Solutions for Improved Conveyor Performance
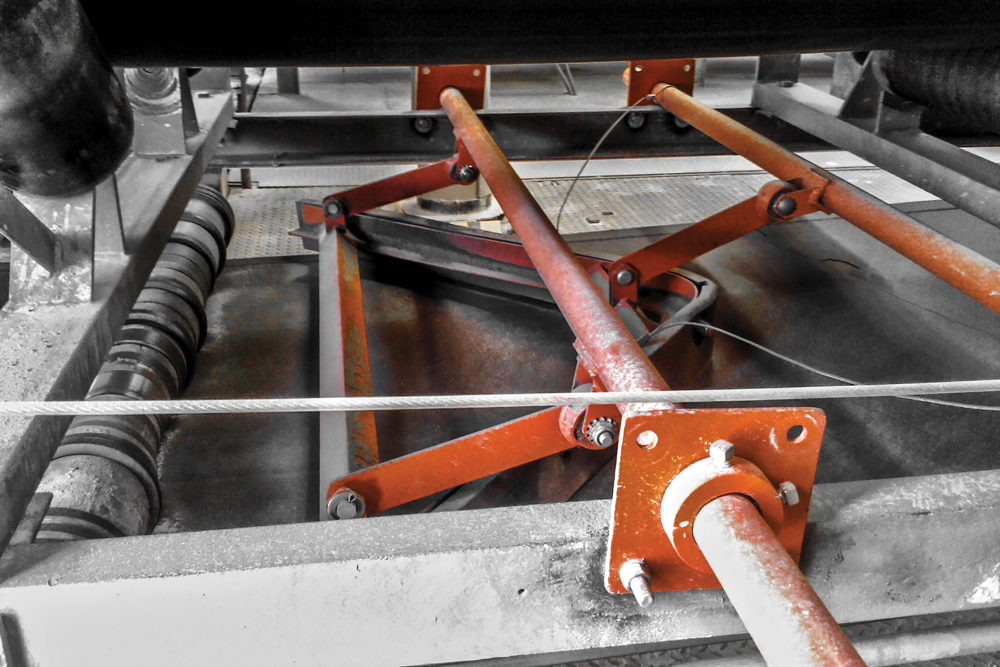
First published in the April 2016 issue of Quarry Management as Removers and Shakers
Martin Engineering offer a range solutions for extending tail pulley life, preventing carryback build-up in conveyor discharge chutes and reducing abrasive wear on metal surfaces
Martin Engineering, specialists in bulk material handling technology, offer a complete line of high-performance components for reducing fugitive material entrapment and improving conveyor tail pulley protection under virtually any belt conditions. The company has designed a family of products to provide consistent blade pressure across the belt plane, producing little wear on the splice, with specific designs for regular and heavy-duty applications, reversing belts and wing pulleys. The result is improved conveyor performance as well as prolonged belt and tail pulley health, reduced maintenance and a safer work area.
‘Bulk material bounces when it comes into contact with a fast-moving conveyor and often shifts as it travels over carrying idlers,’ explained Martin Engineering product engineer Daniel Marshall. ‘These disturbances can eject small amounts of material from the belt. Occasionally, along its return run, the belt will collect lumps of spilled material on the non-carrying side. If these objects are not removed, they can become trapped between the tail pulley and the belt and do significant damage to both.’
Mr Marshall said that when fugitive material is drawn into the tail pulley, one of three things typically happens (and sometimes more than one). ‘In some cases, the belt will fail, suffering high-speed abrasion that results in physical damage to the belt. In other situations, the face of the tail pulley may be gouged, and if material lumps are large and dense, the pulley can actually be forced out of round. Finally, the fugitive material itself may fail, in which case it’s extremely likely to cause belt slippage and mis-tracking.’
Even if none of the above events take place immediately, without appropriate tail protection the fugitive material is simply ejected back on to the conveyor and slammed into the tail pulley repeatedly, until one of the three outcomes does occur. Even small amounts of material can have expensive and even dangerous effects over time.
To combat the damaging effects of fugitive material on single-direction belts, the Martin Torsion VPlow is engineered with a unique spring-loaded suspension system that allows the plough to rise and fall with fluctuations in belt tension and travel. Attached with dual steel crossbars bolted to the conveyor frame a few feet from the tail pulley, the unit is secured by two heavy-duty safety cords. Three torsion arms adjust independently, maintaining consistent pressure for effective cleaning in all stages of blade wear. Effective on standard tail pulleys or wing pulleys at belts speeds up to 900 ft/min (4.6 m/s), the easily replaceable blade delivers 2in (5cm) of wear and can be specified in 60 Shore A durometer nitrile rubber or heavy-duty 90 Shore A durometer urethane.
