The Art of the Possible
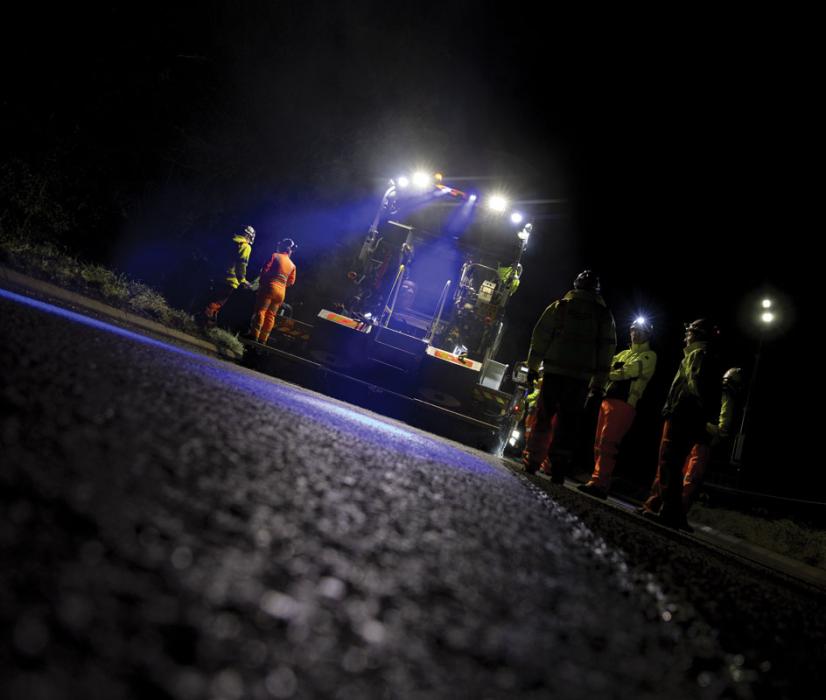
First published in the January 2024 issue of Quarry Management
A blueprint for low-carbon roads by Brian Kent, technical director, Tarmac
Against the backdrop of a climate emergency, the global effort to cut carbon emissions has never been more prominent or, indeed, necessary. No industry is exempt from the changing attitudes towards sustainability and the challenges of driving carbon reduction.
In a sector like highways with a complex supply chain, carbon savings must be driven by a customer’s commitment to sustainability and collaborative working from partners across the supply chain at every stage of a project.
That is the theory. It is easy to say but more difficult to execute in reality. At Tarmac, we have been clear with customers and partners across the highways industry that collective behavioural change is key to delivering environmental savings.
A partnership to deliver change
Last summer we started to talk to Hartlepool Borough Council and Stockton-on-Tees Borough Council to discuss the art of the possible and consider what it would take to deliver a resurfacing project which could deliver significant carbon savings and potentially set a blueprint for other projects on the local or strategic road networks.
The result of this fantastic partnership with both local authorities has been a project which has reduced the carbon emissions of three road schemes in the North East by up to 80% compared with projects using traditional methods.
Working in collaboration with the councils together with international partners including Shell, Volvo CE, Wirtgen, and JCB, we combined an extensive range of low-carbon materials, techniques, and plant equipment for the very first time to resurface a section of the A689 in Wynyard, near Hartlepool, and two residential roads in Stockton-on-Tees Borough.
