The Future of Quarry Management is Now
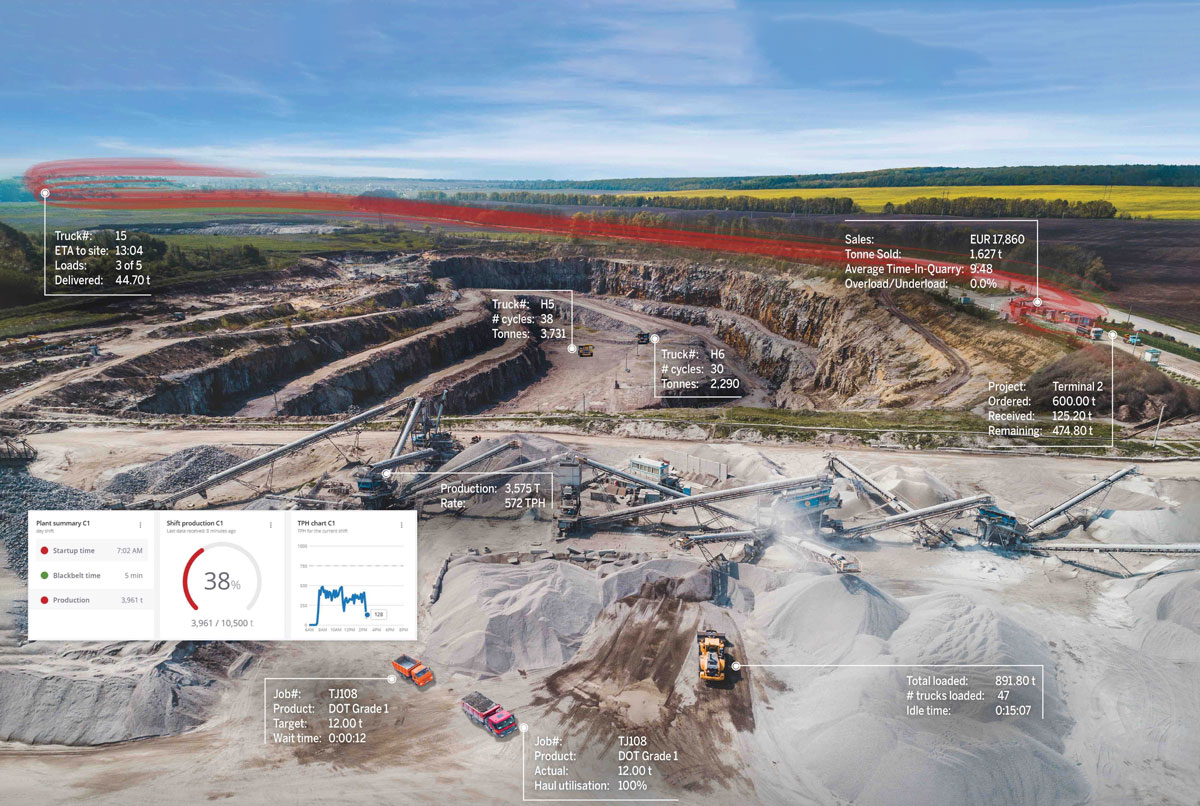
First published in the June 2021 issue of Quarry Management
Windows of opportunity for operational improvement by Kevin Vonesh, worldwide strategic account manager, Trimble aggregates
From autonomous drilling and conveyor belt sensors to truck fleet management and aerial volume measurement platforms, quarries and aggregate production plants are creating virtual stockpiles of data.
However, while these data-producing systems are helping drive productivity for boots on the ground, they are typically not connected in a way that can help support operational objectives. Nor are they able to resolve challenges including rising production demands, tighter specifications, employee recruitment and retention, and safety and regulatory compliance.
The only way to address these concerns is through improved process management. At its most basic, quarrying is a three-step manufacturing operation – extraction, material processing and loading, and much like any manufacturing activity, Lean and Six Sigma techniques allow the identification and removal of waste and minimize impact variability. As many operations have learned, you cannot improve what you cannot measure.
Nevertheless, despite the ongoing investment in systems such as belt scale sensors and fleet management, managers do not have an easy way to compile data about specific operational activities to derive actionable insights.
The connectivity conundrum
Tracking material production, equipment productivity and personnel performance is considerably easier in today’s environment with so many sensors – however, gaining valuable intelligence from all this data is trickier, and something that the entire construction industry struggles with.
In the 2019 ‘Big Data = Big Questions for the Engineering and Construction Industry’ report, FMI, a consulting firm that tracks overall construction trends, found that 95.5% of all data captured goes unused and an estimated 13% of a project team’s working hours are spent looking for project data and information. The problem is a lack of connectivity between solutions – a challenge that quarry managers and aggregate producers will increasingly face.
Much like a project manager relies on an overarching solution to bring together progress data from a job site, quarry and aggregate producers should begin to think about quarry workflow-relevant reporting tools and dashboards. These reporting tools draw data from sensors and systems on loaders, excavators, haul trucks and conveyor belts into a centralized location, where they are organized into valuable intelligence. By measuring data from load and haul, processing, load-out processes and stockpiles, a producer can quickly see what is produced and isolate any opportunities for improvement.
A reporting tool such as Trimble Insight gathers and sorts data and then incorporates key pieces of information (depending on the user) into real-time dashboards to support decision making and production planning. By measuring loadout and processing totals, a producer can see what is produced and isolate opportunities for improvement.
For instance, a large aggregates producer installed Loadrite belt scales to help crews manage production. Pulling belt scale data, including product type, production rates and locations, into a single source helped the producer show target versus actual productivity and identify downtime delays.
In another case, an aggregate operator wanted a report on blast yield tonnage to verify that blasting patterns and hauling cycles were delivering the expected yield. That report was pulled together with data from belt scales and machine monitoring systems.
Similarly, another producer is using sensor-derived data to decide if he needs another wheel loader or a different class of machine to keep up with production while minimizing capital investment.
Operational realities
The ability to monitor operations is bridging the gap between intuition and hard data. A reporting tool confirms and reinforces an operator’s expertise, providing information in a manner that is accurate, timely and easy to visualize.
Since the Trimble Insight tool is connected to scales across the operation, it can provide valuable insights from extraction to load out. It is a single source of truth. With such a system, a producer can quickly see how improving a certain aspect of operations – such as adding new equipment – improves production or the bottom line.
A quarry production monitoring system allows information in real time to highlight an opportunity that could minimize lost production time or reduced performance. It is an opportunity to look through a different set of lenses – in essence, a direct window into operations at any given moment along with the historical data to drive actionable decisions – and it is information that is available anytime, anywhere from a connected device.
Many sites already have the hardware infrastructure in place – it just needs to be connected to an intelligent reporting system, and there are specialists that can advise and assist with connectivity, such as Halomec, the UK authorized dealer for Trimble Insight. For more information or to try the Trimble Insight demo, visit: www.trimble.com/insight; or www.halomec.com
- Subscribe to Quarry Management, the monthly journal for the mineral products industry, to read articles before they appear on Agg-Net.com