Cloud Hill Goes Mobile
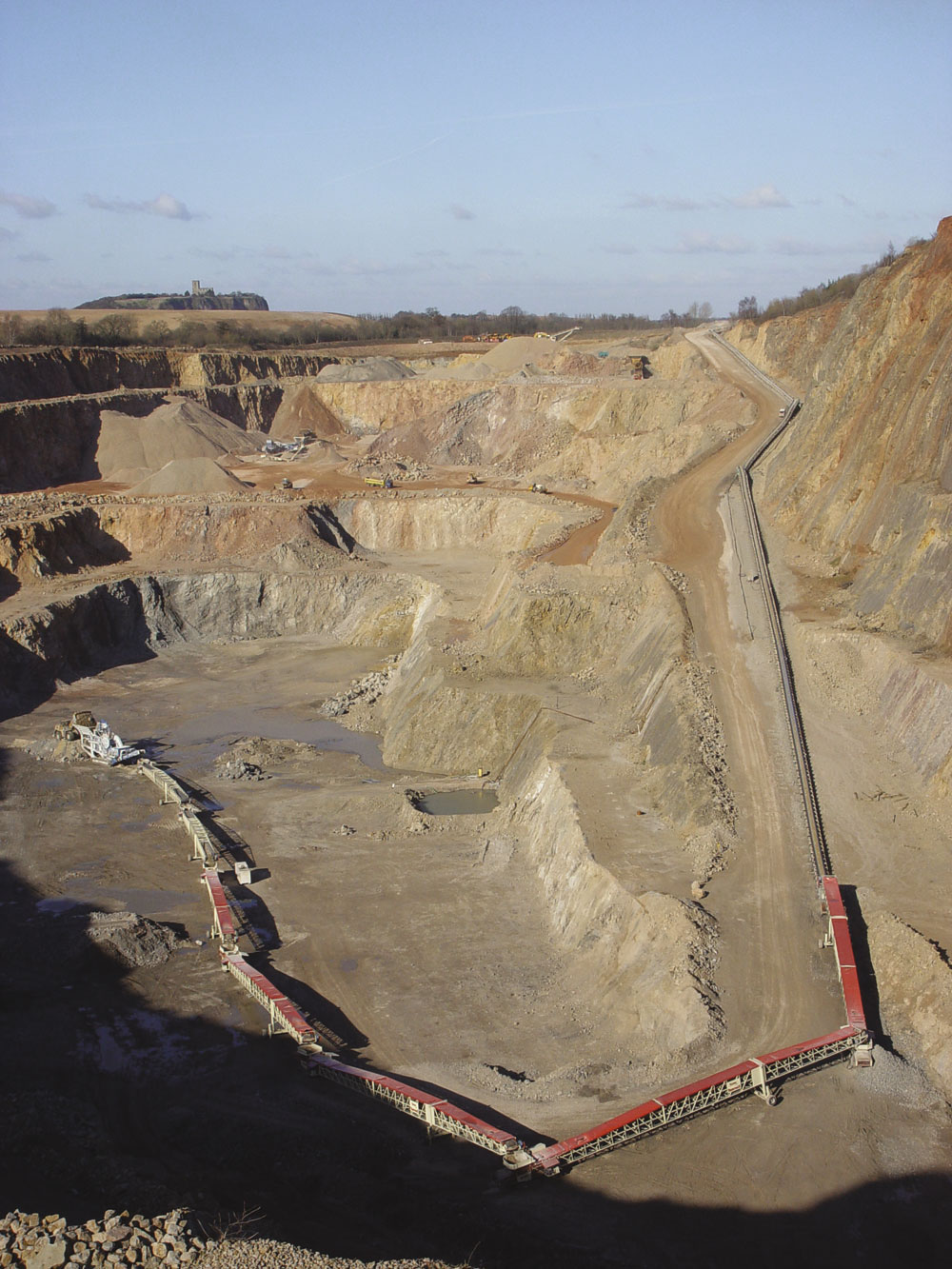
Major investment improves operational flexibility and boosts output at Ennstone Breedon’s largest quarry
Ennstone Breedon Ltd’s flagship Cloud Hill Quarry is situated just a mile away from the company’s headquarters in Breedon on the Hill on the Leicestershire–Derbyshire border, where the rocks of the Lower Carboniferous series comprise a thick succession of partially dolomitised, well bedded limestones. Until the beginning of last year, operations at the site were conducted in a traditional manner with a fleet of four 50-tonne dumptrucks hauling the shot rock up to 2km from the face to the processing plant, where a series of static crushers and screens were used to produce a relatively limited range of products.
Today, however, after a radical redevelopment of the site costing in excess of £4 million, the dumptrucks have been replaced by a new ground conveyor and the former fixed crushing plant has been superseded by a fleet of state-of-the-art mobile crushers, allowing the quarry to supply a much wider range of aggregates throughout the East and West Midlands.
