Wear protection points the way forward for cement producers
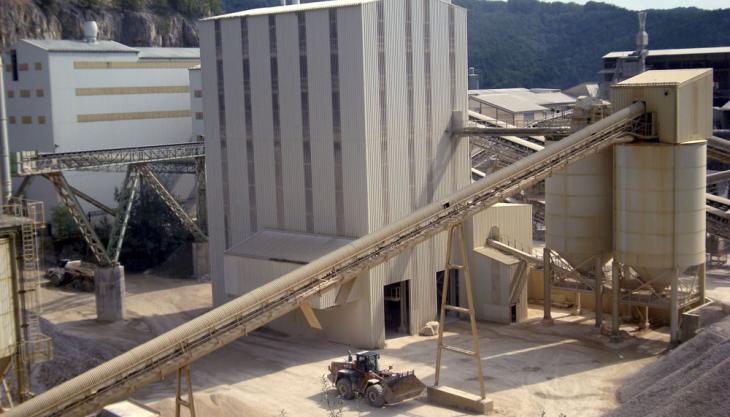
Kingfisher Industrial discuss ways in which cement producers can reduce maintenance costs in a climate of reduced global demand
A recent report into the options available to cement producers, against a background of reduced global demand, identified five key objectives that producers should focus on if they are to optimize their businesses and achieve reduced total production costs. The objectives are:
- Increased use of waste fuel materials
- Reduced material costs, using lower cost materials where possible
- Reduced manpower
- Increased efficiency in the process, and reduced maintenance
- Reduced energy costs.
Upon first consideration, the scope and scale of these objectives would not appear to lend themselves to a one-size-fits-all solution. However, four out of the five can actually be achieved via one specific process - wear protection. This is the process of coating or lining process plant and equipment, such as cyclones, valves, bunkers, pipework, chutes (et al), with ceramics, metallics or polymers to extend their life. In many instances, the benefits of protecting plant are threefold - as well as protecting against wear and extending plant life, the low friction nature of the lining material reduces energy usage and increases production by allowing a greater volume of material to be throughput.
In addition to its many operational advantages, a key benefit of wear protection is that it can be employed at any time in the life of a process system, so users do not have to throw away their existing plant and start again. However, if a system is designed with wear protection from its inception, then overall equipment costs can usually be reduced compared to retrofitting.
Material costs can also be reduced in the rest of the system, as the wear protection can often remove the requirement to manufacture components using heavier grades of material. Take a pipeline, for example. If a wear protection lining system is used, then the user can specify thinner walled pipe because the lining will provide the protection. This could mean 5mm wall thickness for the pipe rather than 10mm, with a commensurate 50% saving in steel cost.
This downsizing is possible because the pipework becomes a carrier for the wear-resistant lining, the synergy of the two meeting the requirements for pressure, temperature and wear protection.
In addition, because high conveying speeds and abrasive materials cause wear of varying intensity at different points in cement handling systems, it is often the case that protection need only be applied to areas of plant that are most vulnerable to wear, further reducing upfront costs and improving ROI for the system user.
Kingfisher Industrial, specialists in wear protection across all types of industries, have calculated that, on average, users of their wear-protection systems benefit by a factor of five times their initial outlay, with many installations providing wear life of up to 20 years following appropriate wear treatment.
This figure is significant because it means cement producers get greater utility from their plants, avoiding the downtime and halts in production resulting from the requirement to provide maintenance and repair of equipment at regular intervals, due to problems associated with wear and erosion. Reduced maintenance also means reduced risk, reduced cost, reduced maintenance personnel and more production uptime over longer periods – all of which are critically important to improve the efficiencies of companies in competitive markets.
A process plant that is equipped with a well designed wear-protection system also offers a number of incidental cost-saving benefits. Because pipework no longer has to be broken down for maintenance at regular intervals, no specialist labour is required, avoiding the safety risks of personnel working at height, performing hot work and lifting operations.
Also avoided are the tasks of organizing access platforms and plant hire, with their attendant costs – and risks; and those of devising clean-up procedures for any spillages that can occur when process pipework is perforated. As a result, the system user benefits from continuous operational gains that defray the cost of the protection system, guaranteeing a prompt return on investment.
The value of using wear protection in cement production was evidenced recently at a UK cement plant that was experiencing increasing downtime with a dense phase conveying system. The vast area of the plant meant that output from the mills had to be carried some 500m through a pneumatic pipeline, some parts of which were underground and had several sharp bends.
The line carrying cement powder in a dense phase state of conveyance weighed about 20.5 tonnes and carried cement at 28m/sec through a small radius bend. Bends inevitably give rise to hammer and distortion of pipelines over time, and the abrasive cement powder rapidly destroyed the more vulnerable areas. In a plant designed to work continuously throughout the year, any unscheduled downtime was very expensive.
The underground section was particularly troublesome, making damage identification and pipe renewal difficult and time consuming. Normally the cement producer would only close the factory for two weeks each year for maintenance, but the pipeline was so vital to continuity of production that any work necessary on this area could easily stop the plant for longer periods.
The requirement to ensure continuity of production meant that any replacement system would need to be installed with minimum disruption, be manufactured off-site and delivered as a kit of parts. In addition, elimination of the product hammer problem, significant reduction in wear rates of the pipes, with a projected 10-year service life, and improved access for inspection and maintenance, were also critical elements of the specification.
After a period of research and preliminary design, the cement company considered a number of potential suppliers, eventually selecting three companies that were invited to place competitive sealed tenders for the work. Finally, the customer chose Kingfisher Industrial to manufacture the system in partnership with his own consulting design engineers.
Using their extensive experience in offering solutions associated with conveyance of abrasive solids and fabrication techniques, Kingfisher chose Schedule 40 carbon steel pipe work reinforced at vital points with K-BAS liners, a re-crystallised cast basalt rock product, which offers extreme hardness and abrasion resistance. The new system incorporated large radius bends (10 x bore diameter), followed by 1m straight extensions downstream to counter turbulence, and was designed to aid the smooth flow of cement powder and reduce abrasive forces.
All elements of the system (lined pipework, trestles, towers and bridges) were manufactured in Kingfisher's purpose-built factory in the West Midlands and delivered to site for final assembly. Kingfisher appointed their own engineering team, consisting of a site engineer with qualified riggers and fitters, to undertake the erection process.
As the site was in operation during the build process, and there were many vehicle movements in the area, Kingfisher also had to manage and monitor the movements of mobile cranes and powered access equipment, due to the risk associated with the possibility of collision. Placing 15-tonne towers accurately on their foundations, and then assembling long lengths of complex bridges and pipe work with great precision using mobile cranes, was no easy task, but one that was completed on time and within budget.