Abrasion-resistant steel from Tata Steel
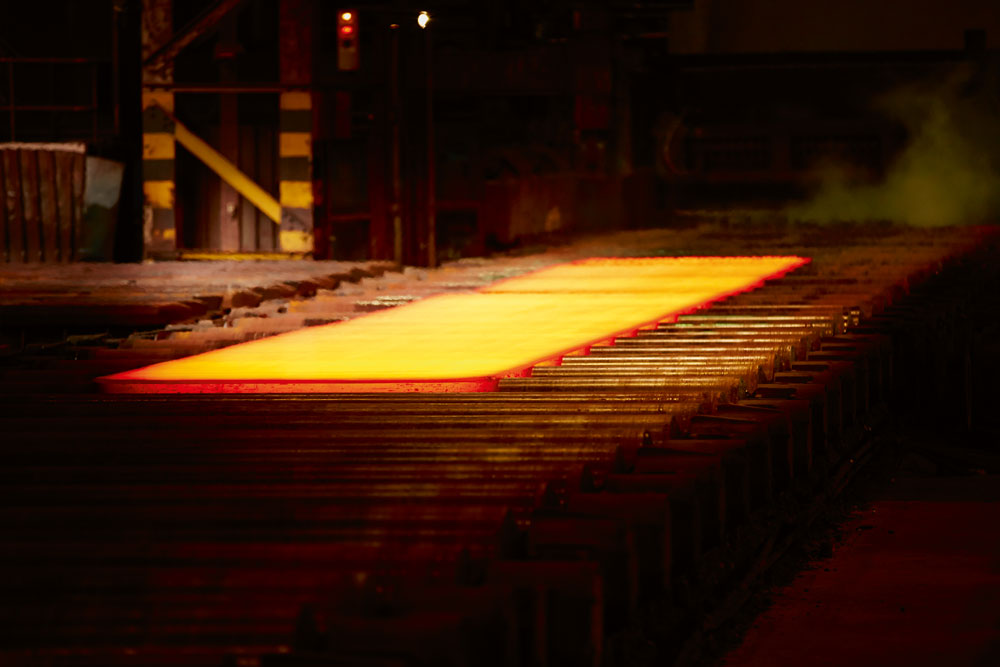
First published in the October 2013 issue of Quarry Management as Conveying in a Cold Climate
Abrazo abrasion-resistant steel offers a solution for arduous material-handling applications in harsh environments
It is hard to think of many environments that are tougher on conveying equipment than quarrying. With large volumes of highly abrasive materials handled every hour, the equipment used to shift these materials from face to stockpile has to withstand serious punishment. The key in such situations is abrasion resistance.
Within conveying equipment there are certain areas that take more punishment than others, such as high-impact zones, and this is where truly abrasion-resistant products are needed. Not many grades of steel can withstand this level of abuse, but Abrazo, Tata Steel’s roller-quenched and tempered abrasion-resistant steel is specifically designed for applications where high strength and toughness are essential.
Used in a variety of wear-dependent applications, Abrazo is particularly suitable for bucket reclaimers and conveyor parts. Available in 400, 450 and 500 BHN wear plate grades, the Abrazo product range also features guaranteed toughness grades.
According to Tata Steel, the wear life of Abrazo is two to three times greater than the conventional steel used in the conveyor structure. As with all construction equipment, productivity, and hence profits, are determined largely by keeping machines running efficiently and continually. Downtime is expensive, so having a belt which can keep running for longer, with lower maintenance, even in these tough conditions, is essential.
But a highly abrasive environment is not the only factor that Abrazo must contend with. The nature of quarrying also tends to lend itself to colder, harsher climatic conditions too. Abrazo maintains its high-impact toughness at temperatures down to –40°C; with both the 400- and 450-grade plates designed to operate in the coldest environments.
Colin Mawdsley, customer technical service engineer at Tata Steel Lifting & Excavating, explained what makes Abrazo so versatile: ‘Compared to rivals’ roller-quenched steels, Abrazo is highly resistant to wear yet remains easy to work with. Higher grades of steel are available but are generally less easy to weld, which ultimately pushes up production costs. Abrazo 500, the strongest in our range, is resistant enough to withstand such harsh environments, but is still flexible enough to be processed.’
One example of Abrazo’s suitability to different applications is in bucket reclaimers. ‘Here, the 450 grade is best. Weld overlay or cast-tile alternatives just aren’t flexible enough for this kind of application,’ explained Mr Mawdsley.
Due to the recently increased finished plate width of 3,200mm, Abrazo 500 can be welded in larger plates instead of using tiles with a cross-over. This means larger components can be produced in one piece, reducing the number of potential welds and simplifying the manufacturing process. This naturally reduces the cost, and increases the strength of the product.
Abrazo works so well in conveying equipment because it has evolved through Tata Steel’s close working relationships with customers in the sector, with their needs and feedback in mind. Like the rest of Tata Steel’s range, Abrazo can be tailored to the needs of its global customers, to give quarry operators optimum performance in service and all the benefits they have come to expect from the quenched and tempered and Abrazo product range. Tata Steel work with their customers’ advanced engineering teams from the outset on the design and development of new products and models, to optimize the design, manufacturing and materials.
Tata Steel strengthened their offering of Abrazo abrasion-resistant steels in 2011, with an £8 million investment at their Clydebridge plant. This followed a £10 million investment at the company’s Dalzell plant in August 2010. The Clydebridge investment has improved Tata Steel’s range of plate products, which are suitable for demanding wear applications in the aggregates industry. The investment included the expansion of the plant’s two furnaces and the installation of two gas-cutting machines and a stamping and marking machine, boosting the output of this specialist plant to 3,200 tonnes a week.
Part of the recent investment has seen a new heavy-plate press installed at Dalzell, increasing the volume of heavier plate produced and improving final plate flatness, which is now better than EN10029 special flatness tolerances. The new production process also provides better traceability for products, thanks to an automatic stamping and marking system, allowing easier identification of material. The final plate product can be supplied in the as-processed, shotblasted, or shotblasted and primed conditions, as required by the customer.
‘There are a lot of good competitors, but Tata Steel are committed to ensuring their products remain the best option in such applications,’ explained Colin Mawdsley. ‘The Clydebridge plant specializes in producing difficult-to-make high-strength steels used in some of the most challenging environments around the world, and the benefits of increasing our capability at Clydebridge on maximizing the value of the steel plate we make in the UK is already in evidence.’
For further information visit: www.tatasteeleurope.com
- Subscribe to Quarry Management, the monthly journal for the mineral products industry, to read articles before they appear on Agg-Net