For less extreme service environments, Martin Engineering also offer an economical solution designed for medium to heavy-duty applications: the Martin VPlow HD, which features a durable 60 Shore A durometer nitrile rubber blade that delivers 2in (5cm) of wear life. Capable of withstanding service temperatures up to 121°C, the design is suitable for non-reversing belt speeds as high as 900 ft/min (4.6 m/s).
For conveyor systems running at faster speeds or carrying heavy loads, the Martin VPlow XHD protects non-reversing standard tail pulleys even at belt speeds exceeding 1,000 ft/min (5.08 m/s), at service temperatures from –29° to 71°C. The heavy-duty half-inch (1.27cm) steel frame construction is said to withstand greater impacts, resulting in durable performance over a long service life, even under the most demanding conditions. The 1.25in (3.18cm) thick urethane side blades deliver 3in (7.62cm) of wear.
Like the VPlow HD, the Martin Durt Dozer Plow is designed to handle standard tail pulleys or wing pulleys on single-direction belts. It sits across the belt at a 45° angle and uses its curved blade to remove fugitive material from the inside surface of belts travelling at speeds up to 700 ft/min (3.5 m/s). The company offers 11 different sizes to accommodate single-direction belt widths from 18in (45.7cm) to 96in (243.5cm).
For tail protection on reversing belts, the Martin Diagonal Plow is a straight-blade design, hung from brackets on both sides of the conveyor. The device floats on the surface of the belt to remove spillage, without the need for adjustment. The durable 60 Shore A durometer nitrile rubber blade delivers 1.5in (3.8cm) of wear at service temperatures up to 121°C and belt speeds up to 900 ft/min (4.6 m/s).
In addition to belt speeds and service temperatures, Dan Marshall recommends that specifiers of tail-protection products inspect the intended mounting points prior to any purchase. ‘A V-shaped plough will eject material from both the left and right sides of the belt,’ he said. ‘In some locations that can make clean-up difficult. In applications where the conveyor is up against a wall or underground, for example, a diagonal plough that sends all of the cleaned material to one side may be more beneficial.’
He added: ‘We designed these products to retain the pressure needed to adequately protect the tail pulley. As with all of our component designs, they’re engineered to deliver long life and ease of service, with minimal maintenance requirements.’
Vibrating dribble chute
Martin Engineering have also developed an innovative solution that prevents carryback released by secondary conveyor belt cleaners from sticking to the rear slope of the discharge chute. If left to build up, material can encapsulate secondary cleaners and deposit harmful carryback on to the return side of the belt, fouling idlers and pulleys. The Martin Vibrating Dribble Chute uses material disruption to cause tacky sludge and fines to fall from the chute wall and back into the main discharge flow.
Prompted by customer requests, Martin engineers observed that the majority of the build-up released by secondary cleaners collected at the rear of the chute mouth, where a sloped surface can trap carryback. Product engineer Dan Marshall said: ‘We discovered that this could happen with nearly every discharge chute conveying adherent material. In some cases, even chutes treated with a low-friction coating can experience build-up. It’s only with the persistent disruption from vibration that we found materials flowed consistently.’
Comprising three parts – a low-friction polyurethane dribble sheet, a steel mounting bracket and a powerful vibrator, the combination of mechanical disruption and the slick surface prevents material from adhering and feeds it back into the main discharge flow. When the unit is mounted into the existing chutework, it often extends the rear configuration closer to the belt, increasing the amount of material captured and further reducing spillage.
To install the dribble chute, first a slot is created in the rear sloped wall to accommodate the steel hook bracket that secures the entire unit to the chute. Lined with thick, soft rubber on the inside arch to protect the chute from structural abrasion caused by constant vibration, the J-shaped bracket holds the dribble sheet secure with four bolts. Capable of being field-modified to fit the width and length of any chute with the necessary belt clearance, a thick and rigid sheet of abrasion-resistant, ultra-high molecular weight (UHMW) polyethylene is installed in an elevated position parallel to the chute floor, so the sheet is free to vibrate.
Bolted to the other side of the bracket, outside the chute, is a unit from the extensive family of Martin electric vibrators, chosen to meet the needs of the application. Rated for continuous duty even when set at a maximum force output level, the units are housed in a totally enclosed, non-ventilated (TENV) case to keep internal components protected from abrasive dust. The electric rotary motor can be as large as 230–460V, three-phase, 50/60Hz and can run as fast as 3,450 rev/min at a centrifugal force output of up to 16,500 pounds (7,484kg). Internal Class-H windings are triple dipped, shock resistant and able to operate under sustained internal temperatures as high as 180°C.
Bulk materials ranging from coal to cement have unique adherent qualities that can cause them to stick to any surface. If left to collect and migrate along the return side of the belt, a bulk material will foul idler bearings and pulley surfaces throughout the whole system, which could cause issues such as mis-tracking, belt slip and accelerated belt wear. To clear these build-ups, workers often need to reach in or, in some cases, enter the chute, which could pose a hazard and may also require a confined-space entry permit. A vibrating dribble chute helps eliminate the need for these potentially risky maintenance procedures.