The redevelopment was brought about by a need to increase operational flexibility in response to changes in market demand, as well as a desire to reduce operating costs. Essentially, the quarry’s existing product range was no longer meeting customer requirements, the four dumptrucks were becoming increasingly costly to maintain and the 40-year-old crushing and screening plant was suffering from increasing structural deterioration.
A decision therefore had to made on whether to renovate the existing plant and equipment or to start afresh with a clean-sheet design. With major investment being required in either case, it was felt that this would be an ideal opportunity to make significant changes and improvements at the site, and so a scheme was developed that would eliminate the reliance on dumptrucks and utilize modern processing equipment to better fulfil customer requirements.
The redevelopment plans were approved in January 2003 and work began immediately. The initial challenge was to install temporary crushing and screening equipment to allow production to be maintained while phased demolition of the old processing plant took place. Work then continued for the next eight months with up to eight different teams of contractors working on site at any one time, including lead engineers Robinsons Longcliffe Ltd and Coalville-based B&B Fabrications.
In addition, Ennstone Breedon’s resident electrical engineer, Aubrey Fry, successfully completed the demanding task of re-wiring the entire plant from the mains in, via a newly installed and repositioned transformer. Another particularly challenging role was carried out by civils specialists David Charles (North Wales) Ltd, who supplied and laid over 2,500m3 of concrete, a difficult undertaking involving complex shuttering and the casting of several sections in areas where demolition work was still ongoing.
Despite the challenging nature of the project, which required over 150 different engineering drawings — all of which were produced on time by consulting engineers George Daniel Engineering Ltd, thanks to very careful planning and some key night-time and weekend work at critical stages of the project, not a single day’s production was lost during the eight-month installation period.
Primary stage
Primary crushing now takes place within the quarry itself, with a Caterpillar 988G loading shovel on load-and-carry duty collecting shot rock from the face and feeding it to a 120-tonne Kleemann+Reiner Mobicat MC122Z mobile jaw crusher via the machine’s specially enlarged heavy-duty feed hopper.
Powered by a 327kW Scania engine and equipped with a 500kVA generator, this track-mounted diesel-electric unit accepts a feed size up to 1,200mm x 900mm and delivers a nominal output of 600 tonnes/h. The machine is equipped with a full dust-suppression system to minimize emissions, as well as an integral hydraulic breaker to deal with blockages in the feed hopper or the crusher’s 1,250mm x 1,000mm jaw opening.
All feed material passes through the crusher and is discharged on to the first of a series of innovative tracked/wheeled mobile conveyors which link the primary crusher, wherever it may be working in the quarry, to the tail end of the new ground conveyor at the foot of the main access ramp. To provide full accessibility to all parts of the quarry, a total of seven bespoke link conveyors, each measuring 42m in length and with a carrying capacity of up to 800 tonnes/h, were supplied by Omagh-based Telestack International Ltd. Designed in partnership with Ennstone Breedon, each one is equipped with its own switchgear and electrical connections to allow independent functioning or linked operation in combination with any or all of the others.
In addition, two of the link conveyors are able to draw their electrical power directly from the Mobicat crusher, due to the installation of ingenious power factor correction systems, supplied by Lima International Ltd, which minimize wasted energy and release extra kVA availability, thereby improving motor efficiency and providing significant cost savings for Ennstone Breedon. The remaining link conveyors are similarly equipped, allowing all five to draw their electrical power from a single 250kVA generator, rather than the 500kVA supply that would normally be required for such an arrangement.
The link conveyor system feeds on to a 600m length of 1,200mm wide ground conveyor, installed by belting and conveyor component specialists MES International Ltd, with assistance from Town End Supplies Ltd. This three-section conveyor follows the curves of the access ramp and carries more tonnes per hour up the 1-in-8 gradient than the former dumptruck fleet, but without the ongoing cost of fuel, tyres and labour.
At the top of the ramp the ground conveyor discharges on to the tail end of the primary surge pile delivery conveyor. This passes through a short Armco tunnel beneath an access road before rising to its full discharge height of 25m.
Secondary crushing
Material is recovered from the 6,000-tonne live capacity surge pile by a pair of back-to-back Skako feeders mounted within a concrete reclaim tunnel. One of the feeders discharges on to a covered, 30m long, inclined reclaim belt which feeds the –200mm (8in down) primary crushed product to a mobile secondary impact crusher — a 77-tonne Kleemann+Reiner Mobirex MRB152Z.
Powered by a 398kW Scania diesel engine and featuring a 400kVA generator and full dust suppression, this tracked unit features a highly efficient, fully independent double-deck pre-screen which scalps any –45mm material, this being fed directly to stockpile by a Telestack TS-525 radial conveyor. Meanwhile, the machine’s 1,500mm wide by 1,330mm diameter rotor and highly effective grinding path deliver a nominal output of 450 tonnes/h (90% passing 40mm), which is conveyed to the top of the screen house by a covered, 100m long, inclined belt.
Screening and tertiary crushing
The refurbished screen house is one of the few remaining parts of the original processing plant, although the entire structure has now been rotated through 180° to accommodate the layout of the new plant. On arrival at the screen house the crushed limestone is fed into a Mogensen sizer which splits the material into two streams, one being delivered to a GEC screen that produces 10mm and dust, and the other being sent in the opposite direction to the first of two Hewitt-Robins screens.
