DUO deliver dual success for CEMEX
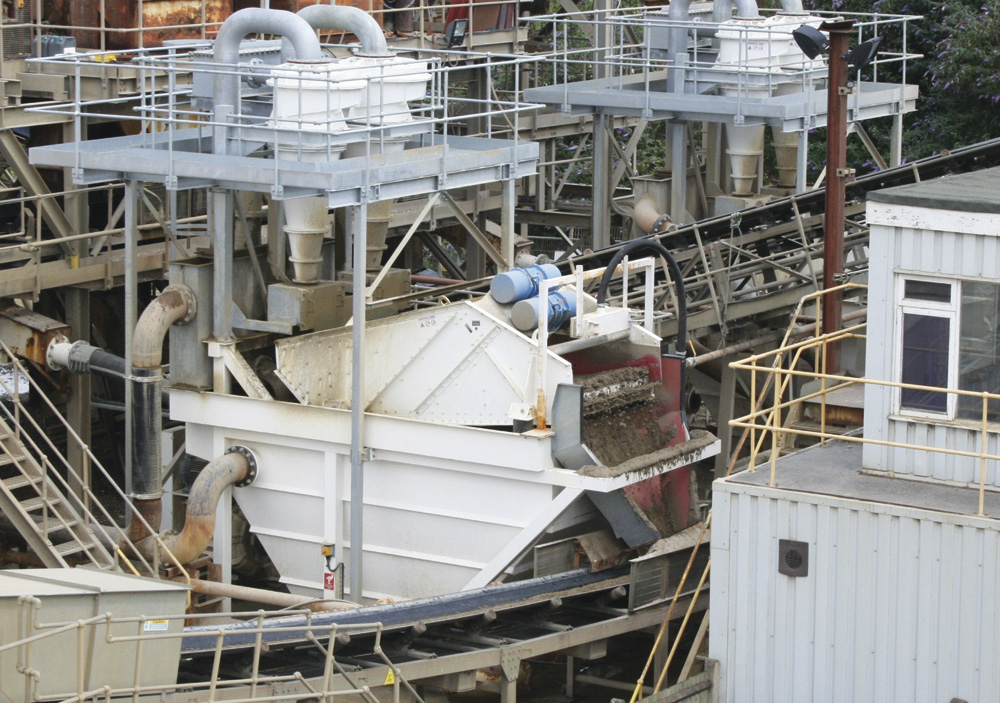
Upgraded sand-processing system for Angerstein Wharf and successful unit-cost processing project at Hatfield Quarry
Angerstein Wharf
Five years ago, when replacing their fire-damaged plant at Angerstein Wharf, in Greenwich, CEMEX took the opportunity to increase the site’s production capacity and efficiency, and to do so utilized DUO’s knowledge and expertise in this area to supply the equipment required to meet their needs. Since then, however, demand for the site’s sand products has continued to increase, so recently DUO’s services were called upon once again to upgrade the site through the installation of two new sand plants.
These new plants have more than doubled CEMEX’s sand-processing capacity at the Thames-side site. Each one operates at a nominal 200 tonnes/h, although both plants are capable handling a maximum of 250 tonnes/h at peak times. DUO designed the feed inlet to deliver an evenly distributed flow to the two plants in order to maximize their efficiency and to provide the total peak output of 500 tonnes/h.
The new sand plants are not only providing a higher output for CEMEX, but also a better-quality end product – delivered through the use of advanced hydrocyclone technology. This technology provides consistent low moisture content dewatering of the product, without the loss of useful fines, and is designed to ensure easy maintenance. The plants receive the –5mm underflow from Angerstein’s two existing Terex Cedarapids horizontal screens and, once processed by the hydrocyclones, the resulting dewatered sand is stockpiled via the site’s existing conveyors, while the waste water is processed for reuse in the washing plant to minimize water consumption and promote sustainability. Access to both sand plants is via fully galvanized support structures equipped with steps and walkways.
Commenting on the new installation, DUO director Fintan Mckeever said: ‘Having installed the turnkey solution that CEMEX are currently operating at their Angerstein site, we were in an excellent position to assist them with this upgrade in terms of understanding the on-site restrictions and their existing operations. The inclusion of the new equipment was designed to utilize the footprint of the sand plants that were being replaced and to work in harmony with the existing plant.’
Glyn Richards, CEMEX’s area operations manager, added: ‘The new sand plants have given the site the ability to significantly increase throughputs and ensure we continue to meet rising market demand. They have been an ideal match for the existing DUO plant.’
Hatfield Quarry
Meanwhile, CEMEX have enjoyed seven years of successful production on a DUO unit-cost processing basis at Hatfield Quarry, in Hertfordshire, which produces approximately 200,000–250,000 tonnes of sand and gravel per annum.
This success has, in part, been attributed to DUO’s expertise in aggregate washing, together with their ability to design bespoke installations capable of meeting production requirements while ensuring adherence to mobility, height and noise requirements, as dictated by planning regulations.
The sand and gravel deposit at Hatfield contains a highly cohesive clay with a 30–40% silt content; a factor that required special consideration during the design of the plant to ensure that the processed material would meet the standards required by CEMEX.
The majority of the washed sand and gravel is delivered to CEMEX’s on-site concrete plant, which is the largest in Hertfordshire, while the remainder is split between an on-site bagging plant and several external concrete plants.
DUO designed the plant to include a prewash, to reduce silt content prior to the fine material being fed to a Finesmaster 200, while the coarse fractions are largely processed via a Commander rinser, a Powerscrub 120R log-washer, a second Commander part-rinser and stockpiling conveyors. The installation also includes a Maxtrak 1000 cone crusher to reduce oversize and maximize concreting aggregates.
As with all DUO installations, the configuration of the plant and day-to-day running processes were both of bespoke design. Material analysis results, production levels and product specification were also taken into consideration at the design stage. CEMEX, having recognized the performance and cost-effectiveness of the installation, subsequently opted to purchase the plant.
For further information visit: www.duoplc.com