Moore Watson introduce the Hypro-Crush
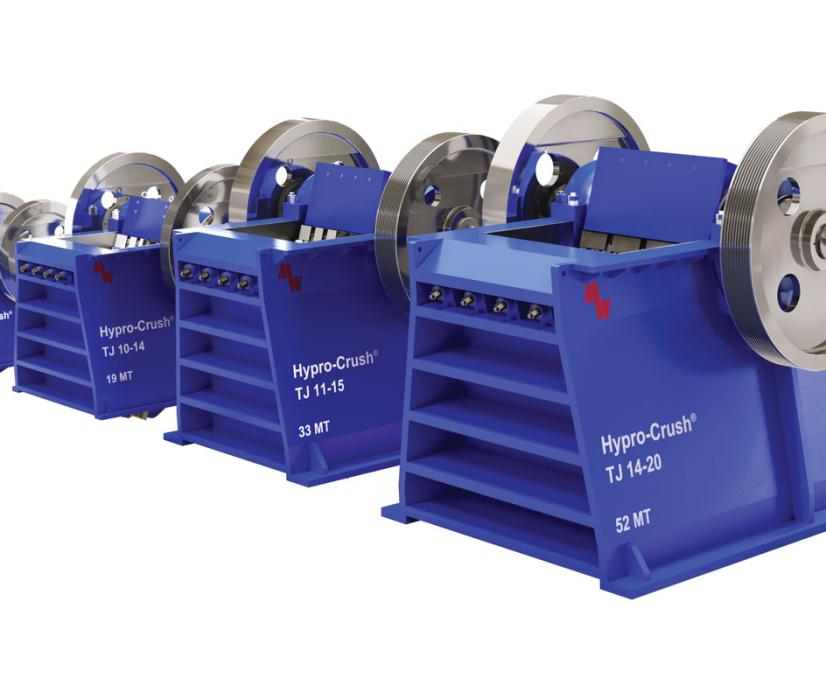
First published in the September 2023 issue of Quarry Management
Company lay claim to the first real and productive jaw crusher development in 164 years
On 15 June 1858, Eli Whitney Blake of New Haven, Connecticut, was granted US patent number 20,542 for a ‘machine for crushing stone’ – a magnificent design that was well-ahead of its time. Since then, apart from small incremental improvements, the same basic design principle has existed in all modern jaw crushers – until now, with the development of the Hypro-Crush.
New Hypro-Crush
The new high-production Hypro-Crush jaw crusher is a new global patent application and development comprising a range of six models for different feed sizes that overcomes the problems inherent with traditional crushers. Due to the Hypro-Crush’s unique design and construction, the first four models to be introduced are commonly used feed size models and cover the spectrum of the full jaw crushing offering of major manufacturers. This has been achieved by using a development which uses less power and weighs significantly less, but still provides the productivity of established large crushers due to the unique designs.
The key development is that the Hypro-Crush is much wider at the bottom than the top, thereby producing a highly efficient design providing the power to crush exactly where it is needed. In effect, the Hypro-Crush is a significantly smaller and lighter machine but has similar production of traditional designs. For example: the Hypro-Crush TJ 10-14 is 1,000mm wide at the top and 1,400mm at the bottom and weighs only 19 tonnes but has the same productivity as a comparable 50-tonne unit manufactured by leading established crusher companies. Furthermore, it only requires 110kW of installed power compared with 200kW of the respective traditional machine. Due to its smaller size, it requires 40% less power to start and run the machine and technical calculations have shown that it will produce in four days what a traditional crusher will do in five or six days. In addition to static installations, the smaller size is expected to revolutionize the development of mobile tracked crushers. The exact production figures and kW requirement for each model will be available after a further stage of testing.
