Bitumen Storage
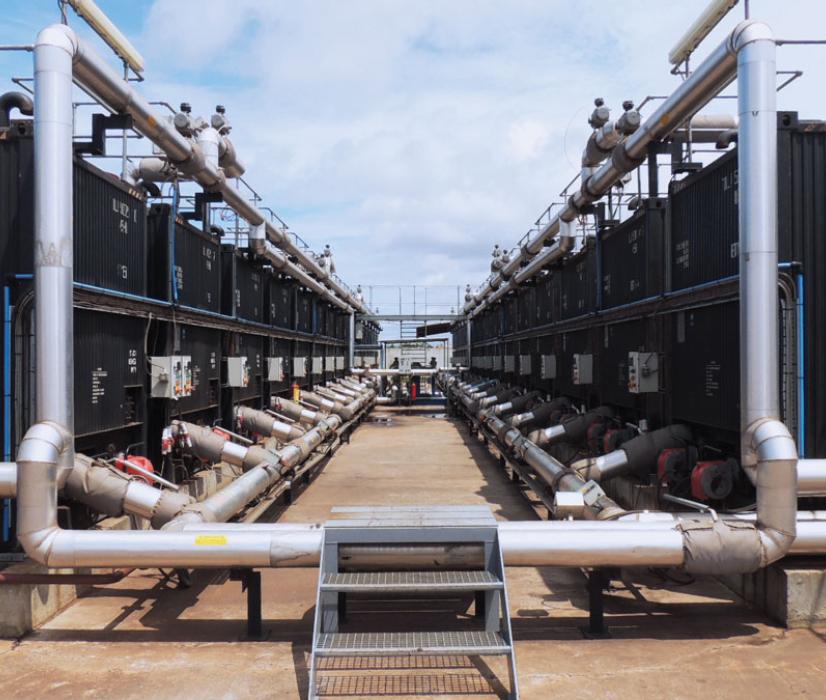
First published in the July 2023 issue of Quarry Management
The growing demand and opportunities for 2023–24
By Jon Whittall, managing director, TEC Container Solutions
Why is there a growing requirement for bitumen storage? In answer to this question, there are several factors causing a shift in the supply dynamic of the bitumen market. One that has been well documented is the multiple refinery closures and restructures, which has put stress on the logistic chain that supports the industry.
Trucking operations from refinery to end user are now often much longer, increasing demand for operators and drivers. The trucking industry is failing to meet this demand, with the International Road Transport Union estimating a current shortage of drivers of close to 400,000, with that number likely to triple by 2026 if no action is taken. Consequently, this has put stress on the logistics chain and disruptions can be frequent, directly affecting asphalt production at end-users’ plants.
The solution to this is to increase the number of bitumen storage locations, reducing the long-distance trucking operations and creating buffer storage that stabilizes supply against this increasing unreliability.
Solution: How the market can address this demand
The industry has reacted by building new large-scale storage terminals in key locations. Some examples of this are in France, South Africa, and the UK. These terminals allow for bulk vessel imports from further afield to secure supply for the relevant local markets and benefit greatly from economies of scale.
However, it is crucial, that we address new challenges with new solutions. In locations lacking large import terminals, or the space to build them, ship-to-shore loading gantries can be utilized to discharge small-to-medium-sized vessels into trailer tankers and bitumen containers that can subsequently unload into inland storage, or in the case of containers, be used as storage themselves. By unlocking new vessel import opportunities, the market will benefit by decreasing the reliance on long (and increasingly expensive) trucking logistics.
Inland storage facilities are also required to react to this demand, working in sync with the larger-scale import terminals. For end users located a significant distance away from the coastal sources, this stabilizes the supply logistic with a buffer of product. These inland points do not need to be as significant in size as the larger import terminals, but can be smaller, strategically located and, therefore, more bespoke. These terminals would also greatly benefit from being of a scalable and even relocatable nature, such as that shown in fig.1.
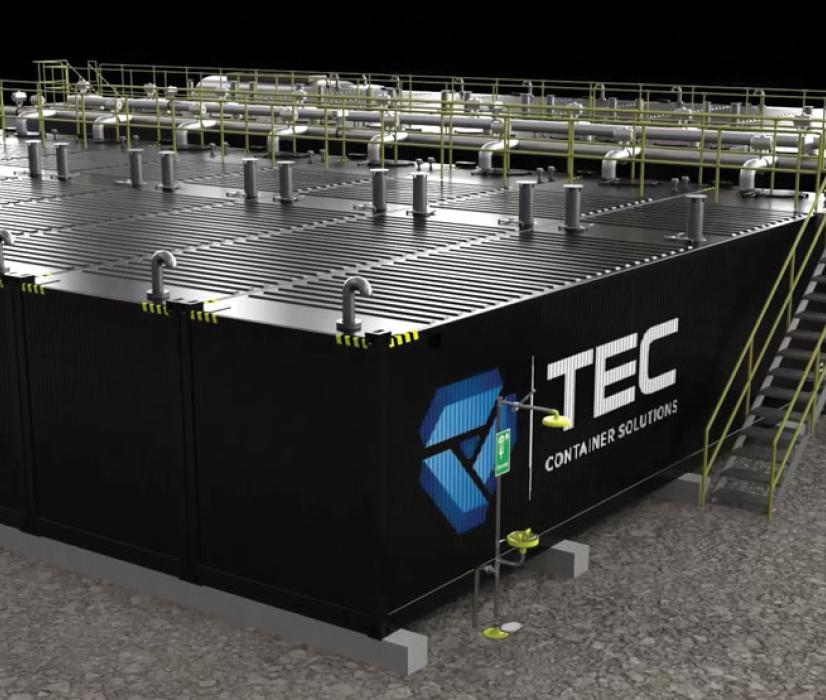
Logistics: the operation required to facilitate storage
Fully integrating the different types of storage (eg coastal terminals, inland facilities, modular storage etc) is key for taking on the new challenge presented to the industry and this can be achieved through a robust logistics chain.
