfy all our requirements. Other manufacturers either didn’t listen or could only supply a standard solution.’
Since commissioning, the processing plant has been performing reliably and efficiently, providing Marshalls with much more control and flexibility over their production and allowing them to increase the output of materials to match demand.
The aggregates producer said it had bucked the trend in the UK aggregates sector by investing in a state-of-art-art fixed processing plant in a quarry, with long-term mineral reserves, that traditionally had production carried out by mobile contractors.
The crushing and screening equipment is expected to provide Marshalls with a speedy return on investment and Mr Robinson is looking to add another bespoke Sandvik plant at Scoutmoor Quarry, near Bury, Greater Manchester.
‘This is a really exciting time for us,’ he commented. ‘At Howley Park, we have invested in a site for the long term which not only supports the expansion of the business, but also strengthens our commitment to the UK aggregates market.’
Mark Bodell said he is delighted to be partnering with Marshalls to provide aftermarket services and support solutions throughout the lifecycle of the processing plant, as part of the Sandvik 365 Services programme.
‘To meet the challenges of the mineral extractives sector, businesses need equipment that operates efficiently and reliably,’ he said. ‘We have invested heavily in strengthening our aftermarket service offerings and Sandvik 365 is an example of the company’s proactive approach to catering for the needs of its customers.
‘It is very important that customers are supported beyond the installation phase and at Howley Park we have set up an ongoing preventative maintenance programme to help Marshalls maximize their production, improve plant efficiency and minimize the risk of downtime. I am looking forward to this being the first of many complete plants that Sandvik will supply to the UK aggregates market.’
- Subscribe to Quarry Management, the monthly journal for the mineral products industry, to read articles before they appear on Agg-Net.com