‘We sought to design a simple and effective solution that only needs periodic pressure washing and is safer and more economical than the alternative – digging out equipment with shovels,’ said Mr Marshall. ‘Less downtime and fewer maintenance hours results in a lower cost of operation, and, over the long run, promotes a safer workplace.’
Wear-resistant metal alloys
To help reduce abrasive wear in chutes, hoppers and other metal surfaces, Martin Engineering have introduced a wear-resistant fused alloy plate that can withstand more abrasion than other protective metal linings. With a bi-metallic design, Martin Arcoplate combines a smooth and dense chromium carbide-rich metal alloy face plate with a hard steel back plate to resist gouging, erosion, temperature extremes and material build-up. Installed on surfaces exposed to abrasive conditions, it is said to increase protection for longer equipment life with less frequent maintenance.
‘Materials with a large amount of silica can be very abrasive, accelerating wear on metal surfaces,’ commented Andrey Leonardo Ribeiro de Miranda, application engineer at Martin Engineering. ‘Applications in which materials are extremely abrasive or hot also damage equipment, chutes and containers. When an unprotected metal surface structure is reduced in thickness over time, it runs the risk of sudden breakage or buckling. Over the long run, clients have found that prevention is far more cost-effective than regular maintenance and replacement.’
Engineered to withstand the harsh conditions of mining and quarrying applications, Arcoplate offers a solution to both excessive wear and material accumulation issues for chutes, hoppers, dumptruck beds, excavator buckets, front-loader shovels, and other bulk-material equipment in need of protection. The bi-layer construction is tailored to the thickness, composition, shape and polish specifications of the application. Very low residual stresses allow it to withstand severe impact forces and bending.
Made with a chemical composition of iron, carbon, chromium, manganese and silicon, Arcoplate is currently available in three grades: Alloy 1600 is designed for high-abrasion and high-impact applications; Alloy 1040 is engineered for moderate impact and cyclic temperatures up to 500°C; while Alloy 8668 is suitable for extreme temperature applications up to 700°C. Each derives its high abrasion resistance from the very hard M7C3 carbides (1,500–1,800Hv), with an average of 60% carbide dispersed through a softer, tougher matrix.
‘Greater hardness does not always mean greater abrasion resistance or longer wear life,’ explained Mr Ribeiro de Miranda. ‘Bulk hardness tests like Rockwell or Brinell measure the average hardness of both the carbide and matrix together. Conducted over a relatively large area, test results can show the same hardness rating as conventional metals, but performance tests show that a carbide-containing surfacing alloy has substantially better wear resistance.’
According to manufacturers Alloy Steel International, based in Malaga, Australia, the top layer leads the industry in having the highest percentage of evenly dispersed hard carbides, resulting in the best resistance to both low- and high-stress abrasion. However, when determining which alloy grade to use for specific applications, company experts say that high bulk-hardness ratings are not the only determining factor.
Abrasion resistance depends on a combination of both hardness and the metallurgical microstructure of the alloy. Normal hardness is determined by three tests: the Vickers Test (Hv); the Rockwell Scale (Rc); and the Brinell Scale (BHN). Although hardness is one factor in determining the wear life of the plate, thickness has to be factored into an extended operational life too.
As the only wear plate available with a total overlay thickness greater than 14mm, the alloy top layer is manufactured 4–20mm (0.16–0.79in) thick, and the steel base plate 7–11mm (0.27–0.43in) thick. Proper thickness is determined based on the material being handled, weight allowance and spatial restrictions of the application. Molded with computer precision, each plate thickness and shape is adapted to the equipment form with no weld beads to interrupt material flow, thus minimizing turbulence and abrasion.
Surface smoothness, uniform hardness and carbide distribution are critical to overall wear plate performance and its ability to avoid build-up that could lead to clogging and excessive weight. When faced with consistent abrasion, a rough surface finish will experience erosion 200–600% faster than a smooth surface of the same alloy structure and hardness. All grades of Arcoplate can be manufactured with finishes rated ‘standard’, ‘polished’ or ‘ultra non-abrasive’ to avoid material hang-up and carryback, and the grain can be fitted in any direction to match material flow.
‘Laboratory and field tests confirm that our specially engineered alloy will outlast quenched and tempered wear plates by a factor of up to 6:1 and conventional welded overlay plate by 2:1,’ said Mr Ribeiro de Miranda. ‘Clients who have installed Arcoplate have experienced less build-up and slower surface erosion, leading to better structural integrity and longer equipment life. Some have also reduced their labour costs, as workers spend fewer hours removing stuck material and servicing damaged components.’
For more information visit: www.martin-eng.com