It is clear from the above that new bitumen vessels are required, and more specifically suitably sized vessels for various regions. The demand for small-to-mid-sized vessels is an issue, with markets looking to import smaller cargoes of 3,000–10,000 tonnes. Currently, no new bitumen vessels are on order, so this is not an issue that will be alleviated anytime soon unless demand subsides.
In other areas, it seems there are two main requirements driving the decisions to transport bitumen – flexibility and efficiency, the former being driven by increased uncertainty and ongoing shifts in the supply chain and the benefits of not being stuck in only one channel, and the latter being driven by the growing focus on reducing both costs and the environmental impact of logistics.
This has caused a notable increase in Bitutainer (and other bitumen container) usage. Being fully intermodal gives the operator opportunities to react to the most cost-effective mode of transport at the time, whether that is via vessel, truck, rail, or barge. As an example, the supply issue with trucking outlined above coupled with rising fuel costs (diesel, which used to make up 30% of transport costs, now makes up 50%) has meant the price of trucking has increased heavily. Conversely, container freight rates have fallen significantly, meaning a switch in the supply routes, where possible, can be advantageous. Additionally, this method can provide an on-site cold buffer storage as well as a medium for hot product delivery.
Bags are also being utilized in some markets where the logistic and often labour-intensive decanting operation can be incorporated, as they too offer a level of flexibility in operations, allowing customers to use them as on-site storage when needed.
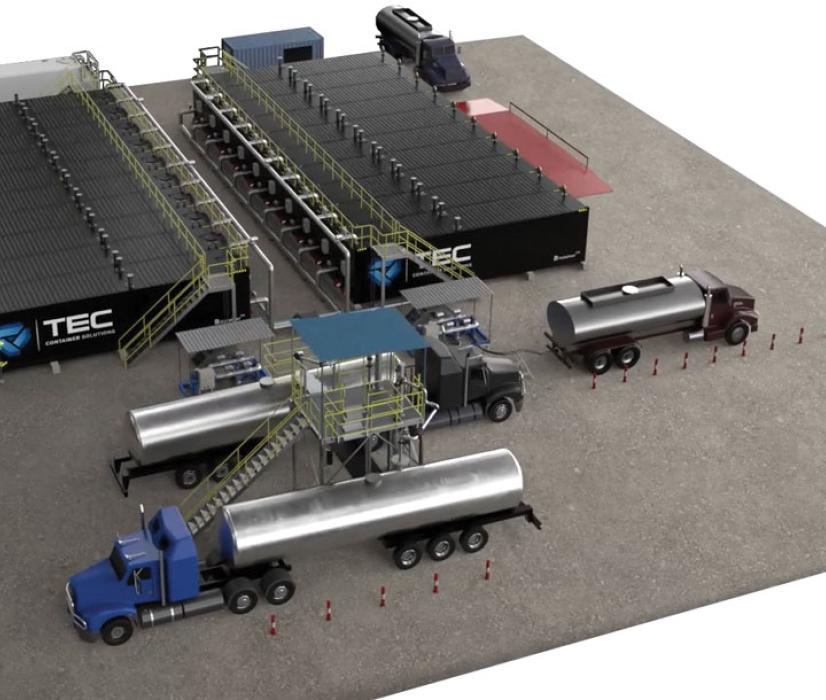
The importance of sustainability-focused storage technologies
The construction industry, in which road building is incorporated, is responsible for approximately 38% of gross annual carbon emissions worldwide.
Although bitumen can be considered as a sustainable product, due to recycling and the fact that the molecules are not burnt for energy, the transportation and the way in which bitumen is stored all contribute to the final carbon footprint of a road construction project.
For storage applications, the first aspect to consider is the amount of energy required to heat (or maintain) the bitumen at the necessary temperatures. This involves ensuring that the heating system is designed for maximum efficiency, by designing the heater tube configuration for maximum transfer with minimal wasted energy.
Where that energy comes from or how it is produced is also important. The use of more sustainable fuels for burners and boilers, such as Biodiesel or electricity generated by renewable energy sources, is increasingly a focus when discussing new storage applications.
Perhaps the most important aspect, particularly when looking at temperature maintenance, is for storage tank manufacturers to focus on minimizing heat loss from the tanks. New developments in insulation methods and redesigns to reduce heat sink points have been made over the last few years, greatly improving tank efficiency.
Finally, it is essential that the storage system is designed for the level of throughput intended. For large storage tanks, high throughput is important to reduce the long-term cost per tonne of heating. If tanks are left maintaining the bitumen at high temperatures for significant periods, this becomes an inefficient way to heat the bitumen.
For times of low throughput, it may be better to allow the product to cool and heat it only when required. This method is well suited to a modular scalable solution, such as the Bitutainer storage facility, where tanks can be isolated so only what is required is heated.
How quickly different solutions can be implemented
Terminals are being built as quickly as possible to meet demand, however, this can be a lengthy process. Finding the land and obtaining permits and permissions needs to happen prior to a shovel touching the soil. Bitumen storage is not high on the preferential list of port space owners and, therefore, this can be a challenge. Construction is also a significant project, heavily affected by the reliability and availability of manpower and resources, both of which have been stretched recently.
Intermediary Bitutainer storage provides a fast build time, allowing companies to be agile and to react to where the market demand is. The scalable nature of this solution also allows for the implementation of storage to be completed incrementally as the demand grows in new regions.
Subscribe to Quarry Management, the monthly journal for the mineral products industry, to read articles before they appear on Agg-Net.com