This combination of screens caters for the production of a variety of ‘bespoke’ dusts as well as a full range of aggregate sizes (6mm, ‰ 10mm, 14mm, 20mm, 40mm and –75mm +40mm), but with customer demand currently greatest for –20mm products, generally anything larger than 20mm is fed to an in-system Hazemag APSM 1020 tertiary impactor for re-crushing.
Owing to space limitations within the screen house, the feed conveyor to the tertiary crusher arrives at right angles to the impactor’s feed opening. This could have made it very difficult to achieve optimum material distribution across the whole width of the rotor, but the problem has been very effectively overcome by the installation of an innovative vibratory spreader feeder, supplied by Skako Comessa, which receives the material, turns it through 90° and spreads it evenly across the crusher feed opening, thereby making best use of the available space, maximizing crusher efficiency and ensuring consistent blow-bar wear.
Delivering an output of around 150 tonnes/h (some 100 tonnes/h less than its maximum design capacity), the Hazemag unit is powered through an inverter and features a highly effective grinding path. This allows full control of the rotor speed and ensures close control over the percentage of dust produced and the grading of the material, with, typically, 95% passing 28mm and less ‰ than 20% passing 6mm. All tertiary crushed material is fed back on to the main feed conveyor to the screen house in a closed-circuit arrangement.
Stockpiling and load out
The 6mm, 10mm, 14mm and 20mm single sizes currently produced at Cloud Hill are either loaded directly on to delivery vehicles via load-out bays beneath the site’s 11 overhead storage hoppers, or are stockpiled in one of four new 25,000-tonne capacity concrete-walled storage bays by means of a reversible collecting conveyor and an 800 tonnes/h capacity Telestack TS-842 stockpiling conveyor. This versatile radial, telescopic and elevating conveyor keeps the material drop height to a minimum and creates the stockpile by depositing layer upon layer of concentric windrows, thereby reducing dust generation and improving product quality by minimizing material segregation, especially when producing blended products.
The quarry’s two ‘bespoke’ dust products (currently 3mm to dust and 4mm to dust) are stockpiled in parallel 30,000-tonne capacity bays housed within the quarry’s new, fully enclosed dust-storage building. Each dust stream is sent from the screen house to its respective berth via separate fully covered inclined conveyors and dedicated roof-mounted tripper conveyors.
Ancillary operations
The second of the back-to-back Skako feeders located beneath the primary surge pile is used to reclaim excess material, which is conveyed to an auxiliary secondary crusher — a track-mounted Kleemann+Reiner Mobirex MRB122Z mobile impactor. This operates in tandem with a Powerscreen screening unit to produce a –20mm+5mm concrete aggregate.
In addition, an independent Type 1 sub-base production plant operates within the quarry with load-out direct to delivery vehicles from the point of production. This operation comprises a 90-tonne Kleemann+Reiner Mobirex MRB172Z mobile impactor operating in tandem with a 50-tonne Mobiscreen MS20 mobile screener.
Powered by a 430kW Volvo engine and equipped with an 880kVA generator, 1,550mm x 3,500mm double-deck independent vibrating screen, hydraulically controlled inlet box and full dust suppression, the MRB172Z’s 1,630mm wide by 1,330mm diameter rotor delivers up to 700 tonnes/h to the MS20 unit.
Once again, owing to the installation of a power factor correction device, this 139kW Deutz diesel-powered three-way-split screener is able to draw all its electrical power requirements from the adjacent Mobirex crusher, thereby rendering its own on-board 175kVA generator redundant and delivering further cost savings for the company. The screener is equipped with a 6,000mm x 2,050mm triple-deck screen box but uses just two of its three decks to produce up to 700 tonnes/h of –45mm Type 1 sub-base. Any oversize is recirculated back to the impactor for re-crushing in a closed-circuit arrangement.
Just two operatives and two wheel loaders — a Cat 980G and a Volvo L220D — provide maximum flexibility in feeding and loading in this self-contained, in-situ operation, which produces around 4,500 tonnes of Type 1 each day and, according to Ennstone Breedon, is the most efficient part of the entire operation at Cloud Hill.
Conclusion
The recent investment in Cloud Hill has transformed the way the quarry performs and delivered a number of tangible benefits for Ennstone Breedon. Costs have been reduced substantially, making Cloud Hill one of the lowest-cost producers in the region, while at the same time annual production has been increased significantly. In addition, the site has been able maximize the output of better-quality products and minimize the production of waste dust. Moreover, the ability to interchange the various mobile crushers according to changing production requirements, maintenance schedules etc, gives the site an added level of operational flexibility. As a result, Cloud Hill can now look forward to the challenges of the future with a great deal of confidence.
Acknowledgement
The editor wishes to thank Ennstone Breedon Ltd for permission to visit the site and, in particular, Owen Batham, operations director, Jason Lowe, quarry manager, and Ken Harrison, quarry supervisor, for their help in preparing this article.