Less of everything
The Hypro-Crush essentially uses less of everything to produce the output of much larger crushers. This delivers major environmental and productive improvements and goes a long way in helping to preserve the world’s fast diminishing resources. As the Hypro-Crush is lighter and smaller, it uses less metal to manufacture, less power to operate, less power to build, less power to run – in other words less of everything but with at least 20–30% more productive capacity. Carbon dioxide (CO2) emissions are significantly reduced both in operations and manufacture. Also, due to the ability to run at a small closed-side setting (CSS) without a loss in production, the possibility also exists to remove a secondary cone from the production process, resulting in less outlay.
Production at least matches traditional larger jaw crushers (or even exceeds them at narrow CSSs) and is maintained due the wider exit for material at the bottom of the crusher. The top feed opening dimensions allow a smaller CSS to be set. This further allows a wider range of CSSs to be used effectively. The Hypro-Crush’s unique convex design wear plates have a ‘belly’ which will spread the material across the crushing chamber to utilize the full width of the lower jaws. A lip on the fixed jaw plate holds the material while being crushed and pushed through by the stroke and lip on the swing jaw plate, whilst tapered grooves located on the crushing wear plates are significantly wider at the bottom than at the top to greatly assist in the flow of material.
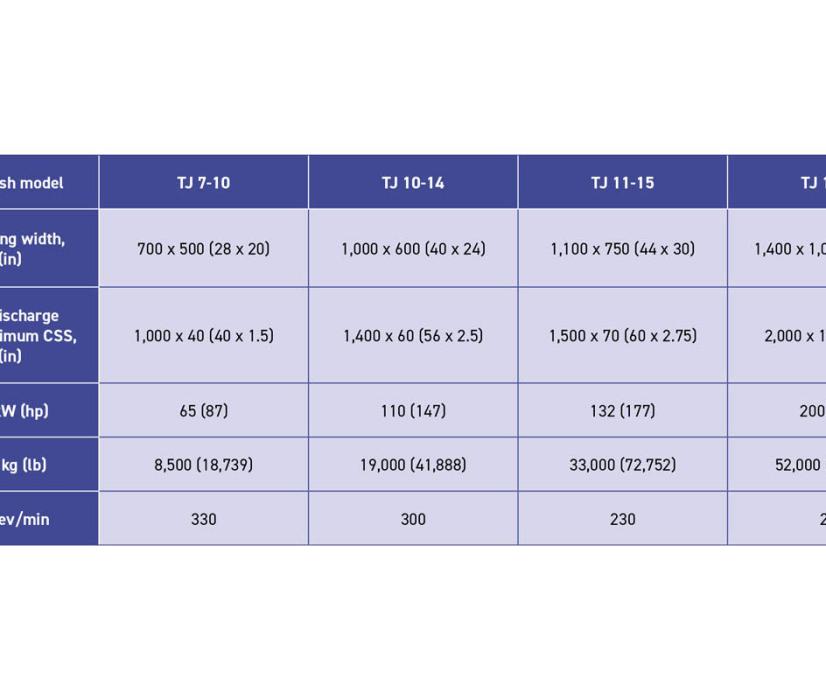
At the heart of the industry
The new design was conceived based on more than 60 years of hands-on global experience in crushing operations by Nicky Watson, who has been at the forefront of crushing operations for over half a century. His know-how has led to the Hypro-Crush, which utilizes many tried and tested features, but with a design geometry that expands the crushing path where it is needed most, thereby increasing crushing capacity without changing the reduction ratio or increasing power requirements. For a given operation, power savings can be made by selecting a smaller lighter (and therefore cheaper) machine for the same operation.
The Hypro-Crush has been designed and developed to not only transform static and mobile crushing installations, but also with a view to delivering sustainability in the mineral processing industry.
In order to deliver the world’s infrastructure, it is essential that sustainable solutions are developed. The Hypro-Crush goes a long way in helping the mineral processing industry meet sustainable and environmental targets through being more efficient, productive, and requiring ‘less of everything’.
For more information please contact: www.moorewatson.com
Subscribe to Quarry Management, the monthly journal for the mineral products industry, to read articles before they appear on Agg-Net.com