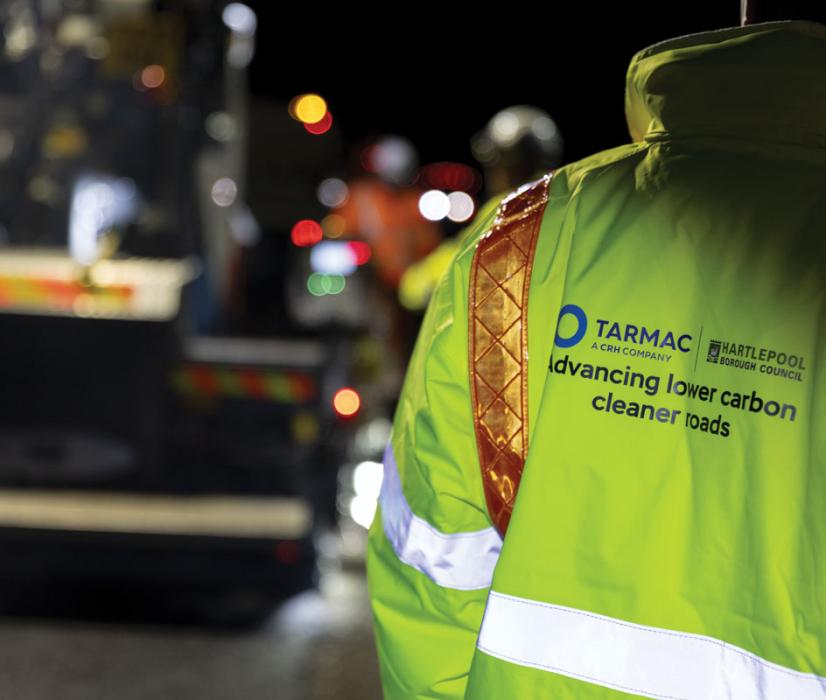
Turning the environmental dial
Proportionately, the largest contributor to the significant carbon reductions on this project was the materials used and the transport and manufacturing of them. Warm-mix asphalt, a standard product for Tarmac that reduces the carbon emissions required to heat the materials, was used which contained recycled asphalt planings (RAP).
While using recycled road materials is not a new concept, the commitment across project partners to delivering the best possible carbon reductions led to 20% RAP being used, compared with a standard 10% in surface course, with 30% in the binder course.
The project also used an innovative carbon-sink bio-binder bitumen supplied by Shell which contains bio-components and thereby locks carbon within asphalt road surfaces, preventing it from being released into the atmosphere and effectively creating a carbon sink.
The binder has previously been successfully trialled in schemes across England, using a version containing a biogenic carbon of up to 250kg carbon dioxide equivalent per tonne of bitumen. However, for this project a prototype version was used containing higher quantities of bio-components than previously used (with up to 375kg carbon dioxide equivalent per tonne of bitumen), showing what can be achieved through persistent innovation.
Leading global partners on the project, such as Volvo, supplied electric vehicles including HGVs, road rollers and a bond-coat sprayer. Some plant vehicles were also powered by hydrotreated vegetable oil (HVO) as a sustainable alternative to diesel. The use of these vehicles led to a 99% reduction in the carbon emissions of the on-site road construction and zero carbon emissions from the transport of materials to site.
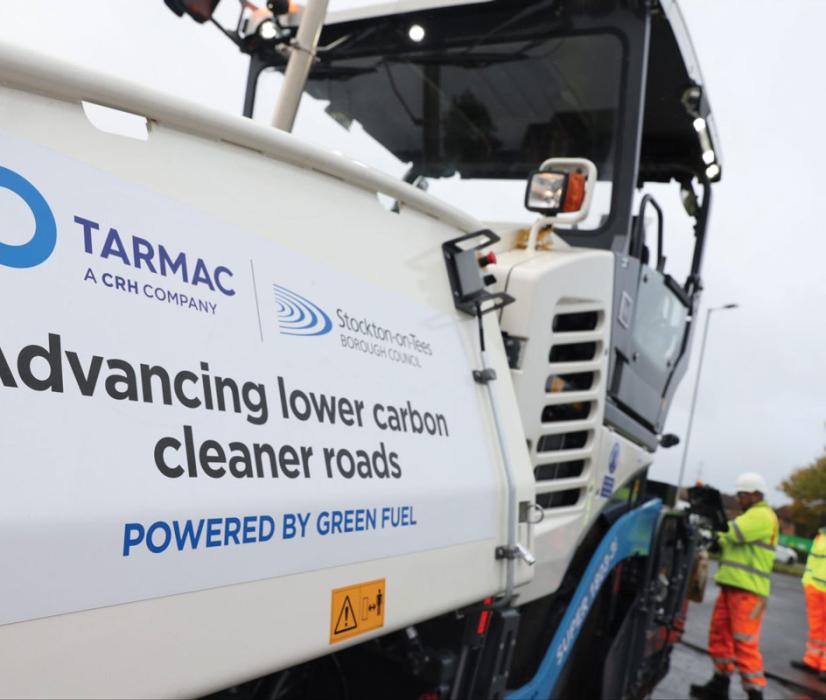
Is this possible everywhere?
