Reinventing the wheel
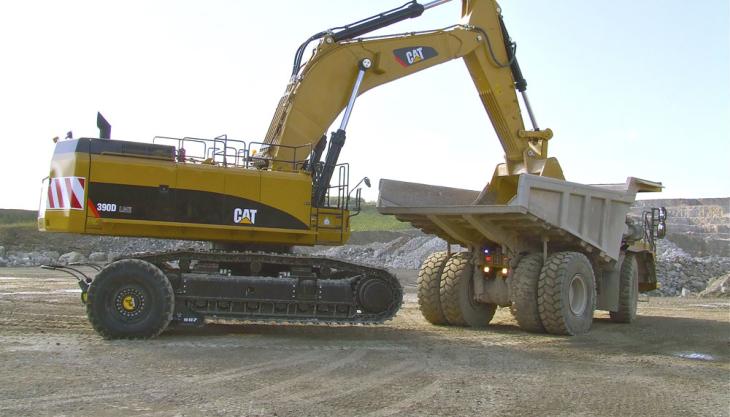
Finnish-built transportation system helps Lafarge overcome health and safety issue at Hope Quarry
DURING 2010, Lafarge Cement UK’s 328ha cement manufacturing site at Hope, in Derbyshire, was presented with a health and safety challenge which required a novel solution that is unique in the UK.
The site at Hope is divided into three areas: the works and batching plant, which cover 63ha; a 109ha shale quarry; and a limestone quarry that covers a further 156ha.
The limestone quarry operates 12 benches, each measuring 15m in height, covering three geological periods of Carboniferous limestone, all of which have to be worked simultaneously due to differences in silica content.
The silica content is high in the top benches, extremely high in the middle and low at the bottom. As a result, there has to be a constant mix of material for use in the cement production process.
The Health and Safety Executive insisted that as each bench was processed, the faces should be dressed as well. The only practical and economical solution was to use an excavator to load out the blasted material and to dress the benches as works progressed.
‘Although we have great faith in our local Finning account manager, Dean Turner, we pointed out that any excavator required to travel around a quarry of this size with such regularity would run up huge undercarriage repair and maintenance costs and would prove uneconomical,’ said Lafarge’s deputy quarries manager Colin Reid. ‘But then he showed us a video of a transportation system and our scepticism turned to intrigue.’
Finning’s excavator solution came in the shape of a Cat 390D ME excavator fitted with a 3.4m stick and 6.9m Smart Boom. To move the 90-tonne machine around the site, Finning further recommended the addition of a Sleipner 970 transport system – a pair of heavy-duty, double-wheeled dollies that fit on the excavator tracks.
The Sleipner system allows the excavator to drive on to the dollies (idler first) releasing the automatic braking system. The excavator then slews around and lowers its boom into the back of a dumptruck, using the bucket as an anchor and effectively turning the excavator into a wheel-mounted trailer that can be towed around the site at around 10 times the travel speed of the excavator under its own power.
Once on station, the excavator operator simply raises the boom, releasing it from the dumptruck, and drives off the Sleipner wheels.
Although the Finnish-developed Sleipner system is used extensively around the world, Hope Quarry is the first example of its use in the UK, and the culmination of a protracted approval process that took more than 12 months.
Finning even took a representative of the Health and Safety Executive to a quarry in Germany to see a Sleipner system in action, a move that ultimately convinced the HSE of the system’s efficacy.
The system is built to accommodate 30-, 50-, 70-, 90-, 100- and 120-tonne machines on a four-wheel system, and 190-, 250-, 310- and 400-tonne machines on Sleipner’s original eight-wheel version.
According to Sleipner export and marketing manager Nichole Beyer, the system is simple to use and has a payback time of less than six months. ‘Customer experience around the world has demonstrated an average 5% increase in productivity, but where most companies make real savings is in the reduction of undercarriage wear,’ she said.
‘Most excavators will go through three sets of tracks in a lifetime. At more than £50,000 per set, there are significant cost savings to be made if equipment owners can safeguard those tracks by using our system.
‘But the repair and maintenance advantages do not end there,’ she added. ‘Traditionally, an engineer would have to carry out repairs in the field because it would be too time-consuming to drive an excavator back to the workshop. Our system means that the machine can be returned to the workshop in a fraction of the time, protecting the engine and hydraulic lines from the ever-present threat of dust contamination associated with open-air repairs.’
Lafarge’s Colin Reid is already convinced of the Sleipner system’s operational benefits. ‘I would readily admit that our initial feeling towards the Sleipner system was one of scepticism,’ he said. ‘But after using it a few times during training, all of our operators said they liked it. And while it’s still early days, the system has already significantly reduced face change times and had a positive impact on our productivity levels.’