Wash Plant Delivers Recycling Efficiency For KSD
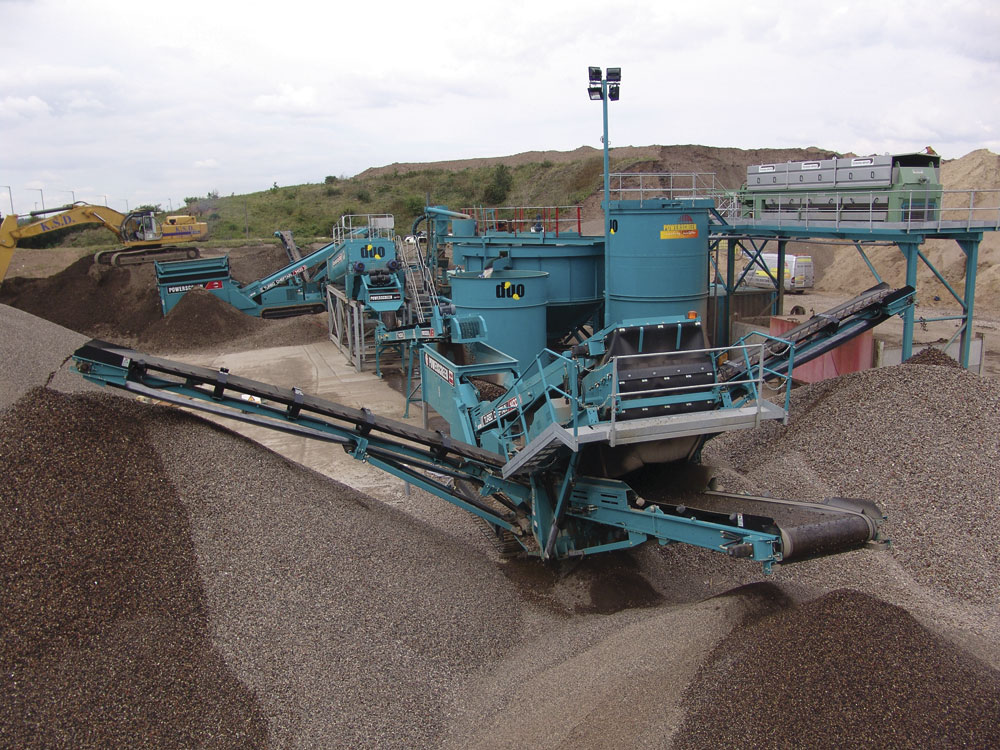
PSWS plant expands markets for West Midlands recycling company
Five years ago KSD Recycled Aggregates, a family owned business with some 35 years’ experience in the supply of haulage for the construction industry, acquired a former landfill site containing approximately 1 million tonnes of construction and demolition waste (CDW) at Coleshill, near Birmingham. For the past four years the company have operated a crushing and screening plant at the 10-acre site recycling imported construction and demolition materials from the local area, but in 2004, with the aid of a government grant and a five-year planning permission, KSD decided to purchase a state-of-the-art washing plant to process the on-site material as well.
Having successfully tendered for the new plant, one of the main problems facing Coventry-based Powerscreen Washing Systems (PSWS) was the lack of water on site (other than a domestic supply), which meant that a closed-loop system was essential. Working within a small footprint, PSWS designed and installed a washing plant that included a complete water-management system from their Italian partners Technoidea.
The wash plant is currently handling 80–100 tonnes/h, with the CDW material recovered from the site being fed by excavator on to the tipping grid of a tracked Powerscreen Chieftain 1400 that acts as the primary screen. This machine features a patented 11ft x 5ft, four-bearing, ‘free-floating’ screen box, which eliminates the need for any fine-tuning. As material passes through the integral screen decks +40mm is fed to stockpile via a folding side conveyor while a direct feed on to a second conveyor delivers topsoil to stockpile. Another folding side conveyor feeds the remaining material to a Powerscreen recycling log-washer.
Capable of producing up to 120 tonnes/h of contaminant-free sand and gravel, the log-washer mixes, mills and washes the incoming feed. Any lumps of earth or clay are broken down during this process and discharged with the wash water, while lighter particles are floated off through specially designed outflow exits on to a 6ft x 2ft trash screen. Two spray bars are mounted at the discharge end of the unit to provide a final rinse.
Material recovered by the log-washer is fed on to an 8ft x 4ft single-deck vibrating part rinser fitted with four sets of spray bars and polyurethane screen modules, before being fed on to a static T4026 inclined transfer conveyor that discharges directly on to the feed conveyor of a second Chieftain 1400. This unit delivers three finished products to stockpile.
Meanwhile, the wash water and fines from the log-washer and final part rinser are fed to a Powerscreen Fines Master 60 static sand-recovery unit for classification and dewatering. Designed for maximum sand grade flexibility, the unit produces around 60 tonnes/h of coarse sand for delivery to stockpile.
As water management was an essential part of the project, PSWS, in conjunction with Tecnoidea, supplied a 47-plate filter press, designed and sized to minimize operator input and maintain low running costs. As well as the press, the system includes a foul-water pump, a GFA automatic flocculent mixing and dosing plant, an SADF sampling system, a 6m diameter dynamic thickener tank with pneumatic discharge valve, sludge and fresh-water tanks, and all the necessary support structures, walkways and access platforms.
According to KSD, installation of the new washing plant has proved very beneficial, allowing them to sell BS-specified –40mm +20mm, –20mm +10mm and –10mm recycled aggregate as well as a general building sand. In addition, the company are looking into potential markets for the dry silt cake from the filter press.
Commenting on the success of the project, site manager Brinder Bullar commented: ‘We are very pleased with the materials that are coming off the washing plant, which are up to the high standards required by the construction industry. Our target was to produce high-end recycled aggregates, which we are doing; the challenge now is to increase our presence in the market and establish recycled aggregates as an alternative in newer markets such as concrete batching.’P