Through this ground-breaking road resurfacing scheme, Tarmac’s project team was able to prove the art of the possible in highways innovation.
This project is a clear example of what can be achieved when all partners in the supply chain commit to sustainability goals and bring forward their best and brightest carbon-saving recommendations. By mobilizing every available resource, innovation, and technology, we have laid the blueprint for what could be delivered on projects across the UK.
This begs the obvious question: why not take this approach on all highways projects going forward? The answer to this is underpinned by the challenges of supply and demand. On this project we used a ‘prototype’ approach, utilizing every possible avenue of low-carbon innovation. However, many of these elements are not yet readily available at a commercial scale, due to higher costs, or are in the early stages of development.
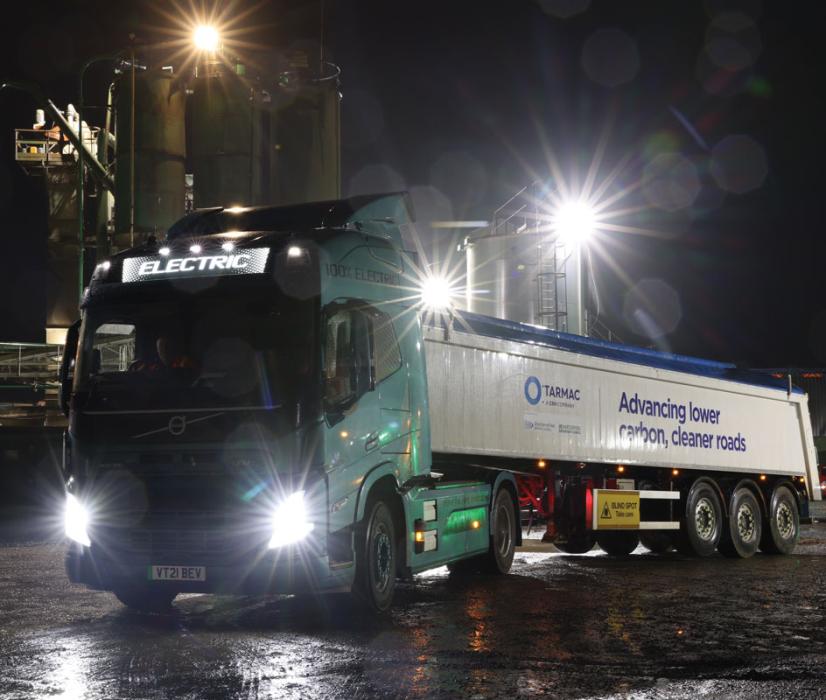
It is now important that we take learnings from this ground-breaking project to help inform further decarbonization decisions across the local and strategic road networks.
To replicate this approach on every project will require further investment and scaling up of technology across the industry. However, to move towards low-carbon working, we need to collectively review how these sustainable options are procured.
The highways industry will only be able to scale up when there is confidence and certainty that there will be a demand for these low-carbon options from clients and asset owners. We need to reach a scenario where sustainability is valued alongside price and quality in order to significantly turn the decarbonization dial on highways projects. This project in the North East has shown the art of the possible because of forward-thinking councils and innovative supply chain collaboration.
Subscribe to Quarry Management, the monthly journal for the mineral products industry, to read articles before they appear on Agg-Net.com